-
- News
- Books
Featured Books
- pcb007 Magazine
Latest Issues
Current IssueInventing the Future with SEL
Two years after launching its state-of-the-art PCB facility, SEL shares lessons in vision, execution, and innovation, plus insights from industry icons and technology leaders shaping the future of PCB fabrication.
Sales: From Pitch to PO
From the first cold call to finally receiving that first purchase order, the July PCB007 Magazine breaks down some critical parts of the sales stack. To up your sales game, read on!
The Hole Truth: Via Integrity in an HDI World
From the drilled hole to registration across multiple sequential lamination cycles, to the quality of your copper plating, via reliability in an HDI world is becoming an ever-greater challenge. This month we look at “The Hole Truth,” from creating the “perfect” via to how you can assure via quality and reliability, the first time, every time.
- Articles
- Columns
- Links
- Media kit
||| MENU - pcb007 Magazine
Estimated reading time: 7 minutes
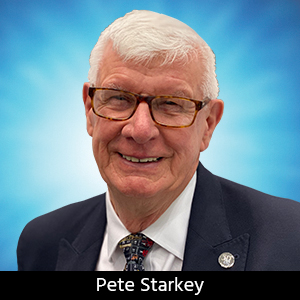
Contact Columnist Form
The Story Behind the News: ESA Approval at Invotec
Starkey: And what pressures are placed on your manufacturing capacity?
Tatton: This sort of work is well within our manufacturing capability. We have many years’ experience of the sort of technologies involved. In terms of capacity, it fits smoothly into our production flow; we are, by nature, a low-volume, high-mix, high-reliability PCB manufacturer. There are some challenges, for example in front end engineering, electrical testing and final inspection. ESA are extremely cautious and demand high-voltage electrical testing on many of their designs. It’s not practicable to build grid-test fixtures for such complex boards in such small quantities, so we have to adapt our flying-probe testers to suit.
Starkey: What are typical characteristics of ESA work?
Tatton: Often large boards, all polyimide, high layer count--generally 20- to 30-layer sequential build, and with finish requirements like reflowed tin-lead with a minimum of 2 microns at the knee of the hole, often in combination with fully-encapsulant electroplated gold over nickel. And the QA testing requirements are not for the faint-hearted. Look at the active circuit area on this panel and compare it with the area dedicated to coupons for a whole catalogue of release tests. The job probably spends as long in inspection and laboratory test than it does in manufacture, but that’s the reality of ESA work.
Starkey: How long did it take to go through the qualification procedure?
Tatton: It was a three year programme--pretty challenging--with many iterations of test coupons. We were sponsored by Airbus Defence and Space, a division of Airbus Group that was part of EADS Astrium before they re-structured. We had been supplying them with high-reliability HDI product for 10 years in advance of the ESA approval and we are now able to support their ESA-qualified requirements, a big benefit to them as well as to us. And our ESA accreditation represents a formal acknowledgement of our technological and manufacturing capability as well as the strength of our commitment to ultra-high reliability.
Starkey: Tim, you already mentioned the unprecedented market response following the announcement of your approval. Are you able to disclose what proportion of your business is attributable to ESA work?
Tatton: It’s obviously an area of rapid growth for us, and currently constitutes about 5% of our turnover. We believe that we can progressively increase this to 15%, which will represent a significant share of the European space market. From our point of view, that’s a manageable share in view of the year-on-year variance in demand, and puts in a much more secure position than companies with 60 to 70% of their turnover committed to the space sector. We have the strength and resources to cooperate with our customers to find ways to control and manage change, where change is necessary, to realise meaningful continuous improvements.
Starkey: Sounds like a pretty good strategy to me, Tim. Thanks for sharing your experiences with us. Every success, and please invite me back to see your new laboratory when it’s ready.
Page 3 of 3More Columns from The European Angle
CircuitData: A New Open Standard for PCB Fab Data ExchangeI Never Realised It Was So Complicated!
The European Angle: Institute of Circuit Technology 43rd Annual Symposium
Ventec International Group's Martin Cotton Celebrates 50 Years in PCB Design
Reporting on the Institute of Circuit Technology Spring Seminar
EuroTech: Raw Materials Supply Chain—Critical Challenges Facing the PCB Industry
EuroTech: ENIPIG—Next Generation of PCB Surface Finish
EuroTech: Institute of Circuit Technology Northern Seminar 2016, Harrogate