Estimated reading time: 5 minutes
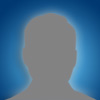
Material Witness: R.I.P. Speedboard C
Material Witness by Chet Guiles
When W. L. Gore recently announced plans to discontinue their Speedboard® C product, it created a bit of a stir in the marketplace. Here was a product that was unique and versatile and that, for many of us in the laminates business, made possible the use of our materials in applications that otherwise could have been problematic. Those of us who have been in the industry for more than a couple of years know that products, even good ones, come and go for a variety of technical and business reasons. Just as materials need to meet applications with "fit, form and function," the same kinds of criteria determine the fit of a given product for a business segment. Another example of a very good product being discontinued is the demise of the DuPont Thermount® product a few years back. That, too, created a bit of furor in the industry, but in the end in that case as in the case of Speedboard C we have to bite the collective bullet and find a way to move on.
What is it that the industry found so useful about the Speedboard C product? Because it was made using W. L. Gore's unique expanded PTFE fibers in the base fabric, with a formulated low dielectric constant thermoset resin system, the product was very useful in bonding together a variety of microwave and RF products where dissimilar and hard to bond layers of materials (such as Teflon laminates) needed to be multi-layered into a complex design. The key properties in this writer's mind were the low dielectric constant and reasonable loss, combined with the fact that it was a high-Tg (220°C) thermoset system that stuck well to a variety of materials. This combination is not easy to achieve and without the boost from the proprietary low Dk expanded PTFE reinforcement, replacing it represents something of a conundrum for the industry.
What does a product need to be and do to be useful in the sorts of applications that used Speedboard® C? As a minimum:
- Low dielectric constant for high signal speeds;
- Dielectric constant stable over a range of frequencies;
- Low loss for optimized signal integrity;
- Excellent adhesion to PTFE and other microwave/RF cores;
- Processable in standard Lamination cycles; and
- Good peel strength to standard copper foils.
What are the limitations in achieving Speedboard C Properties?
Speedboard C was a unique product based on a formulated cyanate ester resin system coated on WL Gore's proprietary expanded PTFE reinforcement. This resulted in excellent dielectric constant (2.6), good loss (0.004) and a high Tg (220°C) resin system compatible with lead-free fabrication. Full Tg development was obtainable using a cure temperature over 200°C (typical for polyimide and cyanate ester resins), though the product could be cured at lower temperatures (high Tg epoxy cures typically at 380°C) albeit with a lower Tg development.
The higher water absorption typical of cyanate ester resin systems is an issue in microwave systems, since water has a high dielectric constant (about 70) and is highly polar, which means that both Dk and df can be significantly affected at higher frequencies.
No replacement material will be Speedboard C, but an alternative offering from Arlon approximates the important electrical properties with the advantage of a much lower loss (0.002 versus 0.004 for the Speedboard C resin system) and significantly reduced water absorption. A ceramic-filled two-part resin system, the GenCladTM 280 product has lower X-Y CTE for improved registration stability and a high decomposition temperature which makes it usable in PTFE fusion-bonding lamination cycles. The ceramic component helps stabilize the Dk over temperature and the low thermal coefficient of dielectric constant is comparable to many filled PTFE products A comparison of key values for GenClad 280 and Speedboard C are shown in the following table:
* Dk values are not reported on comparable test methods.
So what are the trade-offs? And how will they impact performance?Page 1 of 2
More Columns from Various Archived Columns
Slash Sheet Chaos: Is What You See, What You Get?Moisture in Materials: Avoiding Process Gremlins
Material Witness: Beat the Heat--A Non-Math Intro to Thermal Properties
Material Witness: Considerations in Using TC Materials for PWBs
Material Witness: Are Your Materials Up to the Challenge?
Material Witness: Thermal Oxidation of Materials, Part I
Material Witness: Thermal Oxidation of Materials, Part II
Conversations with...Integrated Micro-Electronics Inc.