Estimated reading time: 15 minutes
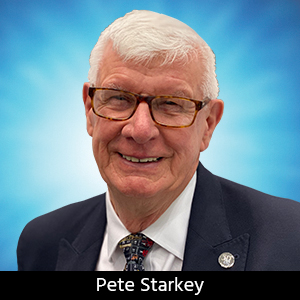
Contact Columnist Form
EIPC's Summer Conference in Milan: Day 2
A big blue sky greeted delegates as they returned to the Ramada Plaza for Day 2 of the EIPC Summer Conference in Milan, Italy. Downstairs in the conference area, EIPC Vice President of Technology, Professor Martin Goosey, welcomed them back and introduced the opening session, the theme of which was collaborative research projects.
Professor Goosey remarked that many SMEs did not have the resources to carry out research independently and that collaboration in R&D activities was a good way of bringing together the disparate skills needed for many complex PCB-related projects. EIPC had been involved for many years and recognised many benefits: direct engagement in the development of new technologies, projects in which members could participate, access for members to outcomes and results, support for the European PCB and electronics industry and, not least, a source of funding for EIPC.
Recent successful projects in which EIPC had participated were Ionmet, Prosurf, and Surfenergy. The Aspis project was ongoing, Susonence and Mesmoproc were in their early stages, and the proposal had just been submitted to develop a process for metals recovery from PCB manufacturing effluent using waste products from the seafood industry.
The successful outcome of one of the completed projects, Surfenergy, was the subject of the first presentation, from Stuart Dalrymple of C-Tech Innovation in the UK. The objective of Surfenergy had been to support the introduction of energy-efficient measures by SMEs in the PCB manufacturing sector, reduce energy costs and environmental impact, and to make informed decisions on investments. An Energy Efficiency Advisor Toolkit was now available and Dalrymple went step-by-step through the stages of using it to set up and operate an energy management system, describing the tools, audit procedures, and key performance indicators that could be used to identify energy-saving opportunities. Intelligence had been gathered on technologies, know-how and other measures with the potential to reduce energy consumption. The toolkit could be accessed free-of-charge on the Surfenergy website, and there were already 4,000 users.
Dr. Karl Ryder from University of Leicester in the UK was a participant in the Aspis project, aimed at developing more reliable alternatives to standard electroless nickel immersion gold PCB finishes. University of Leicester’s contribution to the project was to study immersion gold processes based on novel types of ionic liquid electrolyte known as deep eutectic solvents. He outlined the rationale for choosing to explore the potential benefits of ionic liquid formulations in this application and explained the basic electrochemistry that caused solutions of metal salts to behave differently at metallic surfaces. The objective was to avoid the hypercorrosion effects associated with aqueous immersion gold on nickel, and to deposit gold from a considerably more benign environment. Immersion gold had been deposited on a standard aqueous electroless nickel surface from solutions in a deep eutectic solvent based on choline chloride and ethylene glycol. Three different gold salts had been used: gold chloride, gold cyanide, and potassium cyanoaurate, and their electrochemical behaviour had been studied. A standard aqueous solution based on citric acid had been used as a control. Plating rates had been measured with a quartz crystal microbalance, and an atomic force microscope had been used to measure deposit roughness. Corrosion effects had been studied by stripping the gold and examining grain boundaries in the underlying electroless nickel. It had been demonstrated that immersion gold deposited from the gold cyanide--ionic liquid formulation was bright and uniform in appearance, and gave faster and more reliable solder wetting than the equivalent deposit produced using the aqueous control formulation.
Dr. Andy Cobley, from Coventry University in the UK, discussed the results from an IEMRC-funded research project named ULTEIMet. A combination of electrochemical and laboratory plating tests had been carried out to determine whether ultrasonics would enable electroless copper plating to be carried out at reduced temperatures. Initial studies using a proprietary electroless copper formulation had examined the effect of ultrasound of different frequencies on the stability of the bath. 40KHz had been chosen as the working frequency for plating-rate experiments as it caused no spontaneous precipitation of copper. Plating rates were measured over a range of operating temperatures, with and without ultrasonic agitation, and only slight increases were observed when ultrasound was applied from the start of the process. It had been shown that, in the early stages of deposition, ultrasonic agitation was tending to scrub the palladium activator off the surface and reduce the plating efficiency. When a delay was introduced to enable complete initiation before the application of ultrasound, a significant increase in plating rate was observed such that the process could effectively be operated with a 5ºC reduction in bath temperature. Furthermore, ultrasonic agitation had been observed to result in better coverage and to yield a finer-grain deposit with improved mechanical properties.
