-
- News
- Books
Featured Books
- smt007 Magazine
Latest Issues
Current IssueSupply Chain Strategies
A successful brand is built on strong customer relationships—anchored by a well-orchestrated supply chain at its core. This month, we look at how managing your supply chain directly influences customer perception.
What's Your Sweet Spot?
Are you in a niche that’s growing or shrinking? Is it time to reassess and refocus? We spotlight companies thriving by redefining or reinforcing their niche. What are their insights?
Moving Forward With Confidence
In this issue, we focus on sales and quoting, workforce training, new IPC leadership in the U.S. and Canada, the effects of tariffs, CFX standards, and much more—all designed to provide perspective as you move through the cloud bank of today's shifting economic market.
- Articles
- Columns
- Links
- Media kit
||| MENU - smt007 Magazine
Estimated reading time: 15 minutes
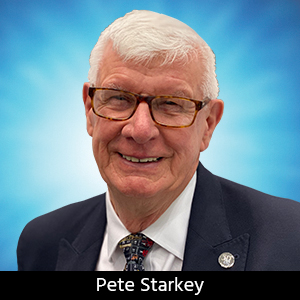
Contact Columnist Form
NPL/SMART Group Conformal Coating & Cleaning Experience
How to rework and repair conformally coated PCB assemblies was the topic of the presentation by Humiseal Technical Support Specialist Jon Anderson. He cited IPC 7711/7721 as a comprehensive work of reference for training engineers in rework and repair procedures for conventional and surface mount components as well as procedures for the removal and replacement of coatings and the soldering and de-soldering of different component types.
IPC 7711/7721 gave guidance on identifying coating types and suggestions as to which removal methods were the most appropriate for which coatings. Although it was possible to rework through coatings without removing them, it was not recommended to do so because of the risk of contamination of assemblies and tools with breakdown products.
Selective coating removal could be achieved by solvent swelling, and solvent pens were available from the suppliers of coatings. Alternatively, mechanical methods could be used, both for selective removal and for clean-up after rework. Typical systems used micro abrasive blasting, with dry media selected to suit the application; natural materials, plastic or mineral abrasives were available in a range of grit sizes. Anderson showed many examples of selective coating removal he had carried out at SMART Group workshops. Once the rework operation had been completed, the conformal coating could be reinstated by brushing or manual dipping.
Willis took the stage again for the day’s final presentation: A discussion of process and field failures, beginning by showing the results of a SMART Group on-line survey which indicated that the most common conformal coating defects were de-wetting (36%), bubbles (27%) and missing coating (13%). He used video clips to illustrate how such defects occurred, emphasising the value of assessing the surface energy of solder masks, and the importance of controlling viscosity and hold times in the coating process. Coating specifications should define where coating was required, where it was not required, and particularly where it did not matter, to avoid unnecessary re-work.
Dendrite formation was the most common field-failure mode in his experience, a consequence of ionic contamination in the presence of moisture and electrical bias, and once again his real-time video examples clearly illustrated how it occurred.
Regarding re-work and repair, his advice was to remove conformal coating before de-soldering components, to minimise the damage, to keep it simple and to clean the tools afterwards!
Page 3 of 7
More Columns from The European Angle
CircuitData: A New Open Standard for PCB Fab Data ExchangeI Never Realised It Was So Complicated!
The European Angle: Institute of Circuit Technology 43rd Annual Symposium
Ventec International Group's Martin Cotton Celebrates 50 Years in PCB Design
Reporting on the Institute of Circuit Technology Spring Seminar
EuroTech: Raw Materials Supply Chain—Critical Challenges Facing the PCB Industry
EuroTech: ENIPIG—Next Generation of PCB Surface Finish
EuroTech: Institute of Circuit Technology Northern Seminar 2016, Harrogate