Estimated reading time: 3 minutes
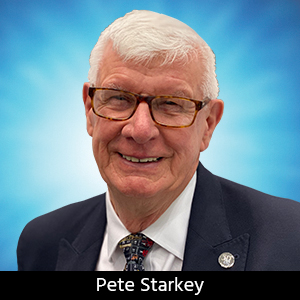
Contact Columnist Form
Behind the News: Tripod Selects Semblant's Plasma Finish
Semblant recently announced that global leading printed circuit fabricator Tripod Technology Corporation selected the Semblant Plasma Finish (SPF) and ProVIA system to meet customer demands for high-volume PCB surface finish advancements.
As a PCB technologist with a long-term interest in the evolution of solderable finishes for circuit boards, I have taken every opportunity to follow the progress of Semblant in the market since becoming aware more than two years ago of their plasma-based surface treatment process and recognising its potential to bring about a step change in the industry. I have reviewed presentations at many conferences and seminars, and spoken at length with senior Semblant people.
From personal experience, I know what an arduous task it can be to get a new finish recognized, qualified, and specified. I was favourably impressed to read Semblant’s announcement and delighted to then have the opportunity to seek the comments of Vice President of Worldwide Sales and Marketing Steve McClure.
Pete Starkey: Steve, it’s good to talk to you again. Congratulations! This is a significant step forward.
Steve McClure: Yes, Pete, we’re very excited about it. It’s a pretty major win for us and marks the culmination of a series of in-depth evaluation and qualification programmes with several OEM customers of Tripod and other leading PCB fabricators. These OEMs recognise the benefits of SPF.
Starkey: From the OEM perspective, what has been the initial driving force? Have they set out to overcome a specific problem?
McClure: Obviously there are many areas where the advantages of SPF can be realised, but one specific problem relates to immersion silver. OEMs and their assemblers like the performance and properties of silver, but creep corrosion has always been an issue. We have conclusively demonstrated that creep corrosion can be eliminated using SPF.
Starkey: So, in this particular application, SPF is being used to enhance the properties of an established finish rather than replace it?
McClure: In this instance, yes. SPF over silver gives OEMs substantial improvements in long-term reliability and resistance to environmental pollutants, but that’s not the only advantage: There are benefits in the assembly process itself, in addition to extended shelf life of bare boards. SPF is a hydrophobic finish and consequently has the ability to restrict the flow of flux and contain it within the local area of the solder pad. Customers are looking to use SPF for significant yield improvement on HDI designs by eliminating solder shorts.
Starkey: What’s the logical next step?
McClure: Tripod’s first priority is to eliminate corrosion of silver. Their next objective will be to eliminate the silver itself with SPF on copper.
Starkey: That suggests the use of SPF as a self-finish?
McClure: Yes, SPF on copper maximizes PCB cost-performance and the process is naturally suited to high-volume production. There is a lot of interest in this area and we have several programs in place, with multi-party dialogue between OEMs, EMS providers, and PCB fabricators. Successful evaluation and qualification require close cooperation right along the supply chain. The OEM ultimately controls the specification, and the EMS and the PCB fabricator are specialist service providers whose input is fundamentally important. As one of our premier partners, Tripod can facilitate quick-turn evaluation, prototyping and production for OEMs approval.
Starkey: Looking further forward, what do you see happening in the military and aerospace sectors?
McClure: This segment has a different set of requirements and are mostly ENIG users. On one hand they see SPF as a means of additional environmental protection, by applying it over the ENIG finish; on the other hand, they see SPF as a finish in its own right which will give improvements in signal integrity at high frequencies by eliminating the effects of electroless nickel, whilst maintaining environmental durability. Several projects are in planning right now. There’s a lot going on to keep us busy!
Starkey: Steve, I am grateful to you for once again sharing your opinions and experiences with us. I wish Semblant continued success.
More Columns from The European Angle
CircuitData: A New Open Standard for PCB Fab Data ExchangeI Never Realised It Was So Complicated!
The European Angle: Institute of Circuit Technology 43rd Annual Symposium
Ventec International Group's Martin Cotton Celebrates 50 Years in PCB Design
Reporting on the Institute of Circuit Technology Spring Seminar
EuroTech: Raw Materials Supply Chain—Critical Challenges Facing the PCB Industry
EuroTech: ENIPIG—Next Generation of PCB Surface Finish
EuroTech: Institute of Circuit Technology Northern Seminar 2016, Harrogate