Estimated reading time: 7 minutes
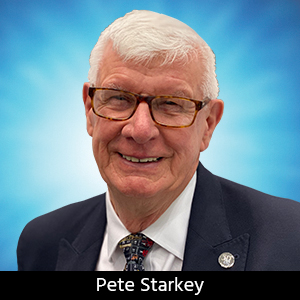
Contact Columnist Form
ECWC 2014 Market Session: Connecting the World
On the first day of the 13th Electronic Circuits World Convention (ECWC), delegates crowded into the Kiew Room of the Nuremberg Messe to hear four of the world’s leading experts on PCB markets and market trends make their analysis of what the future held for the industry. Introduced and moderated by IPC’s Marc Carter, the session included presentations from Dr. Hayao Nakahara, Walt Custer, Michael Weinhold, and Bill Burr.
“Cost, cost, cost--unless you can meet the cost, you can’t continue your business!” These were Dr. Nakahara’s opening words as he examined the business situation in China and discussed the alternative market areas attracting investment. In 2012, China’s share of world PCB production was 44%, and it had seemed destined to continue its domination into the long term. However, rising wages, labour shortages, high personnel turnover, and tougher environmental regulations were making it increasingly difficult to operate, particularly in the coastal regions.
Japanese PCB makers had stopped investing in China and were expanding operations in South East Asia, particularly in Thailand and Vietnam, as were some Taiwanese and South Korean manufacturers. Thailand was the largest PCB producing area in South East Asia, with output already exceeding that of Germany, followed by Vietnam, Malaysia, the Philippines, Singapore, and Indonesia. No substantial Japanese investments were being made in the Philippines and Indonesia, and costs were so high in Singapore that new investment was out of the question.
Why not India or Brazil? Although there had been much speculation over the years, there were no signs of expansion. Government regulations and lack of infrastructure made it difficult to make large investments in India, and although the importation of PCBs continued to increase, domestic production was relatively static. Brazil lacked infrastructure and had the additional burden of a complex taxation system. Output had fallen substantially since Multek had closed down its Brazilian operation.
By comparison, South East Asia had reasonable infrastructure, although nowhere near as highly developed as China, and there were laminate factories in Thailand, Singapore and Malaysia, which also had the world’s largest foil plant.
Dr. Nakahara forecast that South East Asia’s share of the world PCB market would rise from 6.8% in 2013 to 8.2% in 2017, and be worth over $5 billion.
At major conventions, it is customary to expect Walt Custer to give an up-to-the-minute global business outlook for the electronics industry. At ECWC13, he took a slightly different approach and gave delegates an opportunity to learn how apply supply chain data to make meaningful forecasts for individual businesses, in a presentation elegantly entitled “Global Electronic Industry Supply Chain Dynamics: Forecasting Equipment and Component Demand caused by Business Cycles, Product and Technology Changes, and Geographical Shifts.”
He summarised the principal factors determining business cycles: Economic fluctuations, cataclysmic events, new product cycles, inventory build-ups and declines, double ordering in anticipation of shortages, poor management practices, geographic shifts and abrupt technology changes, then listed the global and regional data sources and leading indicators used to monitor and measure growth within the electronics food chain.
Useful data could be acquired from trade organisations, government statistics, published market research studies, company financial reports, and consolidated sector statistics. Purchasing managers’ indices were a valuable group of leading indicators.
With appropriate reference data gathered and in place, Custer demonstrated how it was possible to forecast an individual company’s sales by organising its monthly or quarterly sales figures on a spreadsheet and comparing them with related industry time series for the same period using 3/12 growth rates, then determining lead times against company data, forecasting company sales based on lead times and estimating the company’s gains or losses in market share by comparing company growth to a related industry sector. The methodology had been proved to work, and to give companies good warning of what to expect. He made it look easy!
Michael Weinhold posed the question, “What business are we in?” Whether the nominal response was the making of PCB’s, or electronic components, or electronic devices, or cars, the real answer was “We are in the business of making money!”
The electronics industry offered the potential to make money through innovative new electronic products focused on large volume production, using competence and existing know-how, investing money and resources in future technologies and target markets with growth opportunities. And Weinhold saw component embedding in PCBs as a significant future niche-market opportunity, with particular significance in Europe where the number of PCB fabricators had dwindled from 2,500 in the 1960s and 1970s to barely 250 now, and innovation and differentiation were vital survival strategies in a market otherwise held to ransom by buyers and purchasing agents.
