Estimated reading time: 15 minutes
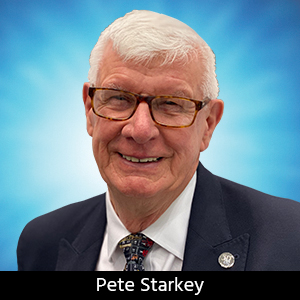
Contact Columnist Form
IeMRC 8th Annual Conference: Innovation and Sustainability
The early morning mist gave way to a clear, bright autumn day as delegates gathered in the Sir Dennis Rooke Building for the 8th annual conference of the Innovative Electronics Manufacturing Research Centre (IeMRC) at Loughborough University in the UK.
Research Coordinator Dr. Darren Cadman introduced an intensive programme of eleven presentations, grouped into four sessions: Accelerating Innovation, Flexible Electronics, Sustainability, and Nanoelectronics.
The opening presentation came from Dr. Huw Davies, lead technologist with the Technology Strategy Board (TSB), the UK's innovation agency whose goal is to accelerate economic growth by stimulating and supporting business-led innovation and offering funding to help businesses develop new products and services and to bring them closer to market.
He gave an overview of his specialist area of electronics, sensors, and photonics, considered by the TSB to be key enabling technologies, and referred to the recently published ESCO report, Electronics Systems: Challenges and Opportunities, a strategy document created for the Department of Business, Innovation, and Skills, which detailed how the electronic systems industry could expand by 55% between now and 2020 to contribute £120 billion to the UK economy and create an additional 150,000 highly-skilled jobs.
One of the main challenges for the UK electronics sector was the prohibitive cost of product development and manufacturing, especially for early-stage companies, and Dr. Davies used Paul Graham’s “Start-up Curve” to illustrate the process of taking a concept to commercial realisation. Phases labelled “Trough of Sorrow,” “Crash of Ineptitude,” and “Wiggles of False Hope” constituted the “Valley of Death” which the TSB aimed to help companies to cross with a whole range of business support and funding tools, designed to meet specific needs of companies, sectors, and technologies.
The Valley of Death was central to the following presentation. In his enormously energetic and entertaining style, Andy West, Professor of Intelligent Systems at Loughborough, told a story about getting into it and floundering around trying to get out of it. His topic was embedded product and process monitoring across the electronics supply chain, and the big question was “Can we get it right first time?” in the context of the migration of UK electronics towards supplying low-volume high-complex manufacturing solutions to a global market.
With his first example, he demonstrated how a combination of RFID and various sensors had been used to help improve the performance of Olympic swimmers by monitoring, measuring, and recording the physical parameters of the process of swimming, then analysing the results to determine how the process could be performed more efficiently. The principle of getting information from sensors to gather data on how a product performed had enormous scope, and could enable designs to be optimised to ensure that a product performed effectively in the environment it was required to work in. Standing in front of a complex Ishikawa cause-effect analysis diagram, he discussed how knowledge could be identified, derived and extracted from all the possible causes, then, using experimental models, simulation models and physical models, built into software to predict where problems might be encountered.
But how to find help and funding for the research? Professor West showed a long list of completed and current TSB and EPSRC projects in which his team had been involved, and briefly described two embedded RFID projects, one related to bare-board testing of PCBs, linking the RFID with the test results and one being conducted in partnership with MTC in Coventry where the system was being incorporated into a complete SMT assembly line. There was massive interest from the automotive industry who saw the principle as a route to better traceability, more robustness, and right-first-time performance.
Once more into the Valley of Death, not Tennyson’s Light Brigade, but Dr. Martin Walkinshaw from the Centre for Process Innovation as he opened the session on flexible electronics. CPI is an independent public/private partnership, whose Printable Electronics Centre focuses on design, development and prototyping for the emerging printable electronics industry. CPI’s mission is to work with clients to bring new printable electronics products and processes to market quickly and efficiently, by offering facilities and expertise that help reduce the level of R&D risk and capital investment, while speeding up time to market--assisting them to cross the same Valley of Death that previous presenters had confronted: the innovation challenges in the mid technology-readiness-level and manufacturing-readiness-level development stages. "Research is the transformation of money into knowledge. Innovation is the transformation of knowledge into money."
