-
- News
- Books
Featured Books
- pcb007 Magazine
Latest Issues
Current IssueSales: From Pitch to PO
From the first cold call to finally receiving that first purchase order, the July PCB007 Magazine breaks down some critical parts of the sales stack. To up your sales game, read on!
The Hole Truth: Via Integrity in an HDI World
From the drilled hole to registration across multiple sequential lamination cycles, to the quality of your copper plating, via reliability in an HDI world is becoming an ever-greater challenge. This month we look at “The Hole Truth,” from creating the “perfect” via to how you can assure via quality and reliability, the first time, every time.
In Pursuit of Perfection: Defect Reduction
For bare PCB board fabrication, defect reduction is a critical aspect of a company's bottom line profitability. In this issue, we examine how imaging, etching, and plating processes can provide information and insight into reducing defects and increasing yields.
- Articles
- Columns
- Links
- Media kit
||| MENU - pcb007 Magazine
Estimated reading time: 3 minutes
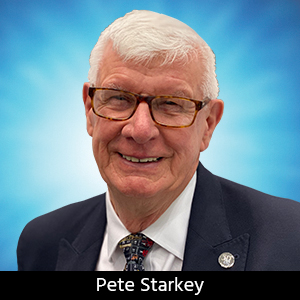
Contact Columnist Form
ECWC 2014: The Metal-base PCB Technology Session
The presentation that attracted most interest and provoked plenty of interactive discussion came from Joe Fjelstad of Verdant Electronics who described an alternative approach to the manufacture of electronic assemblies, which used aluminium as a substrate and eliminated the soldering process. Aluminium had many attributes which made it attractive as an alternative circuit substrate: Abundance, low cost, thermal conductivity, light weight, dimensional stability, thermal expansion comparable with copper, ease of processing, and capable of being anodised or electrophoretically coated.
Ironically, the main reason aluminium had not been considered for traditional PCB applications was its high thermal conductivity and heat-sinking ability, which limited the practicability of the soldering process. Except in applications such as LED substrates, designers had preferred to specify resin-based laminates and then deal with thermal management issues after completion of assembly. And even in the knowledge of the thermal issues and intrinsic reliability problems associated with the introduction of lead-free soldering, human inertia--“better the devil you know” attitudes--had tended to preclude the consideration of radical alternative concepts.
Fjelstad advocated reversing the assembly process to eliminate the solder issue, by positioning and bonded all the components on an aluminium carrier with leads facing up, encapsulating the components in place, exposing the terminations, and interconnecting them by additive or semi-additive PCB fabrication techniques or alternative direct interconnection methods. Because solder lands were not required, conductor routing density could be higher so that fewer layers would be required. The basic manufacturing infrastructure was already in place, semi-additive fabrication processes were well-established, and the concept was appropriate for all classes of products including flex.
The benefits of solderless assembly were many: No PCB was required, no soldering was required, component concerns were reduced, circuit design layout was easier, design security was increased, thermal management was integral, reliability was enhanced, and multiple novel structure options were possible--modular array assemblies, aluminium-core rigid-flex, direct-write prototyping. The limits were more likely to be defined by the imagination of the designer than by the fundamental limitations of the technologies that Fjelstad had described. “Change may happen slowly, but change always comes…”
Page 2 of 2More Columns from The European Angle
CircuitData: A New Open Standard for PCB Fab Data ExchangeI Never Realised It Was So Complicated!
The European Angle: Institute of Circuit Technology 43rd Annual Symposium
Ventec International Group's Martin Cotton Celebrates 50 Years in PCB Design
Reporting on the Institute of Circuit Technology Spring Seminar
EuroTech: Raw Materials Supply Chain—Critical Challenges Facing the PCB Industry
EuroTech: ENIPIG—Next Generation of PCB Surface Finish
EuroTech: Institute of Circuit Technology Northern Seminar 2016, Harrogate