-
- News
- Books
Featured Books
- pcb007 Magazine
Latest Issues
Current IssueInventing the Future with SEL
Two years after launching its state-of-the-art PCB facility, SEL shares lessons in vision, execution, and innovation, plus insights from industry icons and technology leaders shaping the future of PCB fabrication.
Sales: From Pitch to PO
From the first cold call to finally receiving that first purchase order, the July PCB007 Magazine breaks down some critical parts of the sales stack. To up your sales game, read on!
The Hole Truth: Via Integrity in an HDI World
From the drilled hole to registration across multiple sequential lamination cycles, to the quality of your copper plating, via reliability in an HDI world is becoming an ever-greater challenge. This month we look at “The Hole Truth,” from creating the “perfect” via to how you can assure via quality and reliability, the first time, every time.
- Articles
- Columns
- Links
- Media kit
||| MENU - pcb007 Magazine
Estimated reading time: 2 minutes
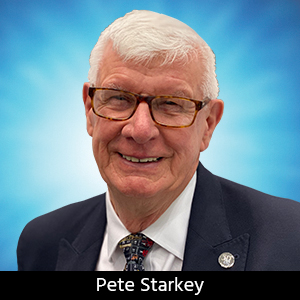
Contact Columnist Form
ECWC 2014: The Drilling and Routing Session
Notable amid the vast array of information and knowledge shared at the 13th Electronic Circuits World Convention in Nuremberg, Germany, was the highly-informative session on advances in drilling and routing, with a focus on the technology of cutting tools. The session was introduced and moderated by EIPC Technical Director Michael Weinhold.
Growth in applications of high-power LEDs had created an increasing demand for substrates with high thermal conductivity, and resulted in the development of a wide range of insulated metal substrates heavily loaded with ceramic fillers in the dielectric. Consequently, the dielectric layer of these composite laminates tended to be very abrasive, causing rapid wear of conventional tungsten carbide routing cutters. Johann Schmidt of CGT GmbH discussed how diamond coated tools could significantly increase dimensional accuracy and reduce production cost.
Schmidt described a proprietary process for diamond coating of tungsten carbide drills and routers, based on hot-filament chemical vapour deposition. A particular feature of this proprietary coating was that it was built up as a multilayered combination of different crystalline and nano-crystalline layers. Typical coating thickness was 12 microns, although this could be varied depending on tool geometry and diameter. The multilayered structure gave the benefit of resistance to crack propagation, a major limitation of single-layer coatings, and a very smooth surface with low friction and excellent chip-removal characteristics. Hardness of the coating was approximately 9000VPN, compared with about 2100VPN for standard tungsten carbide grades, and coated tools could be used at higher feeds and speeds.
Schmidt showed many comparative examples: On a typical IMS substrate, routing feed could be increased from 4 mm per second to 15mm per second with tool life extended from 7.5 metres to 60 metres. And a coated drill could complete 1,000 hits with no clogging, whereas a conventional drill was clogged with aluminium swarf after only 150 hits.
Diamond-coated tools offered greater dimensional accuracy and cost and productivity benefits from increased production speeds and significantly improved tool life resulting in less machine down-time for tool changing. Clearly, even with the most advanced cutter technology, good tool management, machine maintenance and operating discipline were essential, with minimal spindle run-out, rigid fixturing of the work and powerful vacuum extraction if the best results were to be realised. Some applications, such as using a 2-flute end-mill on IMS, benefited from wet lubrication.
Page 1 of 2
More Columns from The European Angle
CircuitData: A New Open Standard for PCB Fab Data ExchangeI Never Realised It Was So Complicated!
The European Angle: Institute of Circuit Technology 43rd Annual Symposium
Ventec International Group's Martin Cotton Celebrates 50 Years in PCB Design
Reporting on the Institute of Circuit Technology Spring Seminar
EuroTech: Raw Materials Supply Chain—Critical Challenges Facing the PCB Industry
EuroTech: ENIPIG—Next Generation of PCB Surface Finish
EuroTech: Institute of Circuit Technology Northern Seminar 2016, Harrogate