-
- News
- Books
Featured Books
- pcb007 Magazine
Latest Issues
Current IssueInventing the Future with SEL
Two years after launching its state-of-the-art PCB facility, SEL shares lessons in vision, execution, and innovation, plus insights from industry icons and technology leaders shaping the future of PCB fabrication.
Sales: From Pitch to PO
From the first cold call to finally receiving that first purchase order, the July PCB007 Magazine breaks down some critical parts of the sales stack. To up your sales game, read on!
The Hole Truth: Via Integrity in an HDI World
From the drilled hole to registration across multiple sequential lamination cycles, to the quality of your copper plating, via reliability in an HDI world is becoming an ever-greater challenge. This month we look at “The Hole Truth,” from creating the “perfect” via to how you can assure via quality and reliability, the first time, every time.
- Articles
- Columns
- Links
- Media kit
||| MENU - pcb007 Magazine
Estimated reading time: 12 minutes
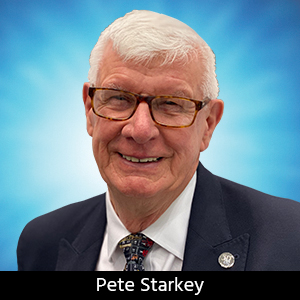
Contact Columnist Form
EIPC's Summer Conference in Milan: Day 1
The Ramada Plaza in Milan, a main industrial, commercial, and financial centre of Italy, was venue for the 2012 Summer Conference of the European Institute of Printed Circuits (EIPC) which drew delegates from 10 European countries, as well as from the U.S. and Israel, to meet, network and learn from an intense two-day programme of 21 presentations and a factory tour.
EIPC Chairman Alun Morgan welcomed everyone and made the opening remarks, reflecting upon the history of Isola, celebrating 100 years since its foundation, and Isola Fabrics, now in its 50th year. He praised the enormous contribution of his predecessor Rex Rozario OBE to the achievements of the Institute, and lamented the passing of Ivan Ho, calling upon all to observe a minute’s silence in his memory.
The first of two keynote addresses came from Hans Friedrichkeit of PCB Network, who took electromobility as his theme “a great opportunity for the European PCB industry.” As an example of evolution in electronics, he compared the Motorola 3200 “Brick” of 20 years ago to the Apple iPhone 5, launched the day before the conference, and the shortly-to-be-available Samsung Galaxy Skin bendable smart-phone. But what of electric vehicles? Had they made equivalent progress? For all of the ambitious projections, the numbers remained relatively small. There was no shortage of justification for electromobility: The world had seen enormous changes in population distribution in the last half-century. Whereas in 1950 world population was around 2.5 billion, there were only two cities with population more than 8 million and over 70% of people lived in the countryside, by 2000 global population had increased to 6.1 billion and 47% of people now lived in cities, of which there were 22 with over 8 million population. The projection for 2050 was for a global population of 9.1 billion with over 70% living in cities and for there to be an increase in “mega-cities” to around 40. Based on these figures, there was a strong argument in favour of electric transportation in urban areas, particularly from an environmental standpoint, and various government incentives had been offered to encourage the uptake. Friedrichkeit quoted figures that indicated that by 2015, Japan, where government incentives were highest, would have 283,000 electric cars, whereas the figure for China was only 110,000. Elsewhere, the numbers were: Italy 8,000, Spain 36,000, Germany 48,000, France 82,000, and the U.S. 236,000. The China figure was surprising, particularly since nearly 30 million electric bikes and scooters had been bought in 2010. But the predicted “green revolution” had not happened, and clearly a breakthrough was needed.
There was no shortage of progress in the development of mechatronic systems for electric and hybrid vehicle propulsion and control, and Friedrichkeit showed many examples. Considering the performance demands on PCBs in these systems, the biggest issue was heat-power dissipation and thermal stress. New MOSFET and IGBT devices operated at temperatures of 150 to 225ºC, but FR-4 laminates were not suitable for operation much above 150ºC. Alternative materials with higher temperature capability such as BT, polyimide and ceramics were many times the price of FR4 and there was an urgent need for cost-effective new laminates capable of long-term service at 170 to 220ºC. Elsewhere in the automotive sector there was continuing rapid evolution of electronic systems: Body, chassis, safety, anti-theft, infotainment, representing substantial ongoing opportunities for the European PCB industry, particularly in Germany.
But what was holding back real growth in electromobility was energy density and battery performance. Although the efficiency of lithium-ion batteries was steadily improving, it still fell well short of what could be achieved with petrol, and costs remained extremely high. Where did the future lie? Friedrichkeit gave a glimpse of a Mercedes concept car with a 10kWh lithium-sulphur battery driving four wheel-engines, supported by a range extender fuelled by hydrogen, a 7.5kg tank-full giving potentially 1,000 km of motoring.
