-
- News
- Books
Featured Books
- pcb007 Magazine
Latest Issues
Current IssueInventing the Future with SEL
Two years after launching its state-of-the-art PCB facility, SEL shares lessons in vision, execution, and innovation, plus insights from industry icons and technology leaders shaping the future of PCB fabrication.
Sales: From Pitch to PO
From the first cold call to finally receiving that first purchase order, the July PCB007 Magazine breaks down some critical parts of the sales stack. To up your sales game, read on!
The Hole Truth: Via Integrity in an HDI World
From the drilled hole to registration across multiple sequential lamination cycles, to the quality of your copper plating, via reliability in an HDI world is becoming an ever-greater challenge. This month we look at “The Hole Truth,” from creating the “perfect” via to how you can assure via quality and reliability, the first time, every time.
- Articles
- Columns
- Links
- Media kit
||| MENU - pcb007 Magazine
Estimated reading time: 15 minutes
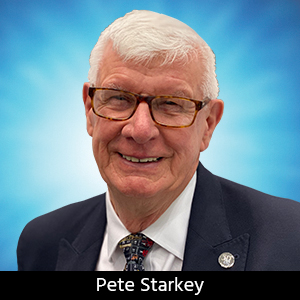
Contact Columnist Form
NPL/SMART Group Conformal Coating & Cleaning Experience
Nominating flux as the root cause of most cleaning issues, he speculated on how many different flux chemistries there might be on the market, arriving at a figure of approximately 150, and asked: “Do all these fluxes demand the same cleaning?” Likening the nomination of a single cleaning process to a game of Russian Roulette, he explained the significance of J-STD-001E requirements for soldered electrical and electronic assemblies, and its associated standards for solder, flux and paste, and the differences between “Acceptable,” “Process Indicator,” and “Defect,” with a reminder that an assembler who does not have these standards included in his own specification cannot claim to comply with them.
Finally, he reviewed IPC-610: “It won’t solve the problem--it will cost you money!” and the workmanship standards for polymeric coatings defined in NASA-STD-8739. His closing words were: “The winner has a plan, the loser has an excuse!”
Nordson Yestech AOI Specialist Andy Bonner talked about techniques for automated conformal coating inspection. He reviewed systems with top-down and side-viewing cameras and a choice of white, red, or UV illumination, and algorithms specific to conformal coat inspection and parts inspection. “Look for the blue bits, and a few other things…” giving examples of bubble defect detection, coating or no coating on pads and through hole pins, coating inside connectors, and cracks and delamination that could be detected. Side angle camera inspection gave the opportunity to inspect coverage on hidden coating areas and review tools enabled operators to determine whether true defects existed.
Detection of defects was only part of the story: It was also possible to record all of the defect data and generate detailed reports on assemblies, works orders, individual boards, systems and operators, and to seamlessly drill down from an assembly to an individual defect within the report viewer.
Next hour, attention turned to the cleaning of PCB assemblies for coating, with a presentation from Graham Fraser of Fraser Technologies on high density interconnects, assembly process cleaning integration and assembly cleaning options. He made it clear that although electronics cleaning had made substantial progress in the past 40 years, lead-free soldering and low stand-off components in high-reliability applications meant it had never been more important to ensure that cleaning was both effective and measurable. And as the complexity of electronic assemblies continued to advance, the removal of process residues became an increasingly complex issue.
He discussed the cause-effect relationships between board design, paste or flux, cleaning agent, and cleaning machine to be considered in achieving an ideal cleaning condition.
When no-clean fluxes were first introduced, spacing between conductors was larger, residues posed minimal reliability risks, and, in many applications, cleaning was not required. As distances between conductors narrowed and Z-axis clearances reduced, residues of non-reacted flux activators under component gaps posed an increasing reliability risk.
Page 5 of 7
More Columns from The European Angle
CircuitData: A New Open Standard for PCB Fab Data ExchangeI Never Realised It Was So Complicated!
The European Angle: Institute of Circuit Technology 43rd Annual Symposium
Ventec International Group's Martin Cotton Celebrates 50 Years in PCB Design
Reporting on the Institute of Circuit Technology Spring Seminar
EuroTech: Raw Materials Supply Chain—Critical Challenges Facing the PCB Industry
EuroTech: ENIPIG—Next Generation of PCB Surface Finish
EuroTech: Institute of Circuit Technology Northern Seminar 2016, Harrogate