-
- News
- Books
Featured Books
- pcb007 Magazine
Latest Issues
Current IssueInventing the Future with SEL
Two years after launching its state-of-the-art PCB facility, SEL shares lessons in vision, execution, and innovation, plus insights from industry icons and technology leaders shaping the future of PCB fabrication.
Sales: From Pitch to PO
From the first cold call to finally receiving that first purchase order, the July PCB007 Magazine breaks down some critical parts of the sales stack. To up your sales game, read on!
The Hole Truth: Via Integrity in an HDI World
From the drilled hole to registration across multiple sequential lamination cycles, to the quality of your copper plating, via reliability in an HDI world is becoming an ever-greater challenge. This month we look at “The Hole Truth,” from creating the “perfect” via to how you can assure via quality and reliability, the first time, every time.
- Articles
- Columns
- Links
- Media kit
||| MENU - pcb007 Magazine
Estimated reading time: 10 minutes
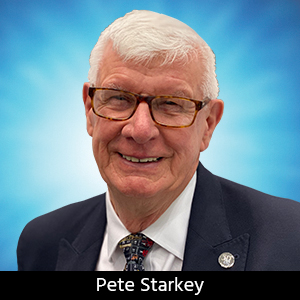
Contact Columnist Form
IeMRC Conference in UK: Five Years of Innovation
The leaves were just beginning to fall on a misty autumn morning in Loughborough, in the East Midlands of the UK, at a new venue for the Fifth-Annual Conference of the Innovative Electronics Manufacturing Research Centre (IeMRC), now at the Holywell Park Conference Centre on the University campus. IeMRC is the UK's internationally-recognised provider of world-class electronics manufacturing research, which focuses on sustaining and growing high-value manufacturing in the UK by delivering innovative and exploitable new technologies and by providing strategic value to the electronics industry.
Industrial Director Professor Martin Goosey opened the conference with a brief review of the five years since the foundation of IeMRC, and was pleased to report that funding had been secured for the next five years and that two flagship projects and eleven standard projects were currently being supported. A further call for proposals would be made in early 2011.
Professor Goosey introduced the first session, on the theme of advanced packaging, and the keynote presentation was given by Dr. David Pedder, with a discussion of the role of flip-chip bonding. Since the introduction of the flip-chip concept by IBM in the early 1960s, devices had progressed from simple transistors with three bonds per chip to system-on-chip devices with over 2100. Flip-chip gave the benefits of very high-interconnection density and improved high-frequency performance with minimal component footprint. Dr. Pedder reviewed bonding technologies: Solder flip-chip bonding was the predominant technique and typically used a 95Pb-5Sn solder. He explained how solder bumps were formed on the chip and how solder joints were subsequently formed with the substrate, where the effect of surface tension of the solder assisted in alignment and achieving a predictable solder joint geometry. Adhesive flip-chip bonding was popular for chip-on-glass and chip-on-flex applications, with the advantages low process temperature and requiring no underfill, as well as being lead-free. Solid phase flip-chip bonding was employed in flip-chip-on-board and flip-chip-in-package applications. Gold bumps were generally used, and joints made by thermocompression or thermosonic bonding. Flip chip techniques were now being utilised within conventional packages as an alternative to wire bonding and would continue to grow in importance as a key packaging technology. Ten years ago, 2% of all devices employed flip-chip principles, presently the figure was about 5% and this was projected to grow to 10% over the next 10 years.
Norman Stockham from The Welding Institute addressed the potential choices of packaging materials and joining and interconnection processes for high-temperature electronics and sensors, such as those used in the automotive, aerospace and oil and gas sectors. The sub-title of his presentation was "Beyond Solder?" Solder had thousands of years of history and many electronic components were specifically designed for assembly by soldering, which combined high production volume capability with good electrical and thermal conductivity. Solder joints were self-aligning and reworkable, but when service temperatures approached 300°C, conventional electronics solders were no longer appropriate. High-temperature solders were available with melting points up to 450°C, and brazing alloys up to 1,000°C, but at service temperatures over 300°C, the performance and reliability of conventional joining and packaging technologies were being significantly challenged. Stockham reviewed a wide range of options for device and substrate attach, including adhesives, gold-silicon eutectic, liquid phase, solid phase and discussed design and reliability issues, particularly with respect to minimizing CTE stresses. In conclusion, he commented that solder technology would not be easily replaced in the high-volume PCB assembly market, although it had, to a large extent, been replaced in die attach, device interconnect and package sealing. There were alternatives to solder for higher temperature applications, but these would need to be considered at an early design stage in conjunction with device and packaging materials, interconnect, layout and production requirements.