Dr. Walkinshaw listed current innovation challenges in printable electronics: Scale up to large area, roll-to-roll processing, uniformity, integration with conventional electronics, barrier and encapsulation, and cost of manufacturing. A key technology area was the atomic layer deposition of ultra-barriers for flexible electronics applications, which was an enabler for organic thin film transistors for flexible displays, solid state lighting and photovoltaics, and integrated smart systems and sensors. He gave updates on the LACE project: Large-area coating for organic LEDs including developments in large-area single pixel solid-state lighting, organic photovoltaic technology for architectural glass, integrated smart systems developments, including ink formulation and characterisation, printed connections for novel lighting application, printed antenna for flexible circuits and printed electronics in toys and games. Other projects in which CPI were partners were Intellico: Intelligent embedded components for enhanced supply chain observability and traceability, and Diginova: innovation for digital fabrication. He reviewed activities in the development of high-mobility organic semiconductors for displays, and challenges in roll-to-roll coating of these materials by ink-jet and slot-die techniques.
Roll-to-roll processing was the subject of the following presentation, by Dr. Hazel Assander from University of Oxford, but in this case the operation was carried out under vacuum. Dr. Assander reported latest developments in the IeMRC flagship project aimed at demonstrating the ability to fabricate all-evaporated transistors in a roll-to-roll web process environment, exploiting technology that is used in the packaging industry. Main issues were to establish process parameters for building and testing transistors, to design circuits tailored for the properties achievable by this manufacturing route, to develop suitable organic semiconductor and polymer gate insulator materials, and patterning processes to yield robust final devices. Good progress had been made in integrating the process stages, and in the optimisation of techniques for high-resolution pattern metallisation, gate insulator deposition, patterning of organic insulator and semiconductor layers, and modification of the insulator surface. Dinaphthothienothiophene (DNTT) had been evaluated as an alternative to pentacene and had given improvements in environmental stability. Yield improvements and the reproducibility of transistor properties had provided the confidence to start building actual circuits; inverters, NAND and NOR gates and ring oscillators, which had been characterised and environmentally and mechanically tested.
From film-based flexible electronics to fabric-based antennae for wearable applications, Dr. Rob Seagar from Loughborough University and Professor Tilak Dias from Nottingham Trent University took turns to describe their work on high performance flexible fabric electronics for megahertz frequency communications and the results they had achieved.
Tests had been conducted with full fabric patches and dipoles made of copper wire or a proprietary metallised textile fibre and their high-frequency characteristics measured. Their performance made these antennae commercially viable, although some variability still needed to be addressed. Work was currently focused on digital embroidery techniques, the selection of suitable electro-conductive yarns, the optimisation of machine conditions to create fabric antennae, and the investigation of fabric based interconnection systems. The mechanical and electrical properties of wide range of different yarns had been studied, and their compatibility with embroidering machines determined. Overcoming friction had been one of the biggest challenges, but lubrication and modification of the yarn-guiding system had yielded some improvements. Parameters such as stitch direction and stitch density had significant effects on the durability of the fabric antennae during abrasion testing. Washing trials had shown little effect on durability. Meshed patch antennae were being investigated as a means of reducing material cost and reducing stiffness, and funding was currently being sought for continuation work.
The third session was on the theme of sustainability. Professor Margaret Bates from the University of Northampton took time out of her international travel schedule, pausing en-route from India to Kenya to describe to the conference her work to improve the recycling of electronic waste in Africa.
She commented that E-waste, of which the UK currently produces 1 million tonnes per annum, is increasing three times faster than other waste streams. World-wide, 41.5 million tonnes had been generated in 2011 and this was forecast to increase to 93.5 million tonnes in 2016. What started off as a re-use strategy to give developing regions the benefit of low-cost information technology by shipping functional or easily repairable computers as a means of fosterig sustainable development had now got out of proportion and it was estimated that by 2016-2018, the volume of obsolete PCs generated in developing regions would exceed that of developed regions and that by 2030 the developing countries would be discarding 400 to 700 million obsolete PCs per year compared to 200 to 300 million in developed countries.
Although the Basel Convention prohibited the shipping of hazardous waste to developing countries, Nigeria was a key destination for E-waste from UK, largely because Nigerians came to the UK to buy it, and there were links with organised crime. There was a huge trade in second-hand PCs because people could not afford to buy new, but a large proportion of the material currently imported was beyond repair and unless there was an effective end-of-life recycling solution would end up in landfill or on illegal open dumps.
