-
- News
- Books
Featured Books
- pcb007 Magazine
Latest Issues
Current IssueThe Hole Truth: Via Integrity in an HDI World
From the drilled hole to registration across multiple sequential lamination cycles, to the quality of your copper plating, via reliability in an HDI world is becoming an ever-greater challenge. This month we look at “The Hole Truth,” from creating the “perfect” via to how you can assure via quality and reliability, the first time, every time.
In Pursuit of Perfection: Defect Reduction
For bare PCB board fabrication, defect reduction is a critical aspect of a company's bottom line profitability. In this issue, we examine how imaging, etching, and plating processes can provide information and insight into reducing defects and increasing yields.
Voices of the Industry
We take the pulse of the PCB industry by sharing insights from leading fabricators and suppliers in this month's issue. We've gathered their thoughts on the new U.S. administration, spending, the war in Ukraine, and their most pressing needs. It’s an eye-opening and enlightening look behind the curtain.
- Articles
- Columns
- Links
- Media kit
||| MENU - pcb007 Magazine
Estimated reading time: 4 minutes
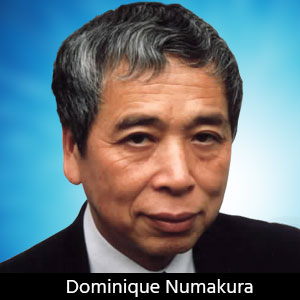
FINETECH JAPAN 2016
A fresh new slate is offered to all Japanese students in April. Some students start a new academic year in April, while others have graduated and are ready to begin their careers. Many Japanese companies begin a new fiscal year in April, and the spring trade show season begins. First up is the 26th Flat Panel Display Expo (FINETECH JAPAN).
The three day show began on April 6th at Tokyo Big Sight. Related show events held concurrently included the 7th Film Tech Japan, 5th Plastic Japan, 16th Int’l Laser & Photonics Expo (Photonix 2016), 3rd Metal Japan and 1st Ceramic Japan. Exhibit space was sold out and reserved by mostly manufacturers; many companies hailed from Korea and Taiwan. You can usually count on a few colleges or universities in attendance; however, this year no academic institutions reserved space.
There is a technological clash between LCDs and OLEDs, and I was expecting to see some innovative presentations from both of these groups, but I was very disappointed. After I thought about it, I realized that many Japanese panel manufacturers are scaling down their business operations. They were forced to because of the fierce competition from their Korean, Taiwanese and Chinese counterparts. Manufacturers from these three companies did not showcase their newest technologies; they kept a low profile. On the other hand, a couple of second-tier display module manufacturers from Taiwan presented a few innovative technologies. The technologies were not aimed at the premium product market. Their products offered a cost-effective alternative for modules in small- to mid-sized size applications (these were probably the hit of the show).
Companies affiliated with chemicals, materials and equipment manufacturing were the primary ones in attendance. Their product lines had nothing to do with panel displays, but they still reserved large booths and presented an array of new technologies. Their focus was not to introduce new or unique products; their strategy was to offer improvements to existing products. Typically in the case of film products, the manufacturers presented a smaller thickness, higher heat resistance, longer flexing endurance, smaller loss with high frequency, higher dimensional stability and more. These companies were not expecting a huge amount of business; their goal was to engage some potential customers for a future business relationship. A marketing representative from a large company told me their goal was to offer many products with hopes of attracting one customer with future product application needs. A market researcher told me that it is the reason why they were introducing many new products during the exhibition for the scouting.
I saw a very unique product called transparent polyimide. Two companies showcased transparent resins, films, copper laminates and flex circuit applications. These companies don't expect this to be used in applications such as touch panels because of its higher costs compared to PET based products. They are expecting to make money from industrial and medical applications that require heat resistant optical devices.
There was not anything that really popped out at the show. Most of those that visited the exhibition were affiliated with the chemical and material industry, and they were looking for a few new business avenues. Unfortunately for those who reserved space, this means there were no new customers. Everyone in Japan is trying to scratch out a living. No one has thrown in the towel yet, and they all need one lucky break. I believe the harder you work, the luckier you get; I am optimistic that the Japanese electronics industry will see better days ahead.
Page 1 of 2
More Columns from EPTE Newsletter
EPTE Newsletter: Travel to Japan During COVIDEPTE Newsletter: A New COVID Surge in Taiwan?
EPTE Newsletter: COVID-19 PCR Test in Japan
EPTE Newsletter: Japan Failing in Vaccine Distribution
EPTE Newsletter: A Long Trip to the U.S.
EPTE Newsletter: Ten Years After Fukushima
EPTE Newsletter: Taiwan Releases 2020 PCB Production Numbers
EPTE Newsletter: The Printed Circuit Industry in China