Dr. Chris Hunt, leader of the Electrical Interconnection team at the National Physical Laboratory in the UK, described a new approach to studying conductive anodic filament (CAF) formation, a significant failure mechanism in PCB assemblies. CAF was an electrochemical process which resulted in corrosion products growing along glass-resin interfaces with the PCB. A combination of five conditions caused CAF to occur: Ionic species to act as electrical charge carriers, moisture to dissolve the ionic material, an acid environment around conductors to initiate copper corrosion, a pathway for the ions to move, and an electrical bias to act as a driving force for ion transport. To study the different variables separately, it was necessary to be able to grow CAF in a controlled way, and a Simulated Test Vehicle had been designed and developed. This was based on a thin polyimide substrate with a 2-ounce copper conductor pattern, across which glass strands could be laid and encapsulated with different resin systems by applying them from solution then drying and curing. Another version of the test vehicle had a drilled hole to facilitate the application of process solutions of different concentrations. A matrix of tests had been carried out with a range of resin systems and glass fibres. It had been observed that heat-cleaned and loom-state glass fibres formed CAF more easily than finished fibres, and loom-state fibre had the highest propensity to form CAF compared with others. Phenolic-cured resin promoted more CAF than dicy-cured. The de-smear process increased CAF formation, but not as significantly as did the reflow process, and large glass bundle size gave a slight bu insignificant increase.
Subject of the next conference session, moderated by Oldrich Simek from PragoBoard in the Czech Republic, was PCB substrates and reliability. First to speak was EIPC Chairman Alun Morgan, this time in his role as Director of OEM Marketing for Isola Europe, and his topic was low-loss, high-thermal-reliability PCB materials.
Morgan began with an explanation of the causes of signal losses, where they occurred and how the laminate manufacturer could reduce them. There were two main types of signal loss: Conduction and dielectric, both of which effectively resulted in energy being wasted by the generation of heat. Conduction losses occurred in the copper and, as signal frequency increased, were increasingly associated with the surface of the copper because of a phenomenon known as the “skin effect,” which was the tendency of an alternating current to distribute itself within a conductor with its current density highest near the surface, causing the current to flow mainly at the "skin" of the conductor. The depth of the skin varied significantly with frequency - for copper it was 9.3mm at 50Hz, 6.6 microns at 100MHz and 0.66 microns at 10GHz. The skin effect effectively reduced the current carrying capacity of the conductor and increased its resistance at higher frequencies. The bonding treatment on standard copper foils left a rough surface with a depth of approximately 10 microns, which although it had little effect at low frequency caused serious losses at high frequencies, and low-profile (LP) or very-low-profile (VLP) foils were preferred for high-frequency applications.
Alternating signals caused polarisation and molecular vibration within the glass and resin components of the laminate, generating heat and consequent dielectric loss. Because the dielectric constants of glass and resin were different, the microimpedance effects of filament distribution in a glass-fabric reinforced laminate could cause problems with signal integrity at high frequencies. Delegates who visited the Isola Fabrics plant the previous day had seen at first hand how significant improvements had been made in the uniformity of glass distribution by manufacturing square-weave fabrics with spread fibres, to minimise this effect.
There were various terms for loss factor: dielectric loss, loss tangent, dissipation factor, loss angle and tan delta, all with the same meaning. Standard FR4 had a loss factor of 0.015 at 1GHz, compared with 0.002 for PTFE and 0.003 for certain ceramic-filled materials. Morgan referred to eye-diagrams to illustrate how it became progressively more difficult to discriminate between zero and one in a high-speed digital signal as loss factor increased. New-generation, non-PTFE, non-filled PCB substrate materials were becoming available which combined thermal reliability with loss factor around 0.003 at 1 GHz.
Whether intentionally or not, Morgan’s closing comments about recent launches along the market vector of Isola’s product-positioning map provided the perfect lead-in to the next presentation. With already an enormous variety of PCB base materials on the market, and new ones being frequently added, and well-marketed to OEM end-users, customers expected their PCB suppliers to be able to source fully characterised materials and move quickly in order to provide qualification samples. In many cases, the process recommendations given to PCB manufacturers were generic, insufficient or not practicable. Materials were often grouped into generalised classifications and the data sheet did not necessarily give a complete picture. From the perspective of a laminate user, Dr. Sylvia Ehrler, responsible for PCB base material qualification at Multek in Germany, commented upon PCB base material qualifications and the discrepancies between supplier recommendations, customer expectations and reality. It was Multek’s experience that new laminates were often released to the market too soon after development, before precise and resilient processing recommendations for key manufacturing steps like multilayer pressing, drilling and desmearing had been established.