“Do you want the unpleasant truth or comforting lies?” The second keynote speaker was Walt Custer, who presented his business outlook on the global electronics industry. As ever, his meticulous compilation of slides of market data--132 this time, not counting the jokes--flashed past in a vivid blur of information. Although the world economy had shown significant growth from 2010 to mid-2011, conditions had weakened in late 2011 and had not yet recovered. Major issues were Europe’s tighter fiscal policies, squeezed consumer purchasing power and sovereign-debt tensions, high unemployment, and political wrangling in the U.S., China’s rising costs, labour shortages, and weaker exports, and Japan’s strong yen and weak domestic demand. Western Europe was not expected to recover quickly, and the inability of Europe to re-achieve economic traction would hold back overall world progress. World GDP growth for 2012 was expected to reach 2.4%, but the forecast for Europe was -0.4%. And in the electronic equipment sector, against a world growth projection of 2.0%, Western Europe was expected to decline by 2.5%.
Looking at factors affecting the European PCB industry, in particular Germany, Custer quoted Michael Gasch’s comments and noted that the decline in the photovoltaic industry was causing severe price competition in the PV inverter business, and that the automotive industry was still developing well although most of the PCB requirement was now sourced in Asia. Moreover, large manufacturers in Germany had ties in Asia and price pressure was causing them to shift business there. Small manufacturers were suffering a decline in business and the medium-to large manufacturers were seeing up-and-down fluctuations. Purchasing patterns had changed also--as customers realised that capacity was available, they were tending to order at a much later point in time.
Custer’s general conclusions were that although short-term global forecasts were negative, the situation could improve significantly if Europe could resolve its current economic crises, if the U.S. elections were completed and were followed by some positive actions, and if China completed its leadership change and focused on growth. And on a brighter note, recent Eurostat and ZVEI data was showing some positive trends.
EIPC Technical Director Michael Weinhold moderated the first technical session, on innovative PCB technology, and presented the first paper on behalf of Thomas Hofmann, of Hofmann Leiterplatten in Germany. “Heat is the killer of electronics,” he commented as he discussed new PCB technologies for improved thermal management of electronic assemblies. Reviewing the development of PCBs with embedded components since the 1960s, Weinhold defined them as multilayer circuits with active or passive components on inner layers. Different embedding technologies were available and the first patented technology to embed SMD components was registered by Hofmann in 1996. The advantages of embedded components were protection against environmental influences, miniaturisation of the multilayer assembly, replacement of housings, improvement in electrical properties--particularly regarding EMC and, most importantly, improvement of thermal properties. Having listed the thermal conductivities of materials used in PCBs and assemblies, Weinhold demonstrated how embedding a component could theoretically increase its thermal contact area by over 600%, and gave a series of illustrations of experiments showing differences between embedded and equivalent non-embedded devices, using thermal imaging to indicate temperature distribution. He gave some examples of practical applications in automotive lighting and discussed the potential for using component-embedding techniques to develop the system-in-printed-circuit-board SiPCB concept, which would present good opportunities for PCB fabricators to work closely with electronics designers.
Continuing on the theme of thermal management, Norbert Krűtt, CEO of FELA Leiterplattentechnik in Germany described the development of integrated total thermal solutions for power LEDs. In the first instance he demonstrated what could be achieved at no extra cost “save money only by thinking,” with an example of heat management by layout: within the same board area, using the same IMS substrate, just by maximising the pad size on which an LED was mounted, the thermal resistance could be reduced by over 90% and even if a lower-cost, less thermally conductive substrate was used, thermal resistance could be reduced to 1/3 of the original. Heat management was also critically dependent on making the right choice of dielectric, and striking a balance between thermal conductivity and dielectric strength. Krűtt gave an example where a 150-micron dielectric of thermal conductivity 4.0 W/mK had a higher thermal resistance than a 25-micron dielectric of thermal conductivity 1.0 W/mK.
Krűtt saw FELA as much more than a PCB manufacturer. Where thermal management was concerned they were a system provider who supplied custom-engineered solutions. FELA did not buy-in IMS materials--everything was fabricated in-house, giving unlimited permutations of construction together with the assurance that material quality and reliability was fully under their own control. He showed many examples of thermal management applications where the emphasis was on innovative and cost-effective design.
Embedded power electronic modules for automotive applications was the subject of the presentation of Lars Bőttger from Fraunhofer Institute in Germany. Embedding power chips gave many advantages in terms of improved reliability, improved heat transfer and shielding capability. The replacement of bond wires by plated thick copper connections resulted in low inductances and created opportunities for 3-D packaging. Assembly techniques fell into two main categories: face-up and face-down. Fraunhofer favoured the face-up approach and had installed a processing line in Berlin capable of handling 18” x 24” panels for development of new substrate and embedding technologies. Bőttger showed many examples including embedded power-MOS packages, power chip packages and a power-in-system package with 9 embedded MOSFETs in three layers of stacked chips.
There had been significant developments in the field of power electronics in high-current PCBs for electric vehicle applications, through a collaborative project known as Hi-Level, and a motor control module had been realised with the capability to switch power greater than 10 kW. This incorporated 12 IGBTs embedded in a power PCB with heavy copper inlays and the overall construction was thin enough to attach directly to the motor. One challenge had been to develop a pressure-less technique for die attach and a process based on low-temperature sintering of silver paste had given successful results. Embedding technology offered a solution which was applicable to many different types of power device using the same manufacturing line and, particularly for automotive applications, the technology had great potential for cost reduction and improved reliability.
