-
- News
- Books
Featured Books
- pcb007 Magazine
Latest Issues
Current IssueInventing the Future with SEL
Two years after launching its state-of-the-art PCB facility, SEL shares lessons in vision, execution, and innovation, plus insights from industry icons and technology leaders shaping the future of PCB fabrication.
Sales: From Pitch to PO
From the first cold call to finally receiving that first purchase order, the July PCB007 Magazine breaks down some critical parts of the sales stack. To up your sales game, read on!
The Hole Truth: Via Integrity in an HDI World
From the drilled hole to registration across multiple sequential lamination cycles, to the quality of your copper plating, via reliability in an HDI world is becoming an ever-greater challenge. This month we look at “The Hole Truth,” from creating the “perfect” via to how you can assure via quality and reliability, the first time, every time.
- Articles
- Columns
- Links
- Media kit
||| MENU - pcb007 Magazine
Estimated reading time: 6 minutes
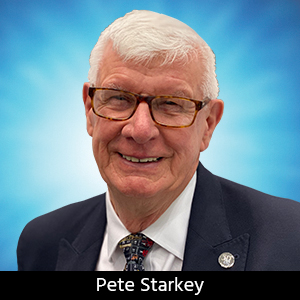
Contact Columnist Form
An Inside Look: High-Temperature Electronics Manufacturing
“High temperature electronics is not just about solder, it’s about all of the parts that make up an electronics product. Substrates, components, connectors, cables, solders, and assembly processes all need to be considered. ‘High temperature’ generally means between 150°C and 200°C, but there are many applications where electronic assemblies have to work at temperatures up to 300°C. These hostile operating conditions are typically found in aerospace, automotive, and petrochemical industries,” said Bob Willis as he introduced SMART Group’s webinar on High-temperature Electronics Manufacturing. The presentation covered a broad topic, but a comprehensive programme and a team of the industry’s leading experts held the attention of a substantial audience for over three hours.
An overview from Finbarr Waldron, laboratory and project manager at Tyndall National Institute and chair of SMART Ireland, put a clear perspective on the challenges presented by high-temperature operating environments. He began by considering reliability. Under normal conditions, the customer needed confidence that a product would perform its task correctly for a reasonable lifetime, with a minimum of warranty or product liability issues or repair costs. In the high-temperature environment, the product would be exposed to extreme conditions, the application could be safety-critical or mission-critical, a long operating life would be expected, and maintenance and repair might be impossible.
He discussed high-temperature device materials such as silicon carbide and gallium nitride, metal and ceramic packaging, high-temperature die-attach materials, high-temperature interconnecting substrates: Polyimide and ceramic and assembly methods based on high-temperature solders and solderless systems.
With a series of examples, he demonstrated conditions typical of industrial, automotive, avionic, and space applications. Oil drill-head sensors operated at 170°C under extreme vibration and high pressure. Automotive applications required a 10-year working life with engine-bay temperatures potentially cycling between -40°C and 150°C, together with vibration, mechanical shock, and corrosive conditions. Lambda sensors saw temperatures in excess of 300°C. Aircraft systems were safety-critical with 25-year operating life expectancy in exceptionally harsh environments, particularly in engine monitoring systems.
The ultimate in reliability was prerequisite for electronics operating in the space environment: Devices for scientific measurement, guidance, propulsion, and a host of sensing and monitoring operations. “You only get one shot--you don’t get the chance to go back and fix it!” Typical conditions were temperatures ranging from -65°C to +150°C, vibration up to 50G at up to 2 KHz, pressure change from atmospheric to vacuum, heavy radiation, and electromagnetic interference. Waldron’s research group at Tyndall National Institute was developing test methods for evaluating components for the BepiColombo mission, due to set off in 2015 on a seven-year journey to Mercury where it would endure temperatures in excess of 350 °C.
Dr. Chris Hunt, leader of the Electronics Interconnection team at the National Physical Laboratory, focused his presentation on interconnects operating at temperatures close to and above the melting point of conventional solders, and explored potential high-temperature interconnect solutions including conductive adhesives, sintering, transient liquid phase soldering, and carbon nanotubes. Few lead-free solder alloys were available for operation above 200°C, and tended to be far too expensive for all but the most critical applications. An example quoted by Dr. Hunt was a gold-tin solder paste at £16,000 for 500 grams!