The second conference session was concerned with materials processing and assembly. Professor Anthony Walton of the University of Edinburgh presented an overview of the IeMRC "Smart Microsystems" Flagship Project, which focused on the creation of innovative electronic-based systems through the integration of microelectronics with novel material and manufacturing technologies, and involved seven multi-national companies, six SMEs and two trade organizations. Against a background where the typical cost for a 45 nanometre CMOS fab was at least 1 billion pounds sterling, and the price of a set of masks for one device could be 1 million dollars, economics rather than physics was becoming the limiting factor: Many companies could not afford investment to keep up with road map technologies, and the microelectronics industry needed to explore ways of doing innovative things with readily-available, non-leading-edge silicon technology to provide a route back into mainstream production for UK microfabrication within the worldwide microelectronics sector. This was the underlying theme of the Smart Microsystems project and Professor Walton showed examples of micro displays, detectors for telescopes and drug delivery systems, produced by post-processing on CMOS. Work packages included the integration of novel magnetic materials, novel printing technologies, sensors and microfluidics.
Professor Sudipta Roy, of the University of Newcastle-upon-Tyne, described the development of "EnFACE" processes for maskless electrochemical pattern transfer in micro-fabrication. Standard processes typically used a photolithographic resist on the substrate, involved many process steps and necessitated a clean-room environment. The concept of EnFACE was the transfer of a pattern from a photolithograhically patterned counter-electrode tool to a substrate in a single processing step, and up to 40 substrates had been imaged using a single tool. The number of photolithographic operations was reduced by 90 to 95%, and the sustainability of micro-fabricated products was improved as a consequence. In operation, the tool and substrate were placed in close proximity in an electrochemical reactor. When current was passed through the reactor, metal was plated or etched selectively at the areas of the substrate directly facing the uncoated areas of the tool. The technique has been used to fabricate micron scale features in copper or nickel ranging from 10 to 200 microns, with low material and energy consumption. Modelling techniques had been used to simulate the process and to understand the parameters influencing pattern transfer and shape evolution. It had been observed that acidified solutions could not be used, that low metal ion concentrations gave best results and that additives were not required. Pulse current gave better pattern transfer, with cell potentials similar to those used in conventional tank plating, and solution flow was necessary to remove reaction products.
Professor Marc Desmulliez of Heriot-Watt University gave a candid review of the development of a frequency-agile microwave oven bonding system (FAMOBS), from feasibility study to production prototype. The project aimed to manufacture a proof-of-concept device for variable-frequency microwave heating, to improve the production efficiency of the curing of conductive adhesives and encapsulants in semiconductor packaging, which could be installed on the pick-and-place arm of a flip-chip bonding machine and achieve alignment at micron accuracy. Professor Desmulliez gave the details of six generations of prototype and described their limitations and the lessons learned in system integration. The outcome was a new-generation oven with an integrated pyrometer, which had enabled successful curing to be achieved. Using pulsing techniques, the temperature of the material could be controlled accurately during curing, and hotspots and thermal runaway problems avoided.
The theme of Session 3 was printed electronics, and first to present was Dr. Hazel Assender from University of Oxford who introduced the RoVaCBE Flagship project: Roll-to-roll vacuum-processed, carbon-based electronics. There was huge potential market for tagging devices for anti-counterfeiting, brand protection and product tracking applications, and for sensors and displays, which could be developed by exploiting the principles of organic electronics on a roll-to-roll process, and the opportunity existed to produce large areas of simple, low-cost, flexible devices with low environmental impact. Vacuum web processing was a well-established method of manufacturing metallised food packaging, and was capable of being adapted as the basis of a manufacturing process for organic electronics. It also had the potential capability to deposit metals, ceramics and organics in the same in-line process.