Device embedding technology had a long history in Europe in the ceramic hybrid sector, and had been employed in PCBs since the late 1990s. The technology had the benefits of fast design and fabrication. High-reliability product development was possible and standard components could be embedded in small and medium quantities. The alternative was to design on silicon, which could offer substantial cost and size reduction, but involved high set-up expenses and long design cycles and was only appropriate for large-scale production.
Weinhold showed examples of various techniques, proprietary and non-proprietary, for component embedding, inspection and test, and made value-in-use comparisons to illustrate costs and break-even points. It was clear that embedded technology had the potential to improve quality, miniaturisation, energy efficiency, and thermal management, but also clear that PCB fabricators would have to learn how to absorb and master the challenges of fabrication, assembly, device testing, and end-use application. And it had to be understood that the market opportunity was determined by quantity. Once quantities were sufficiently large to make it economically viable for silicon and chip packaging industries to take an interest, they would sooner or later find a solution. The silicon solution would be selected and implemented, and that particular product would be lost to the PCB industry.
To properly realise the opportunity presented by embedded component technology, it was important that the PCB industry should encourage electronic designers to recognise it as a fast and cost-effective route to market. This would stimulate demand for small-to-medium batch quantities and offer a good return for PCB fabricators.
Bill Burr delivered that final paper of the session, with some thought-provoking observations and alternative views on the growth of the solid state lighting market and its impact on the PCB industry: “Is it really time for overdrive? The LED dilemma.” He foresaw a fundamental paradigm shift driven by the technical and market parameters of solid state lighting and a Moore’s Law counterpart known as Haitz’s Law, which stated that every decade, the cost per lumen would fall by a factor of 10, and the amount of light generated per LED package would increase by a factor of 20.
“The times they are a-changing!” There had been artificial lighting since man first discovered fire, and of recent times the lighting business had been dominated by a few big-name manufacturers whose business model was to churn out billions of replacement light bulbs. Then came LEDs, characterised by low power consumption, low operating voltage and small form factor. And they had a much longer life expectancy than conventional bulbs, typically 50,000 hours compared with 1,000 hours. There were an estimated 14 billion light-bulb sockets in the world. Each time a conventional bulb was replaced by a solid state device, it effectively took one socket off the market.
Burr talked about “The Bothersome Bump”--the initial filling-up of light-bulb sockets was forecast to consume 2 billion bulbs worth of capacity per year. But after an initial build-up, peaking at about six years, there would be an enormous capacity hangover. Perhaps a smaller secondary peak would be seen at nine years, and another, even smaller, at 12 years corresponding to replacement cycles, but steady state demand volume would show only a gradual linear increase in line with ongoing growth of the total number of sockets. That was where Haitz’s Law diverged from Moore’s Law. There was a limit to how much light the world needed, so whereas the demand for computing power was near infinite, lighting requirements were finite, and as LED efficiencies improved, the actual number of luminaires required to achieve a given lighting level was decreasing significantly.
What would be the consequence on the PCB industry? Rapidly growing markets would drive substrate volumes. Increasing power density--more output per LED and more LEDs per unit area--would demand greater thermal conductivity and create a substantial and growing demand for metal-in-board substrates. Developments in the technology of LEDs themselves, for example the alternatives for producing a pure white light by the use of coloured phosphors on basic blue-white LEDs, or white and multi-colours by combination of monochromatic red, green and blue LEDs, powered and switched separately and requiring more complex metal-in-board interconnects.
The initial market surge was expected to subside in the middle of the decade, although it was anticipated that the shortfall would be filled by new applications as new capabilities of solid state lighting were realised. All of these developments would require enhanced thermal and power management capability from the interconnect and the printed circuit industry would respond with an expanding range of solutions going beyond established metal-base and metal-core technologies to provide cost-effective solutions to the challenges of thermal and power management, enabling new applications, and market opportunities.
More Columns from The European Angle
CircuitData: A New Open Standard for PCB Fab Data ExchangeI Never Realised It Was So Complicated!
The European Angle: Institute of Circuit Technology 43rd Annual Symposium
Ventec International Group's Martin Cotton Celebrates 50 Years in PCB Design
Reporting on the Institute of Circuit Technology Spring Seminar
EuroTech: Raw Materials Supply Chain—Critical Challenges Facing the PCB Industry
EuroTech: ENIPIG—Next Generation of PCB Surface Finish
EuroTech: Institute of Circuit Technology Northern Seminar 2016, Harrogate