-
- News
- Books
Featured Books
- design007 Magazine
Latest Issues
Current IssueProper Floor Planning
Floor planning decisions can make or break performance, manufacturability, and timelines. This month’s contributors weigh in with their best practices for proper floor planning and specific strategies to get it right.
Showing Some Constraint
A strong design constraint strategy carefully balances a wide range of electrical and manufacturing trade-offs. This month, we explore the key requirements, common challenges, and best practices behind building an effective constraint strategy.
All About That Route
Most designers favor manual routing, but today's interactive autorouters may be changing designers' minds by allowing users more direct control. In this issue, our expert contributors discuss a variety of manual and autorouting strategies.
- Articles
- Columns
- Links
- Media kit
||| MENU - design007 Magazine
Estimated reading time: 1 minute
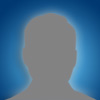
Contact Columnist Form
Design for Manufacturing: Mythbusting - Semi-additive Process Makes Sub-3/3 a Reality
Prudent PCB designers used to have good reasons for avoiding trace widths and spaces smaller than 3 mils beyond very short spans. But the 3-mil limitation is now becoming a thing of the past, thanks to the use of semi-additive fabrication by some board manufacturers. The main reason designers steered clear of sub-3-mil lines and spaces for more than short distances is etch factor.
The convergence of ever-greater circuit density and ever-higher data rates has reached the point where the chemistry of conventional PCB fabrication processes cannot be controlled tightly enough to consistently satisfy design needs. The traditional manufacture of PCBs begins with a laminate clad with copper on one or both sides. PCB manufacturers purchase clad laminates (cores) from suppliers in a wide range of substrate materials and copper thicknesses, and they also create laminates by bonding substrate materials in prepreg form with copper foils in a press.
Basically, traces are patterned by applying an etch resist to the copper surface, curing the resist by selectively exposing it to light where copper should be retained as traces and other features, and then etching away (subtracting) the unexposed resist and underlying copper in an acid bath. The objective is to produce traces whose cross-section is rectangular. However, the bath not only removes copper in the vertical direction but also eats some of it away at the sides of the traces horizontally underneath the resist, resulting in the sort of profile illustrated in Figure 1.
Figure 1: The etch factor (F) is the ratio of the trace height divided by how far the trace was eaten away at the top on one edge compared to the base. F = t/x.
Editor's Note: This column originally appeared in the April 2014 issue of The PCB Design Magazine.
Amit Bahl directs sales and marketing at Sierra Circuits, a PCB manufacturer in Sunnyvale, CA.
More Columns from Various Archived Columns
Slash Sheet Chaos: Is What You See, What You Get?Moisture in Materials: Avoiding Process Gremlins
Material Witness: Beat the Heat--A Non-Math Intro to Thermal Properties
Material Witness: Considerations in Using TC Materials for PWBs
Material Witness: Are Your Materials Up to the Challenge?
Material Witness: Thermal Oxidation of Materials, Part I
Material Witness: Thermal Oxidation of Materials, Part II
Material Witness: R.I.P. Speedboard C