Because OEMs often had early knowledge of new materials before they were in stable production, they expected fast material qualifications by their PCB suppliers, who in turn had to rely on data, test results and manufacturing recommendations provided by their material suppliers. It was not unknown for OEMs to specify materials in their designs that were not yet available to the PCB fabricator, even in sample form. This early marketing of materials caused avoidable effort and cost, and ran the risk of losing market share for new materials at a time when laminate suppliers should be beginning to recover their development costs through sales. Dr. Ehrler called for material suppliers to cooperate closely with PCB fabricators and supply detailed and precise documentation of all parameters tested, together with truthful test results, to receive comprehensive manufacturing recommendations before the commercialisation of a new base material.
Please don’t shoot the messenger! Emma Hudson from Underwriters Laboratories was not the bearer of good tidings when she gave an update on the implementation of UL746E, which required the reclassification of FR-4 materials. Despite UL having proposed that FR-4 epoxy laminates be classified in sub-groups based on chemistry and performance, which would have enabled the continuation of reduced test programmes, the Standards Technical Panel had failed to reach consensus in the vote of April 3, 2012 and ANSI now required the published requirements of UL796E to be implemented, with an effective date of June 30, 2014. The consequence was that any non-traditional FR-4 material that did not match published infra-red spectra and performance requirements would be treated as a non-ANSI grade and subject to full UL796E Section 9 testing. This would have an impact on laminate manufacturers and solder resist suppliers but by far the biggest effect would be on PCB manufacturers, who would be required to carry out a file update on all recognised PCBs using FR-4 material and full testing, including bond/delam and flame, of all non-ANSI grades and flame testing of all solder resists with each laminate combination. CCIL and MCIL programmes would not apply to non-ANSI materials. The only concession was that the enormous amount of work associated with the file update for PCBs would not begin until the file update process for laminates had been completed in June 2014.
Flammability and flame retardancy being the hot topics of the hour, it was appropriate that the following presentation should be on the subject of halogen-free flame retardants, and Dr. Oliver Töpfer from Nabaltec in Germany discussed the advantages of Boehmite when utilised as a halogen-free flame retardant filler in the cost-effective production of high-reliability base laminates. Boehmite was a form of aluminium-oxide-hydroxide, and was thermally stable up to 340ºC. By comparison, aluminium hydroxide decomposed at 200ºC to aluminium oxide and water, which had been shown to contribute to delamination and CAF effects, as well as losing its effectiveness as a flame retardant. Boehmite had a synergistic effect when used in combination with phosphorus-based flame retardants like DOPO, phosphaphene anthrene oxide, and could provide a significant increase in Tg whilst offering significant cost savings. Boehmite had been used in IC substrates and packaging since 2008 and was already used in cables, connectors and solder masks. Its first approvals in halogen-free FR-4 had been established in 2010 and its use was steadily increasing. Dr Töpfer established on a show of hands that the majority of members of the audience were carrying devices, particularly smart-phones, which contained boehmite as a primary flame retardant.
PCB007’s Pete Starkey stood-in for Giacomo Angeloni to moderate the session on processes and testing, in which the first speaker was Dr. Frank-Marc Krűger from Atotech in Germany. His work on ionic-liquid-based immersion gold processes paralleled that which had earlier been reported by Dr. Karl Ryder, but his focus was on non-cyanide formulations and his studies had centred around the use of sodium tetrachloroaurate Na[AuCL4] in a choline chloride-ethylene glycol deep eutectic solvent. Deep eutectic solvents based on choline were cheaper and less toxic than other ionic liquids, non-flammable and tolerant to water, but were viscous and had relatively low conductivity. Solutions of sodium tetrachloroaurate in choline chloride-ethylene glycol had been shown to be stable for five weeks at 50ºC, although if held for long periods at 90ºC the gold salt tended to decompose and precipitate metallic gold. When used to deposit immersion gold on electroless nickel, better results were obtained at lower temperatures: bright, uniform coatings were obtained at 20ºC at a plating rate of 40nm in 10 minutes with strong agitation. Porosity in the nickel layer resulted in discolouration because of copper dissolution. The chemistry was fragile but offered potential to be developed into an environmentally friendly drop-in process.
