-
- News
- Books
Featured Books
- pcb007 Magazine
Latest Issues
Current IssueInventing the Future with SEL
Two years after launching its state-of-the-art PCB facility, SEL shares lessons in vision, execution, and innovation, plus insights from industry icons and technology leaders shaping the future of PCB fabrication.
Sales: From Pitch to PO
From the first cold call to finally receiving that first purchase order, the July PCB007 Magazine breaks down some critical parts of the sales stack. To up your sales game, read on!
The Hole Truth: Via Integrity in an HDI World
From the drilled hole to registration across multiple sequential lamination cycles, to the quality of your copper plating, via reliability in an HDI world is becoming an ever-greater challenge. This month we look at “The Hole Truth,” from creating the “perfect” via to how you can assure via quality and reliability, the first time, every time.
- Articles
- Columns
- Links
- Media kit
||| MENU - pcb007 Magazine
Estimated reading time: 8 minutes
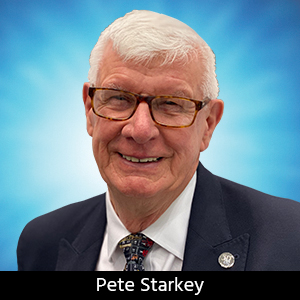
Contact Columnist Form
An Inside Look: SMART Group's "Back to Basics" Workshop
It would be a perfect world if electronics assembly processes could consistently achieve 100% yield without the need for rework and repair. In real life, rework is an essential activity in even the best-run production facilities. The task becomes increasingly difficult when fine pitch components, BGAs, LGAs, and QFNs are involved and it is critical that, whatever rework may be necessary, it is done right, with the right tools and the right skills, with confidence that the finished product will be fully reliable.
Over 30 line managers, process and quality engineers braved freezing weather to travel from far and wide to the Manufacturing Technology Centre in Coventry, UK, to get the benefit of first-hand experience from top industry experts at SMART Group’s rework and inspection workshop, moderated by Technical Committee member Jason O’Dell, managing director of O’Dell Rework Solutions.
Patrick Webb, Technology Manager of Electronics Manufacturing, welcomed workshop participants to the Manufacturing Technology Centre (MTC), a purpose built facility opened in 2011 with the objective of bridging the gap between academia and industry by providing an environment for the development and demonstration of innovative manufacturing processes and technologies on an industrial scale. “We take bright ideas and convert them into viable processes that can be transferred into industry. Our members can push the boundaries of innovation through testing the practical applications of equipment in the workshop.” Electronics manufacturing was one of seven specialist disciplines within MTC.
The first workshop presenter was IPC Certified trainer Paul Pidgeon of STEM Training, who gave a “Back-to-Basics” tutorial on hand soldering. Starting from first principles, and with many practical illustrations and realistic examples, he discussed the fundamentals of the soldering process, the interactions of metals, the role of flux, the formation of intermetallic bonds, and the effects of too little or too much heat. He then went into the details of hand-soldering technique: how to select the appropriate tip size and shape for a particular application and how to keep the tip in good condition, how to set the at-rest temperature for different solders--315°C to 380°C for tin-lead, 360°C to 430°C for lead-free, where he added, “start with the lowest temperature you can get away with,” how the solder station compensates for the heat loss when the tip meets the job, how to feed solder into the joint, when to use additional flux, and how and when to remove the tip from the joint. Pidgeon noted that, “Creating a solder joint is an art form!”
He explained the differences between clean and no-clean fluxes and how to remove residues, then discussed inspection and acceptance to company standards or to international standards such as IPC-610 and J-STD-001.
Pidgeon listed 20 variables which could affect the effectiveness of the soldering operation, including tip shape, tip size, tip idle temperature, quantity of flux, type of flux, quantity of solder, solder wire gauge, type of solder alloy, ambient air temperature, size of the component, solderability of the component terminations, density of the PCB, design of the PCB, pre-soldering temperature of component and PCB, angle of the tip, position of the tip, power of the solder station, quality of the soldering iron, soldering dwell time, and cleanliness of component and PCB. Pidgeon explained that most people just turn the temperature up and described practical ways of overcoming soldering difficulties. His essential advice was: “Be patient, take your time, practise, learn from the experience, and gather knowledge.”
“AOI and Rework” was the topic of the next workshop session, presented by Graham Penson of TestSolve. He pointed out the limitations of traditional manual inspection, particularly when old-fashioned yellow arrow-stickers got displaced or went missing, and discussed the benefits of automated optical inspection, what equipment was available, and where and when to use it. After reviewing the different options available for AOI, from basic desk-top systems through magazine-fed off-line systems to pass-through on-line systems, he discussed where it was appropriate to incorporate AOI into the assembly process-flow: post-solder paste, pre-reflow and post-reflow, he discussed procedures for dealing with faults identified and their associated data. It was essential that boards were serial-numbered or bar-coded so that the right data could be recalled at the rework station, with a board map to show where faults were located, and “good” and “bad” images for reference. In terms of process-control feedback and AOI performance analysis, it was debatable whether to keep all calls--true or false--or only those validated by the operator, and whether to record high-resolution images of faults, for future analysis. Provided there could be confidence in near-zero false calls, other considerations were the relative merits and practicalities of live versus post-process final inspection, balancing the conflicting issues of line interruption versus correctable error resolution, and maintaining flexibility for low-volume high-mix operations.
