-
- News
- Books
Featured Books
- pcb007 Magazine
Latest Issues
Current IssueInventing the Future with SEL
Two years after launching its state-of-the-art PCB facility, SEL shares lessons in vision, execution, and innovation, plus insights from industry icons and technology leaders shaping the future of PCB fabrication.
Sales: From Pitch to PO
From the first cold call to finally receiving that first purchase order, the July PCB007 Magazine breaks down some critical parts of the sales stack. To up your sales game, read on!
The Hole Truth: Via Integrity in an HDI World
From the drilled hole to registration across multiple sequential lamination cycles, to the quality of your copper plating, via reliability in an HDI world is becoming an ever-greater challenge. This month we look at “The Hole Truth,” from creating the “perfect” via to how you can assure via quality and reliability, the first time, every time.
- Articles
- Columns
- Links
- Media kit
||| MENU - pcb007 Magazine
Estimated reading time: 6 minutes
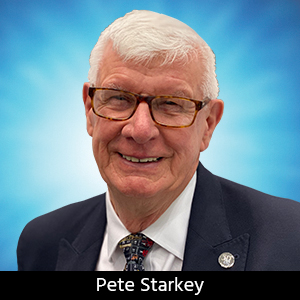
Contact Columnist Form
Institute of Circuit Technology's 2014 Darlington Seminar
Brown took the multilayer layup process as his example to review and considered issues associated with the use of thin copper foils, speculating upon the possibilities of making thin copper foils easier to handle and less vulnerable to damage, and protecting them against particulate contamination. Was this too much to expect? In Brown’s view it was not a dream, but a practical reality and the answer was to laminate the copper foil with a proprietary protective film at the roll stage, prior to panelising. The protective film supported and protected copper during foil handling and throughout the lamination process, and was simply peeled off at the breakdown stage.
Benefits included the elimination of epoxy spots and a reduction in pits and dents due to airborne particulates or damaged separator plates. In his experience this protective film significantly improved handling of thinnest copper foils, speeded-up the lay-up process, allowed user the choice of steel or aluminium separator plates and was suitable for automated handling systems. As a potential further economy, traditionally-generous oversizes on foil could be reduced.
Dr. Andrew Cobley, director of the Functional Materials Research Group at Coventry University, gave a presentation entitled “Conductive Fabrics to Enable Wearable Electronics” describing a new Knowledge Transfer Partnership project, in which Coventry University were collaborating with the National Physical Laboratory (NPL).
There was an increasing demand for wearable technology from industry sectors such as medical and healthcare, sport and fitness, consumer electronics and defence. The world market for wearable e-textiles was projected to grow from approximately $300 million to $1.5 billion by 2020, and healthcare would remain the dominant sector.
Various methods were available to introduce electrical conductivity into a fabric: Woven metal threads, metal-coated fibres, carbon fibres, printed or deposited conductive polymers and inks, or plasma deposition of metal. Disadvantages of current methods were the poor conductivity of non-metallic fibres, the limited bendability and stretchability of metallic fibres and difficulties in achieving selective conductivity. Washability of conductive fabrics was an essential requirement.
The approach being taken in this KTN project was to fully encapsulate fibres within the fabric with a coating of nano-silver particles, formed in-situ on a chemically functionalised textile material. This resulted in 100% encapsulation of fibres in a 20 nanometre silver coating with excellent adhesion, flexibility and wash-resistance, although conductivity was limited but could be improved by electroless copper plating and applying immersion silver as a final finish. The process had been successfully demonstrated on a wide range of natural and synthetic textiles. The principles established presented opportunities for selective functionalisation by ink-jet or screen printing, such that useable electrical circuits could be created within the fabric.
Page 2 of 3
More Columns from The European Angle
CircuitData: A New Open Standard for PCB Fab Data ExchangeI Never Realised It Was So Complicated!
The European Angle: Institute of Circuit Technology 43rd Annual Symposium
Ventec International Group's Martin Cotton Celebrates 50 Years in PCB Design
Reporting on the Institute of Circuit Technology Spring Seminar
EuroTech: Raw Materials Supply Chain—Critical Challenges Facing the PCB Industry
EuroTech: ENIPIG—Next Generation of PCB Surface Finish
EuroTech: Institute of Circuit Technology Northern Seminar 2016, Harrogate