Professor Bates had worked for several years with government and industry to provide education and training and to establish proper E-waste recycling facilities in Nigeria, Ghana, and Tanzania to reduce their reliance on landfill for disposal. Presently she was working with the Kenyan National Environment Management Authority to build the E-waste recycling capacity in that country.
Sustainability from a different angle--Dr. Andrew Ballantyne reported work in progress at University of Leicester to develop greener, cleaner, cheaper sustainable soldering fluxes from novel ionic liquid solvents. Ionic liquids were purely ionic materials with melting points below 100°C, which exhibited unusual solvent properties, low vapour pressure, and good thermal stability. Deep eutectic solvents were a class of ionic liquid composed of organic cations with halide anions and various complexing agents to make an anionic complexes, characterised by low cost, ease of manufacture, low sensitivity to water, and high metal solubility, which had proven applications in metal finishing, plating, electropolishing, and metals recovery.
The purpose of a soldering flux was to clean metal surfaces, prevent them from oxidising during the soldering process and maximise wetting interaction between substrate and solder. But conventional fluxes tended to be toxic and corrosive, and there were supply chain issues with certain ingredients. By comparison, deep eutectic solvents were inexpensive, exhibited high solubility of metal oxides, together with low toxicity and environmental impact. Qualitative tests had indicated that they could be used as flux for soldering a variety of metals including copper, brass, cast iron, and stainless steel.
IeMRC was supporting a project to assess the use of deep eutectic solvents as flux media for electronics assembly, to understand the surface chemistry, the influence of formulation and the analysis of degradation products. Studies of solder spread and interfacial properties on copper and electroless nickel immersion gold surfaces were showing encouraging results, which were in the process of being quantified by wetting balance measurements.
Daniel Rogers, a Ph.D. student from the University of Sheffield returned to the topic of recycling and sustainable end-of-life re-manufacture of electronics with a presentation on adapting ATX computer power supply units (PSUs) for use as maximum-power-point-tracking (MPPT) solar interfaces for battery charging. His point of reference was 2007, when EU countries disposed of 6.5 million tonnes of Waste Electrical and Electronic Equipment (WEEE). Traditionally WEEE processing has been focused on extraction of raw materials, and processing centres in Germany were achieving recovery rates ranging from 29% to 61% from ICT equipment. As an alternative to raw materials extraction, the Environmental Association for Universities and Colleges advocated the reuse of computer equipment in the developing countries in Africa.
Rogers was engaged in a project to investigate the practical steps in recovering PSUs, to develop a generic MPPT converter tolerant to variable component choices and specifications, to present a business case for dismantling, recovery and reuse of components, and to evaluate the socio-economic viability of PSU reuse through interaction with ICT recyclers and photovoltaic providers. A partner in the project, Aspire-Sheffield provided employment and a supported working environment for vulnerable or marginalised people, and used the recycling of WEEE as a revenue and employment stream. Their staff had been trained to identify active power-factor-correction (PFC) PSUs.
The suggested end application was to provide a low-cost means of charging mobile phone batteries in in the poorest parts of the world using solar panels as the power source. The technical aim of the power converter was to maintain the solar panel at its maximum power point. ATX PSUs had been modified with a new controller feeding the boost and half bridge stages. With surplus output cables removed and new driver inputs, the PSUs now operated from a DC input at 12-25V. “Perturb and Observe” (P&O) methodology had been chosen as a preferred means of maintaining the maximum power point and solar simulator trials had indicated very high levels of conversion efficiency, confirming the feasibility of the system as an affordable photovoltaic converter.
“Where Nature Meets Electronics” was the tag-line of the presentation by Professor Marc Desmulliez from Heriot-Watt University, which described a process for metallisation of non-conductive surfaces using chlorophyll. Of the various routes available for achieving additive pattern metallisation, Heriot-Watt had an established history in light-directed additive metallisation for contact-less, high-resolution patterning. Their process began by treating a polyimide substrate with potassium hydroxide to impregnate the surface with potassium ions, then immersion in a silver solution to ion-exchange potassium for silver before coating with a thin layer of a photo-activated reducing agent which would donate electrons to regions of the substrate selectively exposed to light and generate silver metal nanoparticles only on those sites. The substrate surface became a nanocomposite layer, with the metal nanoparticles mechanically interlocked within the modified polymer matrix, and 40-micron line-and-space resolution had been achieved.