Pentacene was chosen as an organic semiconductor, together with organic dielectric deposited by flash evaporation as established in capacitor manufacture. Patterning and registration of the organic layers could be achieved by adaptation of existing technologies. Optimisation of process conditions for the deposition of organic and inorganic thin film multilayer structures were the main technology hurdles to be overcome: In particular, getting the curing conditions right and achieving pin-hole-free coatings, but it had been demonstrated that transistors could be fabricated in a roll-to-roll environment at yield better than 90% using solventless, high-speed processes.Dr. Steve Jones of Printed Electronics Ltd. gave a review of the state-of-the-art of printed electronics, beginning with the question "What is electronics?" He described electronics as being about interconnecting components to form functional devices, it had become so ubiquitous that it had become invisible--people tended to be concerned only with application and functionality. An electronic design was based on a library of component data, many suppliers and millions of man-years of information on function and reliability. Electronics had form, function and purpose, was fit for the purpose for which it was designed and was reliable and durable. By comparison, printed electronics was circuitry created with conductive and/or electro-active inks using a variety of printing techniques--the inks were the components, usually in the form of nanoparticles in a carrier that gave an appropriate surface tension and viscosity for the printing method. Presently there was no library of component data, few suppliers and little information on function and reliability. However, printed electronics was still expected to have form, function and purpose, to be fit for the purpose for which it was designed, and to be reliable and durable. Focusing on inkjet as a versatile technique for depositing functional ink, Dr. Jones described the mechanism of drop formation and deposition--the one-millimetre journey--and commented that most problems were associated with inks: Very few of the materials offered to the market had been found to print or function satisfactorily. He showed several examples of printed electronics on unusual materials and surface contours, remarking that it was feasible to print on almost any substrate imaginable. Inkjet required no tooling, and was a fully additive digital process that offered products and processes virtually impossible by any other means.
Peter Wilson, a third-year Ph.D. student at the University of Surrey, reported some interesting observations of the effects of deposition technique on the electrical and morphological characteristics of PEDOT:PSS [poly(3,4-ethylenedioxythiophene) poly(styrenesulfonate)] used as an alternative to indium-tin oxide in transparent conductor applications. Inkjet coating gave better control and less material wastage than spin coating, but differences had been obseved in the dried coatings. Elegant measuring techniques, such as electroimpedance spectroscopy and electrostatic force microscopy, had been used to determine the effects of solvents and surfactants and substrate temperature on fluid flow and surface and interface evaporation. These all influenced morphology, surface topography and charge conduction. Ongoing work included studies of normal-direction charge conduction as a function of printing parameters, force microscopy to view grain morphology,
Scanning Kelvin Probe Force Microscopy to observe work-function changes as a function of chemistry and processing, characterisation of the effects of annealing on in-plane and normal-direction charge conduction and validating the role of Electro-Impedance Spectroscopy as an analytical method for characterisation of multiple thin-film properties.In the final session, Dr. Matthew Ball, Electronics Programme Manager for the Engineering and Physical Sciences Research Council gave an update on the EPSRC manufacturing strategy and a summary of results from the EPSRC International Review. EPSRC's strategic plan established the fundamental values behind their direction, namely that science and engineering drove the global economy, that science and engineering were key to tackling societal challenges, that EPSRC was at the heart of those efforts, and that EPSRC generated the fundamental knowledge and the skilled people essential to business and government and to other research organisations. The strategic goals of EPSRC were to deliver impact, to shape capability and to develop leaders.
Professor Paul Conway, Academic Director of IeMRC closed the proceedings with a summary of the past year and advice on the presentation of proposals for consideration as future projects.The IeMRC conference was excellent, with a well-chosen programme of outstanding presentations which held that attention of a large audience of delegates from academic institutions and industrial organizations large and small, and provoked some vigorous interactive discussion, both in the lecture theatre and in the networking and exhibition area. The IeMRC team are to be commended for their smooth and efficient management of the event.For more information, visit www.iemrc.org.
More Columns from The European Angle
CircuitData: A New Open Standard for PCB Fab Data ExchangeI Never Realised It Was So Complicated!
The European Angle: Institute of Circuit Technology 43rd Annual Symposium
Ventec International Group's Martin Cotton Celebrates 50 Years in PCB Design
Reporting on the Institute of Circuit Technology Spring Seminar
EuroTech: Raw Materials Supply Chain—Critical Challenges Facing the PCB Industry
EuroTech: ENIPIG—Next Generation of PCB Surface Finish
EuroTech: Institute of Circuit Technology Northern Seminar 2016, Harrogate