-
- News
- Books
Featured Books
- pcb007 Magazine
Latest Issues
Current IssueInventing the Future with SEL
Two years after launching its state-of-the-art PCB facility, SEL shares lessons in vision, execution, and innovation, plus insights from industry icons and technology leaders shaping the future of PCB fabrication.
Sales: From Pitch to PO
From the first cold call to finally receiving that first purchase order, the July PCB007 Magazine breaks down some critical parts of the sales stack. To up your sales game, read on!
The Hole Truth: Via Integrity in an HDI World
From the drilled hole to registration across multiple sequential lamination cycles, to the quality of your copper plating, via reliability in an HDI world is becoming an ever-greater challenge. This month we look at “The Hole Truth,” from creating the “perfect” via to how you can assure via quality and reliability, the first time, every time.
- Articles
- Columns
- Links
- Media kit
||| MENU - pcb007 Magazine
Estimated reading time: 7 minutes
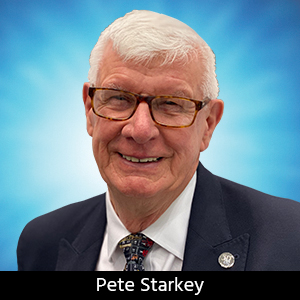
Contact Columnist Form
The Story Behind the News: ESA Approval at Invotec
Starkey: Can you give some examples?
Tatton: Clearly, safety is the critical priority for civil aircraft, but their electronic systems are designed with multiple redundancies so that in the event of a failure, there is usually a back-up system to maintain functionality until the aircraft can be grounded and a replacement module fitted. The commercial consideration is that while an aircraft is grounded it is not generating revenue. In the case of a satellite, the reliability issue is magnified to another level--because of constraints of weight and physical space, multiple back-up systems are just not practicable and the cost of failure is colossal. For example, last year, the European Space Agency launched the Gaia satellite, an unmanned space observatory. It’s currently about 1.5 million kilometres from Earth. It cost a billion dollars to develop and launch.
Starkey: Yes, that puts it in perspective. So how do these considerations affect the role of the PCB manufacturer?
Tatton: Traditionally, the focus has been on inspection and test. But you can’t inspect quality into a product--you have to get the materials and processes right so that you can manufacture the quality in in the first place. Inclusions in laminates are a known source of latent short circuits; we’ve been working with our laminate suppliers for the last five years to help them eliminate inclusions at source and at the same time we have made substantial investment in clean-room facilities and working procedures to avoid inclusions during manufacture. We have earned a lot of credibility with the space OEMs over the many years we have been supplying them, with a whole suite of approvals that demonstrate our process excellence, including NADCAP and AS9100 Rev C accreditation in addition to all of our OEM approvals, many of which call for capability beyond the scope of current ESA requirements.
In particular, our Tamworth factory is the only ESA-approved facility with a full in-house HDI capability and we are looking forward to working with ESA to develop new standards for the use of HDI in their designs. Because ESA operate a traditional system, much like the old MIL-Spec, it can take a long time for technology advancements to become incorporated. As a consequence, OEMs have where necessary developed their own individual specifications.
Starkey: What about the smaller space contractors?
Tatton: A number of smaller companies and research institutions engaged in commercial space projects do not have the resources for formally qualifying their PCB suppliers. Since the announcement of our ESA approvals, we have had many approaches from such organisations, several of which we weren’t previously aware of. Although technically they may not need ESA approval, they see it as a de-facto standard and call it up anyway.
Starkey: These opportunities aside, Invotec must now be in a very strong position to address the mainstream space sector.
Tatton: We have been very pleasantly surprised. Since our initial announcement in January this year, we have had orders from 20 different customers in 12 different countries, plus around 20 further new enquiries, several of which from outside Europe. It takes very careful management to assimilate so many new customers, particularly when each of them has their own special requirements, but we have the right engineering and quality assurance resources to support them and I’m pleased to say that we have coped pretty well.
Page 2 of 3
More Columns from The European Angle
CircuitData: A New Open Standard for PCB Fab Data ExchangeI Never Realised It Was So Complicated!
The European Angle: Institute of Circuit Technology 43rd Annual Symposium
Ventec International Group's Martin Cotton Celebrates 50 Years in PCB Design
Reporting on the Institute of Circuit Technology Spring Seminar
EuroTech: Raw Materials Supply Chain—Critical Challenges Facing the PCB Industry
EuroTech: ENIPIG—Next Generation of PCB Surface Finish
EuroTech: Institute of Circuit Technology Northern Seminar 2016, Harrogate