-
-
News
News Highlights
- Books
Featured Books
- design007 Magazine
Latest Issues
Current IssueAll About That Route
Most designers favor manual routing, but today's interactive autorouters may be changing designers' minds by allowing users more direct control. In this issue, our expert contributors discuss a variety of manual and autorouting strategies.
Creating the Ideal Data Package
Why is it so difficult to create the ideal data package? Many of these simple errors can be alleviated by paying attention to detail—and knowing what issues to look out for. So, this month, our experts weigh in on the best practices for creating the ideal design data package for your design.
Designing Through the Noise
Our experts discuss the constantly evolving world of RF design, including the many tradeoffs, material considerations, and design tips and techniques that designers and design engineers need to know to succeed in this high-frequency realm.
- Articles
- Columns
- Links
- Media kit
||| MENU - design007 Magazine
Estimated reading time: 4 minutes
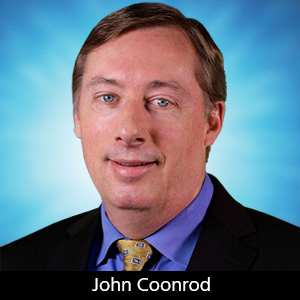
Lightning Speed Laminates: Optimizing Thermal Management for Wireless Communication Systems
The term wireless communication has been around for many years, and it can mean many different things. The wireless communication between your mouse and your computer is very different than the wireless communication between a satellite and its ground station. The PCBs which are used for wireless communications are as diverse as the term. As a general statement, a more complex wireless communication system will require a more complex PCB.
Depending on the wireless system, the requirements for the PCB can be diverse. Even within a system, the different modules or components can have very different requirements. A good example of a complex wireless communication system would be an application for a LEO (Low Earth Orbit) satellite system. The ground station will have different requirements than the space-based station. Two major differences between these two components are power level and power management.
The satellite will be designed to be very efficient for the use of electric power, due to the normal limits of operating in space. The ground station is typically less concerned with power management and can offer much higher power levels than the satellite, although with higher power levels will usually come tradeoffs between thermal management and system performance.
The satellite systems will have concerns with thermal management, but often different than the concerns for thermal management of the ground station electronics. The thermal management issues for the ground station PCBs are usually focused around using high-frequency circuit materials with low loss, high thermal conductivity, low CTE (coefficient of thermal expansion), and low TCDk (thermal coefficient of Dk). The PCB design and fabrication are also considered for thermal management concerns and, when practical, design features like via farms or via fences are included.
Most dielectrics used for high-frequency circuit materials have poor thermal conductivity when compared to the excellent thermal conductivity of metals. As a simple comparison, the thermal conductivity of copper is about 400 W/m?K and most PCB dielectric materials have a thermal conductivity around 0.3 W/m?K. Because of the big difference in thermal conductivity, some PCBs with thermal management challenges will have cavities built into them, which will minimize the amount of dielectric material in the heat flow path. The heat flow path originates from the heat source that resides on the PCB or a RF trace on the circuit, and the migration of that heat to a heat sink that will absorb the heat.
Over many years of dealing with thermal management issues, the PCB industry has informally adopted a rule of thumb that a dielectric with thermal conductivity of 0.5 W/m?K or higher is considered good for thermal management concerns. Many of the ceramic-filled high-frequency laminates have this thermal conductivity value or higher but there are a few special materials with significantly higher thermal conductivity.
RF designers must consider the different properties of the high-frequency circuit materials used in the board. For thermal management issues, a thicker substrate will increase the heat flow path, and that is not desirable. However, a thicker laminate is often desired when operating at lower microwave frequencies because there will be less insertion loss. This assumes the use of a low-loss material, with a low dissipation factor. Insertion loss is directly related to heat generation due to RF power heating the circuit, and higher insertion loss will cause more heat to be generated. A thin circuit will have a shorter heat flow path and that is desired for good thermal management. However, a circuit using a thinner substrate will have higher insertion loss and more heated generated from the applied RF power.
The tradeoffs for thermal conductivity are described here, but an application using a thick substrate should consider a material with high thermal conductivity and low dissipation factor. Of course, an application using a thin substrate will also benefit from these properties, but typically more attention is put on minimizing insertion loss so there is less heat generated. In minimizing insertion loss for a circuit based on a thin substrate, copper surface roughness is often a consideration.
Copper surface roughness at the substrate-copper interface can have significant impact on insertion loss and that is especially true for circuits based on thinner substrates. A rougher copper surface will increase conductor loss and conductor loss is usually a large portion of the overall insertion loss for a circuit based on thin material. Basically, when the copper planes are close together, which is the case for a circuit using a thin substrate, the effects of the copper surfaces will be more impactful on RF performance. The effects on RF performance are related to phase angle, wave velocity, effective Dk and, as already stated, insertion loss.
An example of material formulated specifically for thermal management concerns is a laminate with a thermal conductivity value of 1.24 W/m?K, considered very good for this property, designed for high-frequency circuit materials. Additionally, the laminate has a low dissipation factor of 0.0017 and is available with a very low-profile copper offering a smooth copper surface. Another property not previously mentioned but that can be significant for thermal management, is moisture absorption. The moisture absorption for this laminate is extremely low at 0.05% and that will greatly minimize the undesired effects that moisture can have on RF performance.
There are several different test methods which can be used to determine the thermal conductivity of a substrate. We always use a test method that does not include the effects of copper, so the stated thermal conductivity of the laminate is that of the substrate only. There are other suppliers of high-frequency laminates, which will include the effects of copper in their testing for thermal conductivity and that will cause the property to appear much better than is actually true of the substrate. For this reason and many others mentioned, it is always good to contact your material supplier when working on a new design that is sensitive to thermal issues.
This column originally appeared in the April 2023 issue of Design007 Magazine.
More Columns from Lightning Speed Laminates
Lightning Speed Laminates: Millimeter-wave Properties and PCB Design ChallengesLightning Speed Laminates: Test Vehicles for PCB Electrical Material Characterization
Lightning Speed Laminates: Optimum Thermal Stability Considerations
Lightning Speed Laminates: Thermal Management Isn’t Getting Easier
Lightning Speed Laminates: Benefits of High-Performance Hybrid Multilayer PCBs
Lightning Speed Laminates: An Overview of Copper Foils
Lightning Speed Laminates: The Importance of Circuit Features for Millimeter-Wave Applications
Lightning Speed Laminates: Prepreg Choices for Millimeter-wave PCB Applications