-
- News
- Books
Featured Books
- pcb007 Magazine
Latest Issues
Current IssueInner Layer Precision & Yields
In this issue, we examine the critical nature of building precisions into your inner layers and assessing their pass/fail status as early as possible. Whether it’s using automation to cut down on handling issues, identifying defects earlier, or replacing an old line...
Engineering Economics
The real cost to manufacture a PCB encompasses everything that goes into making the product: the materials and other value-added supplies, machine and personnel costs, and most importantly, your quality. A hard look at real costs seems wholly appropriate.
Alternate Metallization Processes
Traditional electroless copper and electroless copper immersion gold have been primary PCB plating methods for decades. But alternative plating metals and processes have been introduced over the past few years as miniaturization and advanced packaging continue to develop.
- Articles
- Columns
Search Console
- Links
- Media kit
||| MENU - pcb007 Magazine
Estimated reading time: 5 minutes
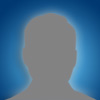
Contact Columnist Form
Slash Sheet Chaos: Is What You See, What You Get?
With the demise some years ago of MIL-S-13949 during the "commercialization" of military procurement--when then Secretary of Defense William Perry instituted moving to "best commercial practice"--our industry lost something that a few of us were concerned about then, and that maybe still should be cause for some concern. I think most OEMs were disturbed to discover that while IPC 4101 was taken more or less intact from MIL-S-13949, there is now no enforcement or validation of certifications to IPC-4101 slash sheets. Changing materials based purely on slash sheets can be hazardous when considering a new supplier or unproven product. Moreover, periodic audits by an independent auditor (DESC) gave a sense of quality system stability, and the annual required testing and data submission on each material approved to the QPL for MIL-S-13949 provided an ongoing assurance of product performance.
I had a number of long discussions with my old friend Dick Grannells, of Hamilton Standard in Connecticut, about the "Perryization" of laminate and prepreg specifications, and we both would have preferred to have retained the MIL-S-13949/DESC audited approach. Perhaps that's a bit of "good old days" nostalgia on the part of an "Alz-Timer," but, in the real globalized world of the twenty-first century, I wonder if the risk that you won't get what you think you ordered is increasing.It is possible to take a lot of liberty with interpreting slash sheets, sometimes ignoring the header definition on chemistry or filler. For example, it has been known for suppliers to certify the same polyimide product to IPC-4101/40, /41 and /42, convenient when a customer orders solely by slash sheet designator and a supplier has only one product, but potentially dangerous since /42 specifications are mutually exclusive of /40 and /41 by definition since the properties of, for instance, blended polyimides are not the same as pure polyimides. How certain can you be when you change suppliers, based on price, that the product you are getting is the same kind of polyimide you have been using and not some sort of blended, filled or otherwise-modified variant with compromised properties?
Blended materials do not necessarily copolymerize to form a homogeneous final product. Work performed some years ago suggests that, during thermal cycling, it is possible for discrete domains of the two blend components to develop cracks--almost like "grain boundary" failure in metals--which can weaken the physical and deteriorate the electrical properties of the composite. The presence of fillers, used to reduce cost or to "extend" the resin system, can also affect or enhance properties. These differences make it critical to understand not only the industry specifications, but the details behind the materials being qualified. If your supplier is not willing or able to tell you how their product differs from the "standard" polyimide you are using, it may very well not be. Luckily, it is possible to evaluate some of these things by doing some basic analysis. In fact, it wouldn't be a bad idea to use the Ronald Reagan U.S./Soviet mutual disarmament principle: "Trust, but verify." IR spectrophotometry, for instance, can detect the "fingerprint" of epoxy reactive groups in polyimide prepreg. Dynamic mechanical analysis can determine whether the fully-cured resin system is mechanically significantly different from a control. thermo-mechanical analysis (TMA) may be able to detect dual Tg's in a cured two-component product.
That doesn't even begin to touch on the confusion about what is "FR-4." "Families" of FR-4 products can be cross-certified to a variety of slash sheets, and ordering "FR-4," without getting very specific, could be an interesting exercise in chaos. In the end, a slash sheet and material specification is a baseline tool that we need to have, but the principle of "Caveat Emptor" ("let the buyer beware") is especially important today with the plethora of materials all being certified to a somewhat confusing panoply of pro-forma "specifications" that never seem to quite specify enough. With over 50 IPC slash sheets, and the complications arising from what is "lead-free" and what is "green" further multiplying the number of possible slash sheets by which "FR-4" products can be designated, designers, manufacturers and material suppliers all need to be speaking the same language when materials are specified and purchased. All this, of course,begs the question: "Do we really need all these FR-4 variants?"
Do your homework! It has been said that there is always someone willing to sell a product that is cheaper, and those who buy only on price are that man's legitimate prey. Don't be a victim of slash sheet confusion. Ask for and expect your suppliers to provide clean and real differentiations between their products. Make sure that when you buy a lower cost "alternative" that it is really the same thing you've been using. It is possible for legitimate competitors to have different cost/price structures for truly equivalent products--just make sure that's what you're looking at. Don't find out after a few thousand thermal cycles that /40, /41 and /42 (with and without filler!) really are different products and perform differently in service. If there are good reasons for differentiated designations, make sure you are not being deceived by the data sheet!
Chet Guiles is a graduate of the University of New Haven with a BA in Chemistry (1971) and of the Syracuse University Eastern European languages Institute in Russian Language (1963, while on active duty with the USAF). Subsequent to his military service, Chet worked in the areas of corrosion metallurgy (Olin Metals Research), and PVC and silicone rubber technology (Automation Industries). Prior to joining Arlon in 1979, Chet worked as a Senior Research Chemist at Pennwalt Corporation performing research on PVC stabilization.At Arlon, Chet has served in a number of roles including Technical Manager for the Silicone Rubber Group in DE, Quality Assurance Manager for the Delaware Microwave Materials operation, Division Technical Director and, most recently, as Director of New Business Development for the Electronic Substrates Division. Retired in 2004, Chet now acts as a part-time consultant to Arlon.Chet has several U.S. Patents and has written and published widely over the past 30 years in the area of materials for PCBs.
More Columns from Various Archived Columns
Moisture in Materials: Avoiding Process GremlinsMaterial Witness: Beat the Heat--A Non-Math Intro to Thermal Properties
Material Witness: Considerations in Using TC Materials for PWBs
Material Witness: Are Your Materials Up to the Challenge?
Material Witness: Thermal Oxidation of Materials, Part I
Material Witness: Thermal Oxidation of Materials, Part II
Material Witness: R.I.P. Speedboard C
Conversations with...Integrated Micro-Electronics Inc.