One of the practical problems associated with the deposition of very thin coatings in a production rather than research-laboratory situation was to measure accurately the thickness of the deposit. Werner Wittwer from Helmut Fischer in Switzerland described how X-ray fluorescence techniques, employing new X-ray tube and detector technologies, had been developed to meet the requirement. X-ray fluorescence analysis had its basis in the phenomenon that, when atoms in a material sample were excited by the primary X-radiation, electrons from the innermost shells were released; electrons from the outer shells then filled the resultant vacancies. During these transitions, fluorescent radiation was generated that was characteristic for each element. This was read by the detector and provided information on the composition of the sample. He explained that what was really being measured was the number of atoms, gold or palladium in the example of PCB finishes, then, knowing the atomic weights, the density of the bulk metals and the size of the measuring surface, the coating thickness could be computed from first principles without the need for calibration standards. Traditional proportional detectors tended to be of limited use on very thin coatings because the signals from gold and palladium were masked by background noise. The silicon drift detector gave more reliable results and the detector and x-ray tube could be optimised for high count rates even at low element concentrations. Fischer’s proprietary WinFTM software corrected for overlap in spectral lines and background scattering and their equipment was capable of statistically significant measurement of gold and palladium at thicknesses of a few nanometres.
Software was the subject of the next presentation as Claudio Bellistri from Orbotech in Belgium described the functionality of InSight PCB automatic pre-CAM for sales and engineering. InSight PCB was a web-based product-assessment tool for managing and assessing incoming customer PCB data for non CAM experts. “So simple, even a salesman can use it…”
Being web-based, the system could operate remotely so the sales engineer did not need to interrupt a CAM engineer to check incoming customer data in order to provide pricing and quotation information. He could work at home if necessary and generate precise summary reports, DFM reports, and Technical Query snapshots very quickly and efficiently, whilst identifying potential manufacturing problems at the earliest possible stage. The system could automatically run a pre-CAM flow as soon as new job data was submitted, and supported Gerber, ODB++, DXF, HPGL, DPF, Excellon, Sieb & Meyer and Hitachi data formats. The flow included input, buildup, cleanup, analysis and panel calculation and the system quickly produced graphic CAM-summary reports in PDF format. It would integrate with Frontline CAM, engineering and third-party quotation systems.
The final presentation of the conference came from Professor Martin Goosey, with an overview of progress on InBoard, a collaborative research project to develop an intelligent product and process monitoring system covering the whole electronic manufacturing supply chain, from printed circuit fabrication and assembly, through original equipment manufacturing, to end-of-life recycling, with easy access to information about the manufacturing history of a product to support traceability requirements and decision making at end-of-life, as well as providing scope for re-use and re-manufacturing. He explained that information could be stored in an electronic product by embedding radio frequency identification tags within the structure of the PCB, with the facility to read or write data wirelessly, and described how this had been successfully achieved. During the manufacture of a multilayer PCB, the RFIX chip was assembled on to an inner layer by a flip-chip process, and became fully encapsulated within the epoxy resin during the laminating process. The only significant modification to the PCB layout was the incorporation of an antenna in the periphery of the design. The embedded RFIX had been shown to withstand harsh environments and multiple thermal shocks. Product information could be stored from the very beginning of the manufacturing supply chain and during subsequent production processes for each individual product, and accessed with a hand-held reader even when the PCB assembly was enclosed within a piece of equipment.
Alun Morgan formally closed the conference, acknowledging the contributions of the speakers, the attention and participation of the audience, and thanked the EIPC team, particularly Sonja Derhaag and Kirsten Smit-Westenberg, for their cheerful and flawless organisation of such an excellent event.
More Columns from The European Angle
CircuitData: A New Open Standard for PCB Fab Data ExchangeI Never Realised It Was So Complicated!
The European Angle: Institute of Circuit Technology 43rd Annual Symposium
Ventec International Group's Martin Cotton Celebrates 50 Years in PCB Design
Reporting on the Institute of Circuit Technology Spring Seminar
EuroTech: Raw Materials Supply Chain—Critical Challenges Facing the PCB Industry
EuroTech: ENIPIG—Next Generation of PCB Surface Finish
EuroTech: Institute of Circuit Technology Northern Seminar 2016, Harrogate