-
- News
- Books
Featured Books
- pcb007 Magazine
Latest Issues
Current IssueSales: From Pitch to PO
From the first cold call to finally receiving that first purchase order, the July PCB007 Magazine breaks down some critical parts of the sales stack. To up your sales game, read on!
The Hole Truth: Via Integrity in an HDI World
From the drilled hole to registration across multiple sequential lamination cycles, to the quality of your copper plating, via reliability in an HDI world is becoming an ever-greater challenge. This month we look at “The Hole Truth,” from creating the “perfect” via to how you can assure via quality and reliability, the first time, every time.
In Pursuit of Perfection: Defect Reduction
For bare PCB board fabrication, defect reduction is a critical aspect of a company's bottom line profitability. In this issue, we examine how imaging, etching, and plating processes can provide information and insight into reducing defects and increasing yields.
- Articles
- Columns
- Links
- Media kit
||| MENU - pcb007 Magazine
Estimated reading time: 9 minutes
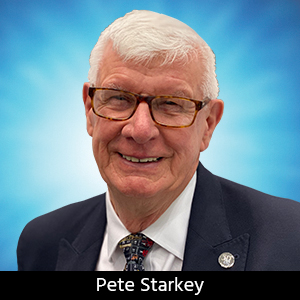
Contact Columnist Form
An Inside Look: 3D AOI of Electronic Assemblies Seminar
For very small components, camera resolution became a significant issue. For example, for pixels of 8 microns, the dimensions of an 0201 component corresponded to 31 pixels x 16 pixels and sub-pixel resolution enhancement was necessary to calculate the relative position of the edge of a component within a pixel. This was achieved by measuring differences in shades of grey in adjacent pixels. Jones discussed detection algorithms for component shift, component missing, insufficient or excess solder and foreign matter, with a series of examples of detected defects, and the potential benefits of future developments in coaxial lighting in improving the detection of dry soldering pads and the position of non-tilted silicon-based bottom-terminated components.
This capability assessment had concluded that the 3D AOI system as described was capable of inspecting 03015 and 0201 micro-components and of detecting defective symptoms such as component shift, component lifted, component missing, insufficient or excess solder or bridging, solder balls, and solder splash.
Pierre Williams from Yamaha discussed new technology available in SMT equipment and software to help raise production yield and reduce waste in a presentation entitled “Boosting Quality Control and Productivity through Closed-Loop AOI.” The goals were to produce more good units and achieve a higher end-of-line inspection pass rate, with fewer line stoppages and faster fault resolution. To achieve these goals, the requirements were high-quality inspection data, real-time information and feedback of defect data, and access to detailed reports, either at the machine or on the move.
In a typical SMT line there was only one AOI and this was located post reflow so that defects were not found until after board has been soldered, meaning that several defective boards could be in reflow by the time the first defect was found, and significant human intervention was needed to monitor reports and stop the line. On a short production run, the run could be finished before the defect was found and there was no benefit from feedback. Until recently, there was no facility for the AOI to communicate with the pick-and-place machine, so quality information was not shared between the inspection area and the production area and there was no scope to eliminate a problem whilst it was occurring.
In the knowledge that reflow could correct minor placement errors, Williams suggested locating the AOI machine after placement and before reflow as the first stage in the transition to closed-loop feedback so that defects could be detected before boards were reflowed. Large amounts of manual rework and repair could be avoided and high-value components could be retrieved and reused. With suitable software, this gave the option to automatically feed-back data from the AOI to the pick-and-place and pinpoint the origin of the defect, and conversely, close the loop to feed forward data from the mounter to optimise AOI performance.
Page 3 of 4
More Columns from The European Angle
CircuitData: A New Open Standard for PCB Fab Data ExchangeI Never Realised It Was So Complicated!
The European Angle: Institute of Circuit Technology 43rd Annual Symposium
Ventec International Group's Martin Cotton Celebrates 50 Years in PCB Design
Reporting on the Institute of Circuit Technology Spring Seminar
EuroTech: Raw Materials Supply Chain—Critical Challenges Facing the PCB Industry
EuroTech: ENIPIG—Next Generation of PCB Surface Finish
EuroTech: Institute of Circuit Technology Northern Seminar 2016, Harrogate