-
- News
- Books
Featured Books
- smt007 Magazine
Latest Issues
Current IssueWhat's Your Sweet Spot?
Are you in a niche that’s growing or shrinking? Is it time to reassess and refocus? We spotlight companies thriving by redefining or reinforcing their niche. What are their insights?
Moving Forward With Confidence
In this issue, we focus on sales and quoting, workforce training, new IPC leadership in the U.S. and Canada, the effects of tariffs, CFX standards, and much more—all designed to provide perspective as you move through the cloud bank of today's shifting economic market.
Intelligent Test and Inspection
Are you ready to explore the cutting-edge advancements shaping the electronics manufacturing industry? The May 2025 issue of SMT007 Magazine is packed with insights, innovations, and expert perspectives that you won’t want to miss.
- Articles
- Columns
- Links
- Media kit
||| MENU - smt007 Magazine
Estimated reading time: 9 minutes
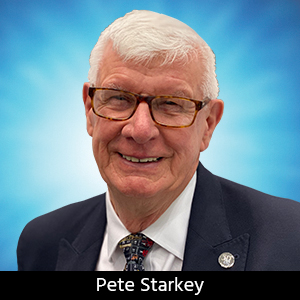
Contact Columnist Form
An Inside Look: 3D AOI of Electronic Assemblies Seminar
The prestigious Manufacturing Technology Centre in Coventry, UK, was an appropriate venue for SMART Group’s seminar on 3-Dimensional Automated Optical Inspection of electronic assemblies, “3D AOI." The event brought together experts from leading AOI suppliers, to discuss and explain different approaches to three-dimensional inspection and to present the latest in technology to an attentive audience of engineers from the electronics manufacturing industry with a collective interest in yield improvement, process control, and quality assurance. All were welcomed by SMART Group Chairman Keith Bryant, who introduced the speakers and moderated the panel discussions.
“Putting 3D into Perspective” was the scene-setting theme of the first presentation, from Andy Bonner, managing director of NordsonYestech Europe, who demonstrated how AOI technology had evolved from the mid-1990s to the present day. “Test and Inspection--who needs it?” was a rhetorical question as he described how AOI began to take the place of in-circuit testing once confidence in the quality of integrated circuits had improved to the point where their functionality could be consistently expected. The weaknesses of early AOI machines were low data processing power, limited lighting capability and analogue top-down cameras. Systems were used to check for component presence and orientation, and the presence of solder.
Lighting progressed from plain white through added coaxial red light, which could show up tombstoning, to RGB phased lighting with arrays of different-coloured LEDs at different angles which gave some information on topography, for example the shape of a solder joint. The next step into the third dimension was to use a series of angled high-resolution cameras, which could for example look at IC packages from the side and see leads and solder joints out-of-sight of the top-down camera. A typical configuration for the inspection of assemblies had five cameras with resolution from 25 down to 8 microns and simultaneous image capture. To measure the height of components and features accurately, the options were laser or moiré optical techniques, or a combination of both. Now, with clever software, “Real 3D” was possible--3D systems could be integrated with 2D applications and optimised for speed and repeatability, with fast programming and easy updates for component changes during production.
So what could be achieved with AOI other than just funding faults? Bonner listed yield improvement through feedback to the line, historical data, production statistics, and designer and supplier feedback.
Gary Leong, director of business development with ViTrox, remarkably bright-eyed after a 14-hour flight from his base in Malaysia, gave an informative presentation entitled “Capturing lifted lead, coplanarity and missing component defects effectively with 3D AOI.” Reflecting on his early career as a post-reflow inspector, he was concerned for his future when the company invested $300,000 in an AOI machine. In fact his job was just the same--his boss saw him as an insurance policy--because placing the machine post-reflow still left the opportunity for many in-process defects and the machine, with top-down cameras, gave too many false calls and missed defects such as lifted leads, missing components, coplanarity and foreign material in unpopulated areas. Fifteen years on, today’s 2D + 3D combination systems were capable of consistently detecting these defects, the 2D functions revealing missing, offset, skewed, wrong part, wrong polarity, billboard and tombstone components, lifted or bent leads, excess or insufficient solder, and solder bridging, complemented by the 3D functions measuring package height and coplanarity to an accuracy of 2 microns.
Page 1 of 4
More Columns from The European Angle
CircuitData: A New Open Standard for PCB Fab Data ExchangeI Never Realised It Was So Complicated!
The European Angle: Institute of Circuit Technology 43rd Annual Symposium
Ventec International Group's Martin Cotton Celebrates 50 Years in PCB Design
Reporting on the Institute of Circuit Technology Spring Seminar
EuroTech: Raw Materials Supply Chain—Critical Challenges Facing the PCB Industry
EuroTech: ENIPIG—Next Generation of PCB Surface Finish
EuroTech: Institute of Circuit Technology Northern Seminar 2016, Harrogate