-
- News
- Books
Featured Books
- design007 Magazine
Latest Issues
Current IssueShowing Some Constraint
A strong design constraint strategy carefully balances a wide range of electrical and manufacturing trade-offs. This month, we explore the key requirements, common challenges, and best practices behind building an effective constraint strategy.
All About That Route
Most designers favor manual routing, but today's interactive autorouters may be changing designers' minds by allowing users more direct control. In this issue, our expert contributors discuss a variety of manual and autorouting strategies.
Creating the Ideal Data Package
Why is it so difficult to create the ideal data package? Many of these simple errors can be alleviated by paying attention to detail—and knowing what issues to look out for. So, this month, our experts weigh in on the best practices for creating the ideal design data package for your design.
- Articles
- Columns
- Links
- Media kit
||| MENU - design007 Magazine
Estimated reading time: 1 minute
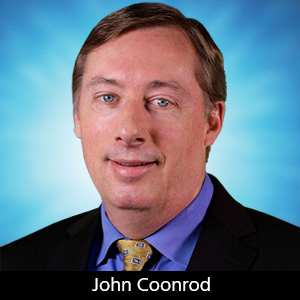
The Dilemma--Solder Mask for High-Frequency PCBs
High-frequency and high-speed digital PCBs may not have issues with solder mask. However, depending on their construction, other PCBs can have an issue with solder mask causing degraded electrical performance. PCBs with a stripline structure, in which the signal layer is buried within a multilayer, typically do not have an issue with electrical performance degradation due to solder mask. Solder mask can impact PCBs with RF circuitry on the outer layers, which can lessen high-frequency electrical performance.
Typically, PCBs with RF traces on the outer layers have minimal or no solder mask in the RF circuitry areas. Many times the solder mask is applied in areas where components are soldered to the PCB but the solder mask is developed away in the areas where conductors have critical RF performance. There are many reasons to avoid solder mask coverage on RF conductors, due to inherent solder mask properties. Most solder mask used in the PCB industry is liquid photoimageable (LPI), which is typically high in dissipation factor (Df) and high in moisture absorption, and the thickness can vary due to processing or design.
The typical solder mask has a dissipation factor of about 0.025 when tested at 1 GHz, and moisture absorption is about 1–2% depending on the formulation. For comparison, many high-frequency laminates have a Df value of about 0.005 or better and moisture absorption is typically no worse than 0.3%. The higher Df property of solder mask raises the circuit’s dielectric loss, which causes an increase in insertion loss. The moisture absorption can cause differences in impedance and phase response, but it is typically more problematic for losses where it can cause increased insertion loss.
Another point to consider is that RF circuitry on the outer layer of a PCB will usually be a microstrip or grounded coplanar waveguide (GCPW) structure. Both of these structures can have lower insertion loss and they get some loss benefit due to their fields using air. Air is the lowest-loss medium for electromagnetic waves, and these waves use electric and magnetic fields. When a microstrip or GCPW is covered with solder mask, some of the fields which were using air as the dielectric medium are now using solder mask instead.
To read this entire article, which appeared in the June 2016 issue of The PCB Design Magazine, click here.
More Columns from Lightning Speed Laminates
Lightning Speed Laminates: Millimeter-wave Properties and PCB Design ChallengesLightning Speed Laminates: Optimizing Thermal Management for Wireless Communication Systems
Lightning Speed Laminates: Test Vehicles for PCB Electrical Material Characterization
Lightning Speed Laminates: Optimum Thermal Stability Considerations
Lightning Speed Laminates: Thermal Management Isn’t Getting Easier
Lightning Speed Laminates: Benefits of High-Performance Hybrid Multilayer PCBs
Lightning Speed Laminates: An Overview of Copper Foils
Lightning Speed Laminates: The Importance of Circuit Features for Millimeter-Wave Applications