-
- News
- Books
Featured Books
- design007 Magazine
Latest Issues
Current IssuePartial HDI
Our expert contributors provide a complete, detailed view of partial HDI this month. Most experienced PCB designers can start using this approach right away, but you need to know these tips, tricks and techniques first.
Silicon to Systems: From Soup to Nuts
This month, we asked our expert contributors to weigh in on silicon to systems—what it means to PCB designers and design engineers, EDA companies, and the rest of the PCB supply chain... from soup to nuts.
Cost Drivers
In this month’s issue of Design007 Magazine, our expert contributors explain the impact of cost drivers on PCB designs and the need to consider a design budget. They discuss the myriad design cycle cost adders—hidden and not so hidden—and ways to add value.
- Articles
- Columns
Search Console
- Links
- Media kit
||| MENU - design007 Magazine
Estimated reading time: 7 minutes
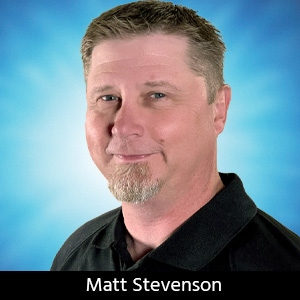
Connect the Dots: Designing for Reality—Pattern Plating
In the previous episode of I-Connect007’s On the Line with… podcast, we painted the picture of the outer layer imaging process. Now we are ready for pattern plating, where fabrication can get tricky. The board is now ready to receive the copper traces, pads, and other elements specified in the original CAD design. This article will lay out the pattern plating process and discuss constraints in the chemistries that must be properly managed to meet the customer's exacting manufacturing tolerances.
Breaking Down the Pattern Plating Process
We start with a pattern: The circuit board design is created with a photoresist mask exposing all the traces and pads to the copper foil or plated copper below it. The next step is plating copper on top of the pattern. This builds copper thickness inside the holes, on the surface, along the traces, and on the pads.
This process beefs up the copper thickness of the outer layer copper features of the board to create the current capacity specified in the design. It is important to ensure that the channels created by the photoresist are deep enough to accommodate the amount of copper required. If they are not, copper will plate over the top of the resist, creating a mushroom at the top of the trace that can be harder to etch out from underneath and create overhanging copper that can break off, form a bridge, and cause shorts.
Preparing Surfaces for Pattern Plating
We ensure the copper surface is pristine so we can plate brand-new copper atop it. This involves a surface treatment process called micro-etching and running the board through a pattern plate pre-clean. We use a series of sulfuric acid rinses and micro-etches to remove any oxidation and impurities on the surface created during the imaging process.
If residual developer solution or photoresist is present, the cleaning process should eliminate it and leave a clean copper surface. During this process, we are careful not to disturb the dry film we put in place or overclean the surface to where we have etched the copper out of the holes, which we invested time and effort in metallizing during the electroless copper process.
Avoiding Overcleaning
This balancing act involves ensuring the electroless copper deposit is thick enough to account for how much is removed during the pre-plating, pre-clean process. We use an SPC tool called an etch rate coupon to determine how much copper we remove during the micro-etch process. That measurement quantifies the amount of copper being removed. Time in the bath and/or the bath temperature can be adjusted to target the desired amount of removal.
However, etch rates are not necessarily constant. They are influenced by temperature, concentration, and copper loading. If you make a new solution of micro-etch without copper in the bath, it won’t etch. Adding copper starts the chemical reaction.
Etch rates vary day to day, even shift to shift, depending on how much use the chemicals see. There are many variables in this process: the chemistry behavior, aggressiveness in etch, and changes in temperature or humidity on the production floor. The etch rate coupon helps manufacturers ensure they are removing copper within the appropriate window.
A Picture of the Plating Floor
The size and layout of plating operations can vary by manufacturer. Our plating floor has six tanks, each holding 205 gallons of blue copper sulfate plating solution. The tanks have copper bars (cathodes) running down the middle where the manufacturing panels are connected, and baskets filled with copper balls (anodes) on the outside of the cell. Those run to our rectifier—the electricity source that creates the electrolytic plating cell.
In the last step before the copper bath, we dip the panel into a tank of sulfuric acid (~10%). This concentration is like the plating bath and helps eliminate dilution due to the drag-out of water coming into the copper bath.
