-
- News
- Books
Featured Books
- smt007 Magazine
Latest Issues
Current IssueCounterfeit Concerns
The distribution of counterfeit parts has become much more sophisticated in the past decade, and there's no reason to believe that trend is going to be stopping any time soon. What might crop up in the near future?
Solder Printing
In this issue, we turn a discerning eye to solder paste printing. As apertures shrink, and the requirement for multiple thicknesses of paste on the same board becomes more commonplace, consistently and accurately applying paste becomes ever more challenging.
A Culture of Thriving
One cannot simply command thriving; it must be nurtured, developed, and encouraged. In this issue, we explore strategies to improve your working relationship model—both internally and externally. In this culture of thriving, your business will grow in the process.
- Articles
- Columns
Search Console
- Links
- Media kit
||| MENU - smt007 Magazine
Estimated reading time: 5 minutes
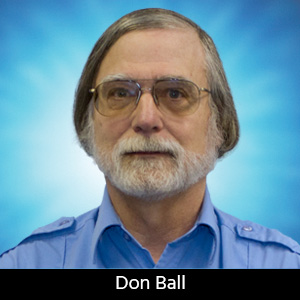
The Chemical Connection: Troubleshooting PCB Process Problems
As a supplier of PCB wet processing equipment, we inevitably find ourselves involved in helping customers solve sudden process problems that may or may not be caused by equipment malfunctions. For the most part, equipment problems are relatively easy to identify and repair: sensors for chemistry and equipment control, clogged nozzles and filters, leaks in the plumbing, etc. But what happens when the equipment checks out and the problem is still there?
This is where a bit of panic sets in: Production is backing up, deadlines for shipping are rapidly approaching, and there is no product to ship. Everyone has a pet theory as to the cause of the problem and fingers get pointed.
The first step is not to panic. Sit down and think things through. In the long run, this will save time and effort. Consider what has changed recently that might cause the problem. Can the cause of the problem be isolated? Don’t assume you know the problem, so look at alternative scenarios that might be the cause. Here are some examples from my somewhat checkered career.
An Airflow Issue
A good example of “What has changed recently?” occurred just a few months ago. A customer had a small alkaline etcher in a separate room where they were having chemistry control problems due to low use. We made a site visit and showed them how to control the etchant despite low use. On the second day of the visit, we began to successfully run their product backlog.
When we resumed running production the next day the room was suddenly filled with ammonia fumes that made it impossible to get anywhere near the etcher. The system had a warm air dryer at the end and a vent between the preceding rinse and dryer to prevent air from the dryer blowing through the system. A quick check on the flow through the vent showed the airflow was less than half of what it had been when installed.
The building had a central ventilation system and investigation showed that a new plating line had just been installed in the next room with the ventilation lines installed ahead of the feed to the alkaline etch room. When those vents were on, it reduced the airflow to the alkaline etch room, so there wasn’t enough flow in the vent to prevent the air from the dryer from flowing through the system, and it was blowing ammonia fumes into the room. We solved the problem by reducing the airflow from the dryer to the minimum needed so we could dry the panels and not overwhelm the vent. This was a somewhat obvious cause-and-effect situation, but other things we could have considered might have been changes in chemistry or suppliers, materials or suppliers, or processing in prior steps.
A Problem on the DES Line
An example of isolating the problem happened more than 20 years ago when a customer had just installed a new DES line and reported that line widths on panels were frequently out of spec. They ran developed panels from their other DES line through the new etcher without any problems with line width specifications, but developed panels from the new line etched in the other etcher showed the same out-of-spec line widths; therefore, not unreasonably, the problem was with the developer in the new line.
A trip to the customer site could find nothing obviously wrong with the new developer. Fortunately, the customer had a standard test pattern they ran through each system daily and an AOI to get quick results. They ran the test patterns in groups of five to check repeatability and the data was stored. A review of the data from the new line revealed that from each group of five, some panels were well within specifications, some were barely in specifications, some were wildly out of specifications, and none of the groups of five were entirely in or out of specifications.
A problem with the developer would show consistent failure modes, not on and off problems, so I concluded the problem was with the exposure unit. But could it be? The exposure unit was brand new with the DES line and was the latest and greatest unit available; it cost more than the DES line. Some exposed but undeveloped panels were collected along with some unexposed panels and brought back to our lab. The exposed panels were developed in the lab etcher and the unexposed panels were exposed in our exposure unit (not the latest and greatest by any means). The panels were then brought back to the customer site. The panels exposed there and developed in our lab showed the same problem of inconsistent line width specifications while the panels exposed in our lab and passed through the new DES line all passed with flying colors.
A technician from the exposure unit supplier was reluctantly called in and, after careful testing, found a slight crack in the vacuum line. Sometimes it sealed itself when the vacuum was drawn and gave the phototool good contact with the etch resist. Sometimes the crack didn’t seal tightly, allowing some slight off-contact with the resist even though the pressure gauges said the seal was good. That vacuum line was replaced, and everything was good.
You may wonder how they got good panels off the other developer if the exposure unit was the problem. Well, the other DES line had a different exposure unit, something I should have checked but didn’t think of. I could have saved a lot of travel time (six hours each way) if I had thought about it.
Conclusion
I have many more such examples, but the point is to think rationally when confronted by a process problem and not succumb to the urge to panic and throw every possible solution at it, hoping one of them will work. Contact your suppliers (and not just your equipment suppliers); they’ve probably seen more weird problems than you can imagine and may have some insight. Finally, remember that these process problems don’t just jump out at you for no reason. There is a cause that can be found and fixed if you use reason and logic.
This column originally appeared in the October 2024 issue of PCB007 Magazine.
More Columns from The Chemical Connection
The Chemical Connection: How We Deal With a Technology RoadmapThe Chemical Connection: Chemical and Equipment Control of High-density Circuits, Part 2
The Chemical Connection: Controlling an Alkaline Etch Bath With Low Copper Loading
The Chemical Connection: Chemical and Equipment Control of High-density Circuits
The Chemical Connection: Can the Limits of Subtractive Etching Be Extended?
The Chemical Connection: Reducing Etch System Water Usage, Part 2
The Chemical Connection: Reducing Etch System Water Usage, Part 1
The Chemical Connection: An Exhibitor’s View of IPC APEX EXPO