-
- News
- Books
Featured Books
- pcb007 Magazine
Latest Issues
Current IssueSales: From Pitch to PO
From the first cold call to finally receiving that first purchase order, the July PCB007 Magazine breaks down some critical parts of the sales stack. To up your sales game, read on!
The Hole Truth: Via Integrity in an HDI World
From the drilled hole to registration across multiple sequential lamination cycles, to the quality of your copper plating, via reliability in an HDI world is becoming an ever-greater challenge. This month we look at “The Hole Truth,” from creating the “perfect” via to how you can assure via quality and reliability, the first time, every time.
In Pursuit of Perfection: Defect Reduction
For bare PCB board fabrication, defect reduction is a critical aspect of a company's bottom line profitability. In this issue, we examine how imaging, etching, and plating processes can provide information and insight into reducing defects and increasing yields.
- Articles
- Columns
- Links
- Media kit
||| MENU - pcb007 Magazine
Estimated reading time: 7 minutes
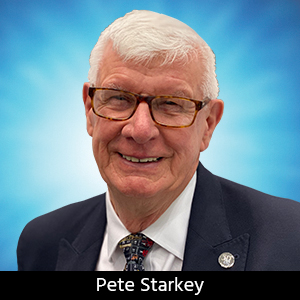
Contact Columnist Form
ECWC 2014: The Base Materials Session
The focus of the session turned to new base materials as Lin Lin, from the Technology Development Centre at Panasonic, introduced a newly-developed ultra-low-loss laminate for high-speed and high-frequency PCBs.
The exponential trend in information and communications technology, for example the projected 61% compound annual growth rate in global mobile data traffic, necessitating the high-speed transmission of large-volume data using the minimum of electrical energy, had created a demand for halogen-free low-loss laminates suitable for fabricating high layer count PCBs with high heat resistance, low CTE, high thickness accuracy, and suitability for lead-free soldering
Of the many laminates previously developed for use in high-speed and high-frequency applications, only woven-glass ceramic-filled PTFE materials had the right dielectric properties to meet performance requirements at GHz frequencies. But PTFE materials were difficult to laminate so their use was limited to low layer-count constructions, so Panasonic had set out to develop a new-generation material with equivalent dielectric properties but better heat resistance and processability, suitable for building high layer-count multilayers.
To achieve the desired dielectric loss characteristics, they had based their new material on a low-Df thermosetting polymer, a modified polyphenylene ether, with a low-Df, low-Dk hardener and a low-Df inorganic filler. The high crosslink density gave low CTE and good temperature resistance. When combined with a low-Dk glass cloth and a low- profile copper foil, the result was a novel high-performance material with excellent stability of dielectric properties within a wide frequency range, with ultra-low transmission loss and lower temperature drift than ceramic-filled PTFE. And the laminates and pre-pregs were eminently suitable for the fabrication of high layer-count HDI multilayer constructions. The new material was expected to be widely applied to next-generation high-speed and high-frequency applications such as network equipment, base stations and high frequency parts. The material had high Tg, low moisture absorption and good heat resistance, making it compatible with lead-free soldering processes.
Not all electronics-grade resins were used in laminate manufacture. The final presentation of the base materials session gave an insight into alternative applications of resins at the next level, in impregnating, encapsulating, and potting of transformers and modules. Jens Buerger from ELANTAS Beck, specialists in the protection of electronic components in the automotive, industrial, medical, and avionics sectors, reported the results of a study of the impact of linear coefficient of expansion on temperature shock resistance.
There were three main categories of electronic protection: thin-film coatings applied by dip or spray were mainly used for moisture protection of PCBs. Thick film coatings, typically applied by dam-and-fill, swirl or dip, were used for major protection of PCBs from chemical attack and vibration. Encapsulation or potting, by dispensing or vacuum potting, gave chemical, mechanical and vibration protection, as well as sealing the assembly.
Page 3 of 4
More Columns from The European Angle
CircuitData: A New Open Standard for PCB Fab Data ExchangeI Never Realised It Was So Complicated!
The European Angle: Institute of Circuit Technology 43rd Annual Symposium
Ventec International Group's Martin Cotton Celebrates 50 Years in PCB Design
Reporting on the Institute of Circuit Technology Spring Seminar
EuroTech: Raw Materials Supply Chain—Critical Challenges Facing the PCB Industry
EuroTech: ENIPIG—Next Generation of PCB Surface Finish
EuroTech: Institute of Circuit Technology Northern Seminar 2016, Harrogate