-
- News
- Books
Featured Books
- pcb007 Magazine
Latest Issues
Current IssueInventing the Future with SEL
Two years after launching its state-of-the-art PCB facility, SEL shares lessons in vision, execution, and innovation, plus insights from industry icons and technology leaders shaping the future of PCB fabrication.
Sales: From Pitch to PO
From the first cold call to finally receiving that first purchase order, the July PCB007 Magazine breaks down some critical parts of the sales stack. To up your sales game, read on!
The Hole Truth: Via Integrity in an HDI World
From the drilled hole to registration across multiple sequential lamination cycles, to the quality of your copper plating, via reliability in an HDI world is becoming an ever-greater challenge. This month we look at “The Hole Truth,” from creating the “perfect” via to how you can assure via quality and reliability, the first time, every time.
- Articles
- Columns
- Links
- Media kit
||| MENU - pcb007 Magazine
Estimated reading time: 15 minutes
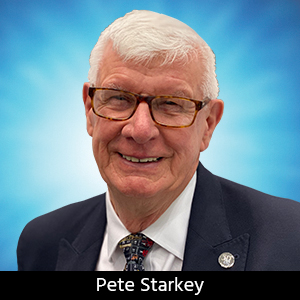
Contact Columnist Form
SMART Group Seminar: Harsh Environments & Electronics
A full-house international audience assembled at the National Physical Laboratory in Teddington, London, England, July 2, 2014, for SMART Group’s seminar on Electronics in Harsh Environments, welcomed by Dr. Chris Hunt, leader of the electronics interconnection team at NPL, the national measurement standards laboratory for the United Kingdom, and the largest applied physics organisation in the UK.
Chair of SMART Group Technical Committee Sue Knight, from STI, gave the first presentation, an introduction from her perspective as a high-end electronics manufacturing engineer. Harsh operating environments were commonplace: She gave examples in telecommunications, oil exploration and power generation, aerospace instrumentation, sensors, motors and actuators, and industrial controllers and sensors. And although high temperature probably represented the area of most concern in maintaining the integrity of substrates, components and interconnections, stresses generally occurred in combination: Typical additional factors being mechanical shock and vibration as well as humidity and chemistry.
As an illustration, Knight described the extreme conditions endured by the electronics mounted in an intelligent, directable drill bit used in oil exploration. Historically, sensing electronics had been mounted at least 10 metres back from the cutting tip of the drill. Presently, to get precise, real-time feedback to monitor performance and improve positional control, complex electronics assemblies were mounted very close to the actual drill bit. Pressures of 25,000 psi and temperatures in excess of 150°C were typical, even though the assemblies were built with commercial-specification components. Current challenges were to operate at pressures up to 30,000 psi and temperatures approaching 230°C, under conditions of extreme shock and vibration as well as the presence of dirt, steam, and slurry. The cost of failure was significant, so reliability was paramount and the manufacturer was responsible for validating that the tool would perform to expectations, modelling and verifying build quality and sensor and tool operation under extremes of temperature and vibration.
What was the relevance to everyday electronics? Knight explained how research and development generated at high level could be subsequently applied to benefit the functionality and reliability of commercially-available equipment. And how could the challenges be overcome? “I have just outlined some of the issues--the other presenters will explain how to solve them,” she said.
Alun Morgan, Isola Group’s director of OEM Marketing and a leading authority on laminate properties and applications, has a particular aptitude for explaining complex technology in a clear and understandable style. Invited to make a presentation on base materials for harsh environments, he admitted being tempted to save time by offering two words of advice--“use polyimide”--and sitting down again! But polyimide was not necessarily a universal solution: If properties were correctly understood and materials intelligently selected to suit the application, many cost-effective and in certain cases technically superior alternatives existed.
Page 1 of 7
More Columns from The European Angle
CircuitData: A New Open Standard for PCB Fab Data ExchangeI Never Realised It Was So Complicated!
The European Angle: Institute of Circuit Technology 43rd Annual Symposium
Ventec International Group's Martin Cotton Celebrates 50 Years in PCB Design
Reporting on the Institute of Circuit Technology Spring Seminar
EuroTech: Raw Materials Supply Chain—Critical Challenges Facing the PCB Industry
EuroTech: ENIPIG—Next Generation of PCB Surface Finish
EuroTech: Institute of Circuit Technology Northern Seminar 2016, Harrogate