-
- News
- Books
Featured Books
- design007 Magazine
Latest Issues
Current IssueAdvanced Packaging and Stackup Design
This month, our expert contributors discuss the impact of advanced packaging on stackup design—from SI and DFM challenges through the variety of material tradeoffs that designers must contend with in HDI and UHDI.
Rules of Thumb
This month, we delve into rules of thumb—which ones work, which ones should be avoided. Rules of thumb are everywhere, but there may be hundreds of rules of thumb for PCB design. How do we separate the wheat from the chaff, so to speak?
Partial HDI
Our expert contributors provide a complete, detailed view of partial HDI this month. Most experienced PCB designers can start using this approach right away, but you need to know these tips, tricks and techniques first.
- Articles
- Columns
Search Console
- Links
- Media kit
||| MENU - design007 Magazine
Estimated reading time: 4 minutes
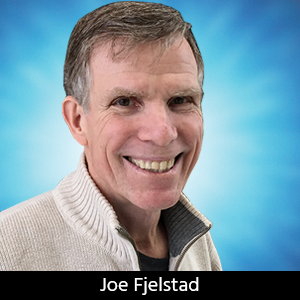
Flexible Thinking: Another PCB Design Paradigm Shift in the Works
Spend a half-century engaged in any kind of manufacturing technology, and you will see a boatload of change, especially in the realm of printed circuits. I can attest to this from personal experience.
While the precise date is contested, Paul Eisler is often credited with the invention of circuit boards in the 1930s, but the patent was suppressed for strategic reasons in the run-up to World War II. It was a military application (proximity fuses for mortar shells) that ushered in the mass production of printed circuits. Since then, the rapid advancement of technology (often still in service of the military’s needs) has altered the landscape of PCB design over the years. We have shared and codified what we have learned into industry standards. The once tried, tested, and relied-upon "rules" are now being challenged by the ever-increasing complexity of electronic systems, driven by the pursuit of higher performance, smaller form factors, and lower power consumption—all at lower costs.
We all read from the same technology scriptures and sing from the same design hymnals that serve the global congregation of printed circuit manufacturers and users, though there are still a few iconoclasts and heretics to challenge them in the service of largely positive change. Even subtle changes are hard to effect. People, especially those in manufacturing, do not like change because it disrupts the manufacturing floor routine. However, change, as even the ancient philosophers knew, is constant and required for continued growth and evolution.
Here are some factors that have influenced and driven design rule changes:
- Miniaturization: Small has long been a hallmark of electronics because it is the watershed from which flows almost every other benefit that we desire in our electronic products. Smaller is convenient, lighter, requires less energy, is higher performing because of proximity, and is more environmentally friendly.
- Power/thermal management: Miniaturization is desirable but comes at a cost. Packing more electronics in closer proximity may improve size and performance and even battery life in portable products, but it also increases energy density and, therefore, heat generation, which needs to be managed. Heat is the product of electron movement and the enemy of product reliability. This requires attention early on, not as an afterthought.
I have been developing ways to integrate thermal management into electronic assemblies and solve the thermal problem up front. This espouses ways to minimize heat damage to electronics by reversing the manufacturing process. Rather than building a printed circuit and assembling components on them, build heat-spreading component boards and then build circuits on them. This is one of the iconoclastic/heretical ideas alluded to earlier. It could be simpler and cheaper, however, it will also require more care up front and in the manufacturing process because rework and repair will be more challenging, if not impossible. Just as the nascent aerospace industry was often dangerous and even fatal, I believe we will adjust to deliver the promise through learned and shared experience. Change your thinking, change your outlook.
For the foreseeable future, signal integrity and timing constraint management will also require attention. With signals now nearing their practical limits based on physics, factors such as crosstalk, impedance mismatch, and delay variations are critical, and strict management of timing needs requires the designer to carefully consider things that were once of little concern. Matching trace lengths, via design, placement, construction, and even power plane design, is consequential. There are also concerns related to layer count. The number of layers in a PCB stackup and material selection can directly impact signal and power integrity, and thermal performance. Moreover, layer sequencing—the arrangement of signal, power, and ground layers—done incorrectly can create many signaling problems. Done correctly, it can minimize crosstalk, reduce impedance variations, and help control unwanted noise. On the bright side, electronic design automation and validation tools are rapidly evolving, and with increased availability and adaptation of AI to the design process, improvements will continue to accelerate.
Changes are coming at an accelerated pace. We must try to stay ahead of them or get run over. We must be the masters of our future rather than its victims.
The long-standing rules of PCB design are insufficient to address the challenges posed by current trends and new developments. As a result, new design methodologies, simulation tools, and manufacturing techniques are emerging to meet these requirements. To make it all work, we will need to engage in improved practices, including:
- Creating a closer collaboration between PCB and system designers, packaging engineers, and manufacturing experts to ensure early design optimization. Several years ago, I wrote that it will be essential to optimize the design from the outset. To achieve this, we should design with manufacturing, rather than for manufacturing—DWM instead of DFM.
- Using advanced simulation tools to analyze signal and power integrity, and thermal performance will help identify and mitigate potential issues early in the design process.
Everyone in the electronics industry will need to adapt to the rapid changes. Given the industry's breakneck speed of development, staying up to date with the latest technologies and design techniques will be essential to remaining competitive. By embracing these evolving principles and leveraging advanced technologies, PCB designers can push the boundaries of performance and innovation and have a great time while doing so.
Joe Fjelstad is founder and CEO of Verdant Electronics and an international authority and innovator in the field of electronic interconnection and packaging technologies with more than 185 patents issued or pending. To read past columns or contact Fjelstad, click here. Download your free copy of Fjelstad’s book Flexible Circuit Technology, 4th Edition, and watch his in-depth workshop series “Flexible Circuit Technology.”
This column originally appeared in the December 2024 issue of Design007 Magazine.
More Columns from Flexible Thinking
Flexible Thinking: Rules of Thumb—A Word to the WiseFlexible Thinking: Musings on High Density Interconnections
Flexible Thinking: Integrated Passive Devices—Design Solutions With Many Benefits
Flexible Thinking: Mechatronics in a Flex World
Flexible Thinking: PCB Designers Still Wanted
Flexible Thinking: Embedded Design—A Term With Multiple Meanings
Flexible Thinking: What Matters When Designing Next-generation Products?
Flexible Thinking: The Simplest Way Is the Best Way