Another presenter with a keen interest in the consequences of increasing power density was Bill Burr, from BPA Consulting in the UK. His title was “The Heat is On – MiB Comes of Age.” Together with his BPA colleague Nick Pearne, Burr had been researching the market in a project they termed Metal-in-the-Board, MiB. Increasing power density in electronic devices in general, and the rapidly increasing utilisation of electronic control of electrical power opened up a new generation of opportunity for innovation in thermal management, particularly in solid state lighting, green power, automotive and electro-mobility applications. MiB technologies were structures added to conventional circuit boards to provide enhanced thermal and power management. Many alternatives were available--a whole new family of acronyms: MLBTV, MLBIL, MBB, TCMLB, HCPCB, DWPCB to name but a few--which could be realised by the PCB manufacturer, whom Burr saw as a translator standing between the material supplier and the subsystem manufacturer, understanding the languages of both sides and turning materials into electronic function. Looking specifically at the solid-state lighting business, he identified a hidden hole which could be the source of big opportunities for the PCB industry. Quoting the Haitz postulate: “The cost per lumen falls by a factor of 10 and the amount of light generated per LED package increases by a factor of 10 every decade.” He predicted that the evolution of high-brightness LEDs would completely change the way lighting was designed and used. They offered illumination at a fraction of the power of the incandescent equivalent, with at least an order of magnitude increase in working life. This might be bad news for manufacturers of light bulbs, but was not necessarily good news for manufacturers of LEDs. Instead of replacing light bulbs every 1,000 hours, LEDs would rarely, if ever need replacing.
“Desperation drives innovation”--sales would stall unless something was done to radically change the industry. Burr believed that new lighting and architectural concepts would integrate form, space and illumination. New applications would emerge and the solid-state lighting business would morph into a PCB maker’s dream…
The importance of base materials for high-speed digital applications was emphasised by Mario Scari, managing director of Isola Fabrics in Italy, the only weaver of glass fabrics in Europe. As high-speed digital applications approached mainstream status in terms of numbers of designs implemented, they presented a series of challenges to the performance of available materials and his graph of loss versus cost clearly illustrated that traditional low-loss materials carried a high price premium. What could be done to improve the properties of existing materials? He quoted Lee Ritchey: “By simply changing the style of glass used in the laminate, the problems of varying impedance and velocity have been substantially reduced,” and showed the difference between a standard fabric, where the glass yarns remained in tight bundles with large spaces in between, and one with spread fibres, where the distribution of glass was considerably more uniform. A new generation of fabrics had been developed. For example, 1067 was the spread equivalent of 106, 1086 the spread equivalent of 1080 and 3113 the spread equivalent of 2113. Scari discussed factors affecting chemical-thermal behaviour at the interface between glass and resin, how these could be improved during the weaving and finishing processes, and how multifunctional silanisation finishes could be applied to suit different resin systems. Looking at the glass itself, E-glass was still the mainstream material. Other types were available with different dielectric characteristics but at greatly increased prices.
A late addition to the programme was a presentation by Jean-Claude Roth entitled: “Films for Advanced PCBs.” In this context, films were fabric-free cured and semi-cured dielectric materials, traditionally used in flex constructions and offering an alternative to liquid dielectrics. Roth described some applications: Pad cratering was a topical industry issue and most work-arounds to date had proved counter to the need to increase board density. If a fracture-resistant film was used on the outer layers of the PCB, the BGA pads were in direct contact with a resilient layer and pad-cratering effects were greatly reduced. Films were available specifically developed for HDI applications, with properties that enabled z-axis spacings to be reduced to as little as 12 microns without risk of shorting between layers. New polymer chemistries ensured that films met and exceeded current thermal and electrical requirements. Films could be used alone or in combination with traditional glass-based materials. They had better breakdown voltage performance than traditional prepregs and were capable of improving transmission line performance.
The first day’s proceedings concluded with a visit to the factory of Isola Fabrics in nearby Brugherio, where conference delegates had the opportunity to see at first hand the warping, sizing, weaving, de-sizing, and silanisation processes in high-volume production.
The conference dinner in the evening provided a taste of Italian cuisine and an excellent networking opportunity, then early to bed for a bright start to the second day.
More Columns from The European Angle
CircuitData: A New Open Standard for PCB Fab Data ExchangeI Never Realised It Was So Complicated!
The European Angle: Institute of Circuit Technology 43rd Annual Symposium
Ventec International Group's Martin Cotton Celebrates 50 Years in PCB Design
Reporting on the Institute of Circuit Technology Spring Seminar
EuroTech: Raw Materials Supply Chain—Critical Challenges Facing the PCB Industry
EuroTech: ENIPIG—Next Generation of PCB Surface Finish
EuroTech: Institute of Circuit Technology Northern Seminar 2016, Harrogate