-
- News
- Books
Featured Books
- smt007 Magazine
Latest Issues
Current IssueSpotlight on India
We invite you on a virtual tour of India’s thriving ecosystem, guided by the Global Electronics Association’s India office staff, who share their insights into the region’s growth and opportunities.
Supply Chain Strategies
A successful brand is built on strong customer relationships—anchored by a well-orchestrated supply chain at its core. This month, we look at how managing your supply chain directly influences customer perception.
What's Your Sweet Spot?
Are you in a niche that’s growing or shrinking? Is it time to reassess and refocus? We spotlight companies thriving by redefining or reinforcing their niche. What are their insights?
- Articles
- Columns
- Links
- Media kit
||| MENU - smt007 Magazine
Estimated reading time: 4 minutes
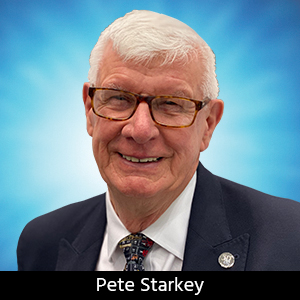
Contact Columnist Form
An Inside Look: IPC's PCBA Cleaning & Contamination Testing Webinar
The effective cleaning of PCB assemblies is an increasingly critical factor in determining the long-term reliability of electronic devices, particularly as design pitch becomes finer and component density increases. Cleaning is an issue that should be considered at the earliest stage of the design process if the highest reliability and functionality is to be achieved. In addition, lead free has placed higher stress on components and PCB materials, increasing the possibility of corrosion and failure.
IPC organised a free webinar January 10, 2013 focused on the practical process issues related to cleaning printed board assemblies and the failure modes that may be experienced during manufacture and in operation.
The webinar was introduced and moderated by Bob Willis who, amongst his many responsibilities, coordinates the NPL Process Defect Database and is managing the upcoming Cleaning & Contamination Testing Center Live programme at IPC APEX EXPO in San Diego, California. Willis concluded his introduction with the advice: “If you’re going to clean, clean properly.”
The main presentation came from Dr. Chris Hunt, leader of the Electronics Interconnection team at the National Physical Laboratory in UK, who explained that cleaning was performed to improve circuit reliability by removing flux residues and contamination. Any remaining residues on the surface could affect reliability by contributing to electrochemical corrosion, which could lead to failure through dendrite growth or conductive anodic filamentation, and he demonstrated how corrosion products in the form of metal ions could migrate, in the presence of moisture and electrical bias, from anode to cathode, across surfaces or along glass filaments.
Test methods attempted either to remove the residue or to measure the effect of its presence. The removal approach effectively cleaned the whole board and measured the conductivity of the solution due to ionic contamination. The alternative approach used resistance measurements at elevated humidity and temperature to detect the presence of ionic contamination.
Dr. Hunt explained the principles surface insulation resistance (SIR) testing, commenting that it was a direct measure of circuit reliability and the only method which attempted to link contamination and reliability. Any ionic contamination would lower the SIR and either degrade electrical performance or cause circuit failure. The SIR technique could be used to qualify both materials and production processes, and required some form of test pattern, properly representative of the design density of the circuit, either as a simple comb pattern on a separate coupon or incorporated into the PCB layout. The test pattern was exposed to an accelerating test environment of temperature and humidity under voltage bias to measure the leakage current between two metal electrodes on a substrate surface.
He showed examples of SIR results, the impact of test conditions on SIR for various fluxes, and the dramatic effects of dendrite formation on insulation resistance. He listed test standards and specifications, including the new ISO-9455-17: Solder flux characterization and IEC-61189-5: Production process characterization, and referred to the many reports and guidelines published by himself and his colleagues, available to download from the NPL library.
The alternative to SIR testing was extract conductivity testing, using alcohol-water mixtures as solvents to dissolve residues from the PCB assembly and measure the conductivity of the extract. Extract conductivity testing was popular as a process control procedure and was known alternatively as solvent extract conductivity (SEC) or resistivity of solvent extract (ROSE) testing. Ionograph and OmegaMeter are well-known proprietary test systems, which measure total ionic contamination as the equivalent of micrograms of sodium chloride per unit area.
Dr. Hunt showed results of different extraction methods, and commented that although SEC and ROSE tests gave an indication of the extent of ionic contamination they did not identify the actual contaminants. However, ion chromatography could be used as a technique to distinguish and quantify individual anionic species in the solvent extract.
Having referred at length to surface contamination issues, Dr. Hunt turned his attention to effects within the PCB itself, particularly the phenomenon of conductive anodic filamentation (CAF), an electromigration effect originating in the PCB manufacturing process that resulted in the growth of conductive material along the interface between laminating resin and glass reinforcement fibres, and could result in internal short circuits between plated-through-holes. He discussed the factors that could contribute to CAF and described a simulation vehicle developed by his team at NPL, which enabled the study of CAF on a single glass filament under controlled experimental conditions and had contributed greatly to the understanding of CAF mechanisms.
Bob Willis put a practical dimension on the proceedings by reminding assembly engineers what they could achieve in their own facilities, and showing many examples of actual contamination-related failure from the NPL Process Defect Database. Not all failures were necessarily corrosion-related in the first instance and an example he quoted was of silicone contamination causing adhesion failure of conformal coating, preventing it from providing long-term environmental protection.
Willis wrapped-up the webinar by recapping what would be offered in San Diego--hands-on workshops and free seminars on each exhibition day, including:
- Cleaning and Contamination Failures – Causes and Cures;
- Cleaning Under Low Stand Off Components;
- Testing Printed Board Assemblies For Cleanliness;
- How to use Ion Chromatography for Cleanliness Testing;
- Evaluating a Cleaning Process Performance;
- Reliability of Flux Residues Under Low Stand Off Devices;
- Cleaning Package On Package Assemblies;
- Conductive Anodic Filament CAF Failures and Defect Analysis;
- Testing Adhesion of Conformal Coatings and Failures; and
- Testing Components for Cleaning Process Compatibility.
The amount of relevant information, both theoretical and practical, delivered in this webinar was substantial and of the highest calibre, with both presenters drawing upon their enormous experience and generously sharing their knowledge. IPC is to be congratulated on a very successful event, both in its own right and as a prologue to the upcoming Cleaning & Contamination Testing Center Live hands-on workshop series at IPC APEX EXPO.For a better idea of what to expect in San Diego, click here.
More Columns from The European Angle
CircuitData: A New Open Standard for PCB Fab Data ExchangeI Never Realised It Was So Complicated!
The European Angle: Institute of Circuit Technology 43rd Annual Symposium
Ventec International Group's Martin Cotton Celebrates 50 Years in PCB Design
Reporting on the Institute of Circuit Technology Spring Seminar
EuroTech: Raw Materials Supply Chain—Critical Challenges Facing the PCB Industry
EuroTech: ENIPIG—Next Generation of PCB Surface Finish
EuroTech: Institute of Circuit Technology Northern Seminar 2016, Harrogate