The photo-activated reducing agent originally used was a methoxy polyethylene glycol, which had the limitation of being very slow to expose, and an undesirable side effect of the long exposure was UV degradation of the substrate. A more efficient alternative had been sought, and Professor Desmulliez’ team looked to nature for a solution. The perceived potential advantages were that the process would be faster--nature is good at optimising process efficiency--and environmentally friendly. Spinach proved to be a good source of natural photoactive reducing agents, although the physics and chemistry of photosynthesis was extremely complex. The natural photosystems contained many light-absorbing proteins, including chlorophylls and carotenes. Using an extract of pulped spinach as the photo-activated agent in the imaging process reduced the exposure time from hours to seconds and gave remarkable uniformity of distribution of silver particles through the thickness of the surface layer, the mechanism of which had not yet been explained.
The theme of the fourth conference session was nanotechnology, and it began with a presentation from Dr. Davis Hutt of Loughborough University on the functionalisation of copper nanoparticles to enable metallisation in electronics manufacturing, a joint IeMRC project between Loughborough and Coventry Universities.
Electroless copper was widely used in printed circuit manufacture for the metallisation of via holes, and most proprietary processes depended upon a colloidal tin-palladium initiator, which was expensive and gave limited adhesion on some substrates, particularly glass. An alternative was proposed based upon commercially available copper nanoparticle powders. In order to aid dispersion, improve adhesion to surfaces and reduce the rate of oxidation, it was necessary to functionalise these particles. The suggested route was to coat them with a self-assembled organic monolayer approximately 2 to 3 nanometres thick, the typical diameter of the nanoparticles being about 25 nanometres. Ultrasound had been used to achieve good particle dispersion and the functional coating had improved both the stability of the dispersion, as measured by dynamic light scattering, and the adhesion of the nanoparticles and subsequently deposited electroless copper on FR4 laminate surfaces. Other substrates were presently being studied.
The final presentation of the day came from Michael Down, a Ph.D. student at Southampton University, discussing a means of dramatically improving the lifetime and endurance of MEMS microswitches by applying vertically aligned multi walled carbon nanotubes as a compliant subsurface to electrical contact interfaces, and to investigate the effects of this subsurface on the electrical and physical performance of low force, low-current MEMS microswitches.
Carbon nanotubes were grown on silicon chips sputter-coated with an aluminium oxide seed layer and an iron catalyst in a chemical vapour deposition furnace using ethylene as the carbon source. They were then sputter-coated with gold, creating rough, but compliant and conductive, surfaces. Samples were tested by mounting them on a piezoelectric cantilever, and contacting them with a gold coated hemisphere at actuating frequencies up to 150hz, with an electrical load of 4V, an electrical current of 0 to 200mA and a contact force of 1mN.
Wear mechanisms and cycles-to-failure were observed, and lifetimes were found to be several orders of magnitude longer than those of solid-solid contacts under the same conditions. A counter intuitive effect was that the number on bounces upon closing the switch increased with the presence of the compliant subsurface. And material transfer, which in regular devices was largely determined by the polarity of the contacts, transferred from the flat substrate to the ball regardless of the polarity and was rate dependent on current and frequency.
IeMRC Academic Director Professor Paul Conway made the closing remarks, summarised ongoing IeMRC activities, and announced that a final call for proposals would be made shortly.
The 8th annual conference of the IeMRC was once again a technically intense, but highly informative opportunity for delegates to learn about innovative and exploitable new technologies, and to network with their peers in industry and academia. And a great credit to the IeMRC team for their smooth and efficient administration and organisation.
Columnist's Note: I am grateful to Vin Scothern for kindly allowing me to use his photographs.
More Columns from The European Angle
CircuitData: A New Open Standard for PCB Fab Data ExchangeI Never Realised It Was So Complicated!
The European Angle: Institute of Circuit Technology 43rd Annual Symposium
Ventec International Group's Martin Cotton Celebrates 50 Years in PCB Design
Reporting on the Institute of Circuit Technology Spring Seminar
EuroTech: Raw Materials Supply Chain—Critical Challenges Facing the PCB Industry
EuroTech: ENIPIG—Next Generation of PCB Surface Finish
EuroTech: Institute of Circuit Technology Northern Seminar 2016, Harrogate