-
- News
- Books
Featured Books
- pcb007 Magazine
Latest Issues
Current IssueInventing the Future with SEL
Two years after launching its state-of-the-art PCB facility, SEL shares lessons in vision, execution, and innovation, plus insights from industry icons and technology leaders shaping the future of PCB fabrication.
Sales: From Pitch to PO
From the first cold call to finally receiving that first purchase order, the July PCB007 Magazine breaks down some critical parts of the sales stack. To up your sales game, read on!
The Hole Truth: Via Integrity in an HDI World
From the drilled hole to registration across multiple sequential lamination cycles, to the quality of your copper plating, via reliability in an HDI world is becoming an ever-greater challenge. This month we look at “The Hole Truth,” from creating the “perfect” via to how you can assure via quality and reliability, the first time, every time.
- Articles
- Columns
- Links
- Media kit
||| MENU - pcb007 Magazine
Estimated reading time: 7 minutes
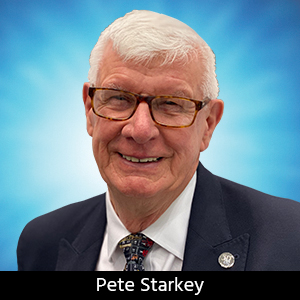
Contact Columnist Form
ECWC 2014 Market Session: Connecting the World
On the first day of the 13th Electronic Circuits World Convention (ECWC), delegates crowded into the Kiew Room of the Nuremberg Messe to hear four of the world’s leading experts on PCB markets and market trends make their analysis of what the future held for the industry. Introduced and moderated by IPC’s Marc Carter, the session included presentations from Dr. Hayao Nakahara, Walt Custer, Michael Weinhold, and Bill Burr.
“Cost, cost, cost--unless you can meet the cost, you can’t continue your business!” These were Dr. Nakahara’s opening words as he examined the business situation in China and discussed the alternative market areas attracting investment. In 2012, China’s share of world PCB production was 44%, and it had seemed destined to continue its domination into the long term. However, rising wages, labour shortages, high personnel turnover, and tougher environmental regulations were making it increasingly difficult to operate, particularly in the coastal regions.
Japanese PCB makers had stopped investing in China and were expanding operations in South East Asia, particularly in Thailand and Vietnam, as were some Taiwanese and South Korean manufacturers. Thailand was the largest PCB producing area in South East Asia, with output already exceeding that of Germany, followed by Vietnam, Malaysia, the Philippines, Singapore, and Indonesia. No substantial Japanese investments were being made in the Philippines and Indonesia, and costs were so high in Singapore that new investment was out of the question.
Why not India or Brazil? Although there had been much speculation over the years, there were no signs of expansion. Government regulations and lack of infrastructure made it difficult to make large investments in India, and although the importation of PCBs continued to increase, domestic production was relatively static. Brazil lacked infrastructure and had the additional burden of a complex taxation system. Output had fallen substantially since Multek had closed down its Brazilian operation.
By comparison, South East Asia had reasonable infrastructure, although nowhere near as highly developed as China, and there were laminate factories in Thailand, Singapore and Malaysia, which also had the world’s largest foil plant.
Dr. Nakahara forecast that South East Asia’s share of the world PCB market would rise from 6.8% in 2013 to 8.2% in 2017, and be worth over $5 billion.
Page 1 of 4
More Columns from The European Angle
CircuitData: A New Open Standard for PCB Fab Data ExchangeI Never Realised It Was So Complicated!
The European Angle: Institute of Circuit Technology 43rd Annual Symposium
Ventec International Group's Martin Cotton Celebrates 50 Years in PCB Design
Reporting on the Institute of Circuit Technology Spring Seminar
EuroTech: Raw Materials Supply Chain—Critical Challenges Facing the PCB Industry
EuroTech: ENIPIG—Next Generation of PCB Surface Finish
EuroTech: Institute of Circuit Technology Northern Seminar 2016, Harrogate