-
- News
- Books
Featured Books
- design007 Magazine
Latest Issues
Current IssueShowing Some Constraint
A strong design constraint strategy carefully balances a wide range of electrical and manufacturing trade-offs. This month, we explore the key requirements, common challenges, and best practices behind building an effective constraint strategy.
All About That Route
Most designers favor manual routing, but today's interactive autorouters may be changing designers' minds by allowing users more direct control. In this issue, our expert contributors discuss a variety of manual and autorouting strategies.
Creating the Ideal Data Package
Why is it so difficult to create the ideal data package? Many of these simple errors can be alleviated by paying attention to detail—and knowing what issues to look out for. So, this month, our experts weigh in on the best practices for creating the ideal design data package for your design.
- Articles
- Columns
- Links
- Media kit
||| MENU - design007 Magazine
Estimated reading time: 2 minutes
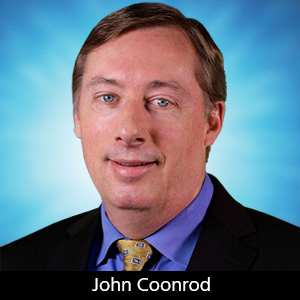
The Art of Bending and Forming PCBs
Flexible circuits are designed to be bendable, but bending rigid PCBs is a little unusual. However, many applications that do not use flex circuit technology will also require bending and forming the circuit. Some of these applications use high-frequency circuit materials to create a circuit in a form that enables improved antenna functionality. Another application involves wrapping a circuit around a structure, which sometimes functions as an antenna as well.
Bending and forming a circuit with dynamic flexing action will require understanding a few basic principles, regardless of the circuit material used. Of course, the circuit material used can make a huge difference in the success of forming circuits without causing conductor or material fracturing. As a general statement with a few exceptions, a circuit material used for bending, forming and flexing cannot have woven glass reinforcement. Because of this, typical FR-4 materials with woven glass are not recommended. Several materials used in high-frequency rigid board applications do not have glass reinforcement and have been used successfully for bending, forming and flexing.
LCP circuit materials are quite suitable for applications where bending, forming and flexing is necessary, and they offer very good high-frequency electrical performance as well. These materials are made as relatively thin laminates, typically less than 5 mils. This thinness aids in the successful bending of the circuits.
However, another set of high-frequency materials has been on the market for many years and used in forming applications: PTFE-based laminates, without glass reinforcement. These materials typically use fillers with the PTFE substrate to help lower the high CTE of PTFE, and this does not detract from the material’s bending capabilities.
The basic idea of bending circuits is based on mechanical beam composite theory. As an example, a simple double-sided circuit will be used to demonstrate the concepts. This circuit will be considered a microstrip transmission line with a signal conductor on the top conductor layer and ground plane on the bottom as shown in Figure 1.
The beam composite concept considers the cross-sectional area of a circuit that is made from different layers of materials. One property critical to understanding bending is modulus; in this case, modulus is the measurement of how stiff the circuit is. A high modulus is stiff, and low modulus is soft. When bending a circuit, softer material will generate less stress within the circuit and when there is less stress, the different layers are less likely to fracture.
Bend radius is another very important issue. A simple way to think about this: If it is necessary to bend a metal sheet that is 1/8” thick without fracturing the metal, then having a large bend radius will be advantageous and, of course, a small, tight bend radius is more likely to cause metal fracturing. The small bend radius causes more internal stress on the metal and is prone to fracturing.
To read this entire article, which appeared in the June 2015 issue of The PCB Design Magazine, click here.
More Columns from Lightning Speed Laminates
Lightning Speed Laminates: Millimeter-wave Properties and PCB Design ChallengesLightning Speed Laminates: Optimizing Thermal Management for Wireless Communication Systems
Lightning Speed Laminates: Test Vehicles for PCB Electrical Material Characterization
Lightning Speed Laminates: Optimum Thermal Stability Considerations
Lightning Speed Laminates: Thermal Management Isn’t Getting Easier
Lightning Speed Laminates: Benefits of High-Performance Hybrid Multilayer PCBs
Lightning Speed Laminates: An Overview of Copper Foils
Lightning Speed Laminates: The Importance of Circuit Features for Millimeter-Wave Applications