Dr. David Bernard, product manager, X-ray Systems at Nordson Dage, described the non-destructive opportunity offered by real-time X-ray to inspect what could not been accessed by optical systems--solder joints on BGA and QFN devices, voids, head-on-pillow defects, excess solder, extent of solder fill of plated through holes, and defects within component package. And X-ray was becoming an increasingly important technique in the detection of counterfeit components. Dr. Bernard explained the fundamental principles of an X-ray system and demonstrated how manipulation of the detector position enabled oblique views and image magnification. Of the three types of X-ray tube available, the sealed transmissive tube gave best resolution and clarity. Two types of detector could be used: the flat-panel detector was useful for fast live imaging of low density objects, whereas the high-end image intensifier was preferred for highest magnification and resolution. He showed many examples of defects revealed and identified by X-ray then got into the debate about whether voiding in solder joints was good or bad, citing several arguments for and against, and using IPC-610E and IPC 7095 for reference. Whatever the opinion of voids, the certain way to locate and quantify them was by X-ray. His concluding advice to prospective purchasers of X-ray equipment was to “try before you buy,” and consider the relative merits of tube, detector, system, and software to ensure the best combination for their particular inspection applications.
Between morning and afternoon workshop sessions, Patrick Webb gave a guided tour (pictured above) of the superbly equipped and immaculately presented surface-mount assembly shop at MTC, explaining it as a production-scale facility dedicated to proof of manufacturing readiness--an integrated and automated process line as a test bed for expanding operational performance. “We have the facility to play around and look at the more wacky things without risking production.”
After lunch, Graham Dickson from Gen3 Systems gave an overview of the tools available for manual optical inspection, from bench-top magnifiers, through binocular microscopes and stereo microscope systems, to analogue and digital CCD cameras in hand-held and work-station configurations, with image capture and video capture. Remarkable results could be achieved in BGA inspection, using cameras with prism lenses capable of looking under even low stand-off devices. High-definition auto-focus cameras with laser pointers and nominal x10 magnification with controllable zoom were very popular for in-process and rework inspection and, with the benefit of a TV monitor, were particularly useful for training exercises.
The final session was presented by workshop moderator Jason O’Dell, who began with the question: “Does your team have what it takes to rework BGAs and QFNs?” and continued by describing the range of specialist rework equipment available--infra-red, hot air, vapour phase, and laser. IR systems gave good control and easy access, although some low-end systems could be very operator-dependent; hot air systems were in widespread use, but required package-specific shields and nozzles; laser and vapour phase systems tended to be too expensive for general use. He personally favoured the focused infra-red system, with a halogen-bulb heat source.
O'Dell suggested that workshop participants examine the requirements of their individual rework tasks, present and future, before committing to investment in equipment. What were the characteristics of their production? High- or low-mix, long- or short-run, whether it was justified to invest in tools such as shields and nozzles for specific component packages, whether the rework parameters would be set-up by process engineers or operators, whether the equipment was easily maintained and calibrated, with good support from the manufacturer, whether it could be easily and cost-effectively upgraded for the future, whether it was capable of real-time in-process temperature monitoring and feedback, and whether it would accommodate the largest and smallest PCBs and components?
He then considered the precautions to be taken before embarking on a rework job: Removal of batteries and ignitable materials, ensuring effective mechanical support, checking whether pre-baking was required, as well as choosing appropriate pre-heat and profile conditions. He made particular reference to chemistry: Choosing the right paste and flux, making sure that they came from a reliable, traceable source and that they were within shelf life. The next consideration was the means by which components would be removed: hot air systems relied on mechanical grippers via the shield; infra-red systems needed a vacuum pick-up mechanism.
Decisions to be made before placing and soldering a replacement component included whether to flux the board or the device, the feasibility of printing paste locally on a densely populated board or whether to paste the component itself using a nested rework stencil, whether to re-ball BGAs or to print paste directly on to the device. O'Dell discussed gel-flux dipping and paste dipping, emphasising that paste for this operation was much more fluid that that used for printing, and precautions with fine-pitch BGAs. Next consideration was achieving accurate alignment using a split-beam prism system to enable the BGA and the pad pattern to be viewed simultaneously at typical magnification of x70, and finally how to monitor temperature using thermocouples or non-contact methods.
There was plenty of interactive discussion throughout the day and those present had a great opportunity to broaden their knowledge of good rework practice by learning from the experiences of the expert presenters and by networking with their counterparts in the industry. Another excellent SMART Group event, a credit to those who organised it, and acknowledgement to MTC for providing a most appropriate venue.
More Columns from The European Angle
CircuitData: A New Open Standard for PCB Fab Data ExchangeI Never Realised It Was So Complicated!
The European Angle: Institute of Circuit Technology 43rd Annual Symposium
Ventec International Group's Martin Cotton Celebrates 50 Years in PCB Design
Reporting on the Institute of Circuit Technology Spring Seminar
EuroTech: Raw Materials Supply Chain—Critical Challenges Facing the PCB Industry
EuroTech: ENIPIG—Next Generation of PCB Surface Finish
EuroTech: Institute of Circuit Technology Northern Seminar 2016, Harrogate