Estimated reading time: 3 minutes
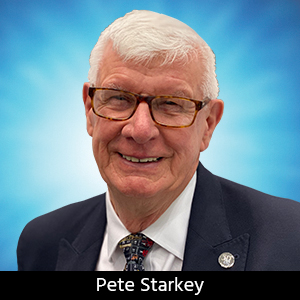
Contact Columnist Form
Cleanness Assessment Using Solvent Extract Conductivity to Improve Circuit Reliability
Setting the correct cleanliness levels for electronics to prevent premature failure is extremely important, particularly in safety-critical applications. Accurate determination of cleanliness to existing standards and the need to quantify contamination types has become more important in printed board manufacture and prior to conformal coating. Different measurement systems and techniques exist and can be used for clean and no clean processes to monitor your company's performance and potential process improvement. -- Ling Zhou
Ling Zhou, National Physical Laboratory specialist in electronic circuit reliability and metal-corrosion-induced failure mechanisms, and head of the Measurement Service for Industry in the area of electronics interconnection, presented an informative webinar on cleanness assessment using solvent extract conductivity, moderated by the ubiquitous Bob Willis.
Remarking that reliability in service was a key issue in high-density electronics assemblies, particularly those required to endure harsh operating environments, she explained that conductive contaminant residues of process chemicals could cause long-term electrical reliability problems by facilitating electrochemical corrosion, resulting in loss of continuity or short circuits.
The three pre-conditions for electrochemical failure were: Charge carriers in the form of ionic contamination together with hydrogen and hydroxyl ions from water, water itself in the form of moisture or humidity, to dissolve the ionic contaminants and sustain them in a mobile ionic state, and an electrical bias between conductors to establish an ionic current in the water layer. This electrochemical cell resulted at best in a degradation of circuit performance through current leakage and at worst, if the contaminants were corrosive, in the formation of dendrites and subsequent circuit failure.
So how to detect and measure ionic contamination? Ling Zhou described the Solvent Extract Conductivity (SEC) method, using a mixture of isopropanol and de-ionised water to remove soluble contaminants from a sample circuit board or assembly then measuring the change in conductivity of the solution to provide a measure of the average ionic contamination present, expressed as micrograms of sodium chloride per unit area. Taking the Ionograph, a proprietary SEC testing system, as an example, she explained how to set up the machine, how to verify and calibrate the system, and how to interpret the results.
She listed the benefits of SEC testing, particularly that it could be performed on production boards directly, for cost-effective assessment and ranking of ionic contamination levels, on either bare PCBs or assemblies produced using different pastes, fluxes, reflow cycles and cleaning processes. The limitation was that SEC testing did not show the distribution of contamination or the effects of any non-ionic residue, and the results could be influenced by component density and extraction efficiency. She discussed the relative merits of different standard test conditions, with reference to IPC-TM-650 2.3.25 (45°C, 10 to 20 minutes) and IPC-TM-650 2.3.25.1 (80°C, 60 minutes), commenting that the more aggressive conditions would tend to remove more contaminants and therefore give higher conductivity readings.
Ageing had a marked effect on the cleanability of solder flux residues. Experiments had been carried out at National Physical Laboratory with test boards assembled with a representative range of through-hole and surface-mount components and aged at ambient temperature for times varying from two hours to 30 days before cleaning by simple immersion in isopropanol, then tested using SEC. It was observed that simple IPA immersion cleaning was only effective for up to two days after assembly, and that residual contamination level increased with ageing time. The experiment had been repeated with different cleaning agents after 30 days ageing: 100% IPA, 75% IPA + 25% DI water, a water-based cleaner and a solvent-based cleaner, and different cleaning methods: Immersion, immersion and brushing, and immersion and scrubbing. The solvent based cleaner gave the best cleaning results, even with simple immersion. Brushing and scrubbing more effectively removed flux residues from the assembly.
Additional project work, comparing assemblies from different companies, of PCBs with HASL and ENIG finishes, soldered by different methods, had been the subject of NPL Report CMMT(A) 233 “Cleanliness and reliability evaluation of test methods and the impact of contamination from production processes on the reliability of printed circuit assemblies” by Ling Zou and Chris Hunt.
When was SEC measurement necessary? Ling Zhou recommended using SEC when new materials and process were introduced, as a good tool to evaluate the ionic contamination level from the materials and assembly processes. And there was an increasing trend for customer specifications to include ionic contamination limits in the interests of longer service life and higher reliability.
Achieving high reliability is an increasingly critical issue in today's manufacture, now that very low defect levels in manufacture are achievable. The National Physical Laboratory is very generous in sharing its knowledge through its series of free webinars. Ling Zhou is to be congratulated for delivering an enlightening presentation with a great deal of relevant practical content. And, as ever, professionally organised and seamlessly coordinated by Bob Willis.
More Columns from The European Angle
CircuitData: A New Open Standard for PCB Fab Data ExchangeI Never Realised It Was So Complicated!
The European Angle: Institute of Circuit Technology 43rd Annual Symposium
Ventec International Group's Martin Cotton Celebrates 50 Years in PCB Design
Reporting on the Institute of Circuit Technology Spring Seminar
EuroTech: Raw Materials Supply Chain—Critical Challenges Facing the PCB Industry
EuroTech: ENIPIG—Next Generation of PCB Surface Finish
EuroTech: Institute of Circuit Technology Northern Seminar 2016, Harrogate