Adhering Copper to the Board
The panels go into the copper bath using a conductive flight bar to hold them. The flight bar is screwed onto the copper cathode bars in the plating cell for a tight electrical connection. The copper anodes on the outer edge receive a negative charge. When we turn on the juice, the copper anodes begin to dissolve in the solution, and the positive copper ions are attracted to the panel’s surface where they undergo a reduction-oxidation (redox) reaction, reducing it to copper metal and giving off hydrogen gas. The copper metal adheres to the board where the electricity initiates the redox reaction.
Elements of this process are visible to the human eye. You can see the color of the copper change on the panel’s surface and the hydrogen in the form of bubbles created by the chemical reaction. We blow air over both sides of the panels to sweep away the hydrogen. This helps avoid leaving microbubbles on the surfaces we are trying to plate.
The goal is to get copper into the holes. We refer to this as “throw.” In a perfect world, we want to plate as much copper at the center of the hole as at the edge or knee of the hole, or even more. Then there’s reality.
It is a lot easier for a free-floating copper ion to slam into the horizontal surface of the board than to dive into a via-hole. To encourage the ions to go where we want them, we must sway the panels and encourage solution in and out of the holes, sweeping them back and forth in the solution. This creates more surface tension to push the solution into and out of the holes.
If our only concern during plating was whether the panels were swaying (agitating), it would be a straightforward process. However, our work happens on a very small scale with some incredibly tight tolerances and many opportunities for variation. Several elements create variations in the copper tanks.
Variations in the Copper Tanks
First, there is the makeup of the chemistry bath itself. There are at least five chemical components that make up a copper bath, and it’s imperative to have them in the correct ratio for the intended output of the plating cell. Depending on the setup of the chemical ratio, the bath can perform differently: higher throw = slower plating times, lower throw = faster plating times, high current density plating, low current density plating, etc.
Copper plating is not simply about the copper concentration and the sulfuric acid (electrolyte) concentration. We need to consider other components in the bath, including proprietary levelers and brighteners. Brighteners, as their name sounds, brighten the copper deposit. The copper from electroless and foil is matte and pinkish. Once it’s plated, the result is the shiny copper deposit we all expect—one with a grain structure that optimizes current flow. Levelers help fill in any small imperfections that may have existed at the start of the plating process. They do an excellent job of filling in gaps and creating a uniform, level copper surface.
During the plating process, our components are consumed or broken down at varying rates, jeopardizing our chemical ratios. To ensure that the chemical processes operate at the correct concentrations and ratios, we use analytical chemical processes across all our chemical baths to confirm the concentrations of all the components.
Technicians take samples and measure sulfuric acid, copper, chloride, brightener, and leveler content. They will make additions or dilutions to keep the bath within the optimal operating window. The brighteners and levelers break down over time and create organic impurities. When they reach the tolerance threshold, the bath will be taken offline and cleaned with a carbon filtering process to remove the impurities. The filtering and chemical oxidation process reduces the bath to almost purely sulfuric acid and copper sulfate, so the brighteners and levelers must be added back to the solution.
Preparing for the Next Phase of Manufacturing
Once the plating is complete, our boards are freshly coated with copper, dripping sulfuric acid, and copper sulfate. Next, we rinse them off and put them directly into an electrolytic tin plating process that is identical to the copper plating process. The result is a layer of tin atop the copper.
That tin becomes our etch resist. After we add it to the board, we remove the photoresist and expose all the unwanted copper below. The tin protects the copper we want during etching. Now that we have protection over the copper traces, pads, and vias, we are ready for the strip/etch/strip (SES) process.
This will be the subject of my next article. If you are eager to learn more now, listen to episode 9 of On the Line with… where we discuss SES.
Read Matt’s book, The Printed Circuit Designer’s Guide to… Designing for Reality, or listen to his podcast here.
This column originally appeared in the October 2024 issue of Design007 Magazine.
More Columns from Connect the Dots
Connect the Dots: Designing for Reality—Outer Layer ImagingConnect the Dots: Designing for Reality—Electroless Copper
Connect the Dots: Navigating the Intricacies of PCB Drilling
Connect the Dots: Designing for Reality—Lamination and Materials
Connect the Dots: Designing for Reality—The Physical Manufacturing Phases
Connect the Dots: Designing for Reality—The Pre-Manufacturing Process
Connect the Dots: Designing for Reality: Prioritizing Manufacturability
Connect the Dots: Are You Ready for 2024?