There is growing interest in sintered metal interconnects for high-temperature electronics. Silver for example did not melt until approximately 970°C, but nano-particle silver powders could be sintered at temperatures of 250°C and below by solid-state diffusion, and attain properties close to those of the bulk metal. Pastes were becoming commercially available which could be printed then dried to remove solvents before being raised to sintering temperature. Silver pastes could be used for die-bonding where high-temperature resistance was required, and copper pastes could be used for forming conductors. National Physical Laboratory was a partner in the ELCOSINT project, developing materials and manufacturing processes for electronic component interconnection using nano-silver based materials to replace high-lead solders.
Carbon nanotube technology shows great potential for future development of high-temperature interconnection. Multi-wall carbon nanotubes offere remarkable electrical conductivity and heat resistance, and a method has been established to grow them as “forests” in area arrays by a photo-thermal chemical vapour deposition process using acetylene as raw material. The process is compatible with CMOS manufacture and could potentially be incorporated into a wafer-fab to grow multi-wall carbon nanotube arrays directly on to CMOS devices. A major challengeis to establish a reliable technique for attaching terminated devices to interconnecting substrates, and work continues on the development of characterisation tools.
Dennis Price, quality director at Merlin Circuit Technology, added a PCB fabricator’s view to the proceedings, with a discussion on high temperature laminates and solderable surface finishes. He listed the many parameters to be taken into consideration when determining the suitability of a laminate for a high-temperature application: Glass transition temperature, decomposition temperature, Z axis expansion, maximum working temperature, and interconnection stress test performance, as well as T260 and T288 performance, solder float survivability, thermal cycling performance, CAF resistance and moisture absorption.
From the designer’s standpoint, the maximum continuous operating temperature of a laminate was a critical factor, although this was difficult to quantify. He suggested that the UL relative thermal index (RTI) was a good starting point, in which data from an a series of accelerated ageing evaluations is extrapolated to give a temperature at which the material will operate for 100,000 hours and retain at least 50% of its original physical or electrical properties.
The most popular laminate choice for high-temperature applications is polyimide-glass, with typical parameters: Glass transition temperature 260°C, decomposition temperature 380°C to 420°C, and maximum continuous operating temperature of 210°C. The material has a tendency to chip during drilling and profiling, and moisture absorption is a significant issue. The ultimate high-temperature substrate choice is ceramic, although processing techniques are fundamentally different from those used in PCB fabrication. Low-temperature co-fired ceramic (LTCC) is a multilayer ceramic technology, with the ability to embed passive elements such as resistors, capacitors, and inductors into a ceramic interconnect package whilst the active elements are mounted on the outer layers.
Standard solder masks are of limited value at high working temperatures. Most are epoxy-based and will oxidise at prolonged temperatures above 150°C, resulting in degradation of properties, and a colour change from green to dark brown. Price is aware of one polyimide-based solder mask, but it is not photoimageable and has limited technical capability.
Price recommends electroless nickel/immersion gold (ENIG) as an appropriate solderable finish for PCBs designed for high-temperature applications. It is flat and exhibited good shelf life and multiple solder operation capability.
Demonstrating remarkable multi-tasking skills, moderator Bob Willis turned presenter to give a practical explanation of the high-temperature soldering processes. He made it clear that the assembly process is limited by the ability of the PCB and components to withstand the peak temperature operating requirements, and remarked that some suppliers have re-qualified their high-reliability parts to operate above 175°C.
Willis listed a series of solder formulations, from SAC alloys with melting points around 220°C to high-lead alloys melting above 300°C, and reviewed a variety of soldering techniques: Manual soldering, robotic iron soldering, laser soldering, selective soldering, vapour phase soldering, and nitrogen/reactive gas reflow, describing the characteristics, relative merits, and applicability of each method and the appearance of solder joints produced.
Referring to his extensive archive of defect illustrations, he described and discussed many examples of high-temperature application defects, including component plating flaking, surface corrosion, component damage, termination dissolution, sulphur corrosion, solder pin separation, PCB delamination, plating separation, and poor hole filling.
Resuming his role as moderator, Willis conducted an energetic question-and-answer session which clarified and expanded upon several of the topics discussed and contributed interesting feedback and opinion from the attentive audience of an extremely informative SMART Group event.
More Columns from The European Angle
CircuitData: A New Open Standard for PCB Fab Data ExchangeI Never Realised It Was So Complicated!
The European Angle: Institute of Circuit Technology 43rd Annual Symposium
Ventec International Group's Martin Cotton Celebrates 50 Years in PCB Design
Reporting on the Institute of Circuit Technology Spring Seminar
EuroTech: Raw Materials Supply Chain—Critical Challenges Facing the PCB Industry
EuroTech: ENIPIG—Next Generation of PCB Surface Finish
EuroTech: Institute of Circuit Technology Northern Seminar 2016, Harrogate