-
- News
- Books
Featured Books
- pcb007 Magazine
Latest Issues
Current IssueInventing the Future with SEL
Two years after launching its state-of-the-art PCB facility, SEL shares lessons in vision, execution, and innovation, plus insights from industry icons and technology leaders shaping the future of PCB fabrication.
Sales: From Pitch to PO
From the first cold call to finally receiving that first purchase order, the July PCB007 Magazine breaks down some critical parts of the sales stack. To up your sales game, read on!
The Hole Truth: Via Integrity in an HDI World
From the drilled hole to registration across multiple sequential lamination cycles, to the quality of your copper plating, via reliability in an HDI world is becoming an ever-greater challenge. This month we look at “The Hole Truth,” from creating the “perfect” via to how you can assure via quality and reliability, the first time, every time.
- Articles
- Columns
- Links
- Media kit
||| MENU - pcb007 Magazine
Estimated reading time: 15 minutes
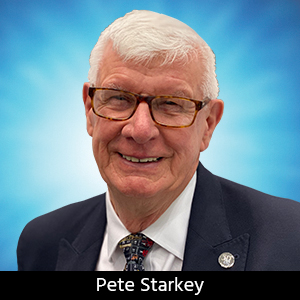
Contact Columnist Form
NPL/SMART Group Conformal Coating & Cleaning Experience
“Flux residues are not created equally!” Today’s soils tended to be harder to clean, and cleaning agents had evolved to match the soil properties. Increased wash times were needed as gaps became smaller. Wash temperature was dependent on the nature of the soil: For some soils, higher wash temperatures were preferred whereas on some others, lower wash temperatures gave better results. Wash concentration needed to be optimised to match the cleaning agent to the soil, and an increase over optimum gave no technical benefit but increased process cost. And getting the cleaning chemistry out of the assembly at the end of the process was an equally important consideration--all aqueous formulations would leave residues if not completely washed out.
Reviewing the choice of cleaning equipment available, he stressed that the importance of cleaning needed to be considered as a priority in setting up an assembly line: “Don’t spend all the budget on the latest pick-and-place machine then find you have to cut corners on the cleaning process! Talk to your suppliers and get your evaluations done up-front” was the message.
Willis rounded off the second day’s programme with a review of available literature on cleaning and practical advice on confirming component compatibility with cleaning materials, performing simple tests like weight change after immersion, stability of marking, and degradation of wrapping materials. Some component issues were very obvious, but care needed to be taken with assessment to avoid short- or long-term reliability problems. A contentious issue was the presumption that ultrasonic cleaning was potentially damaging to components with wire-bonded interconnects. In his long experience, he had never seen a failure attributable to ultrasonics, even in instances of grossly excessive exposure.
Day Three
Bob Willis introduced the final day’s seminar and workshop sessions with a discussion of the advantages and disadvantages of performing the conformal coating operation in-house or contracting it out. He outlined he requirements for a production facility: A dedicated area of the factory with temperature and humidity control, ventilation and extraction, facilities for material storage and material disposal, as well as coating, drying, inspection, and rework equipment, and associated health and safety considerations. The benefits of using a contract service included access to considerable expertise in coating and no capital equipment or additional personnel costs. Weighed against these were the considerations of lead times and work scheduling, costs of coating service plus packaging and transport, and the need for vendor assessment and approval. To illustrate cost, Willis did calculations based on price per hour for labour, overheads, and profit, together with material costs for conformal coating and masking, arriving at figures between £4.00 to £6.00 per assembly depending on coating method.
His next topic was PCB contamination testing options, and he reviewed commonly-used techniques and documented standards. Visual inspection could give valuable information, especially if UV tracers were present in the flux, particularly in identifying possible traps for cleaning and drying residues. As a process control tool, ROSE testing was frequently used for cleanliness monitoring to IPC, IEC, and MIL specs, using 50/50 or 75/25 IPA/water to extract ionic material then measuring the resistivity of the extract.
Meaningful measurement of contamination on a board required consideration of the total time and the rate at which the contamination rose over time. Ionic contamination could originate from soldering materials, the printed board surfaces, fabrication materials, and other sources. Although many people were happy with a result less than the specification limit, much more useful information could be gained by observing the shape of the graphs, and Willis showed examples of results from different PCB solderable finishes and soldering methods. For actual surface analysis or comparison of residues with known process materials he recommended having infra-red spectrometry or ion chromatography carried out by a specialist laboratory.
SIR testing could be carried out on bare PCB coupons, or coupons with components, and could be used at any stage of the process. But he recommended that simpler tests be done first to get the process as well under control as possible before committing to the time and expense of SIR measurement.
His third session was a review of test methods for conformal coating reliability, with reference to IPC-CC-830B; Qualification and Performance of Electrical Insulation Compound for PCBA, IPC-HDBK-830A: Guidelines for Design, Selection and Application of Conformal Coating, and IPC-TM-650: Test Methods Manual.
The conformal coating and cleaning experience concluded with a discussion of conformal coatings defects, causes, and cures. Stressing again the importance of starting with clean surfaces before contemplating any conformal coating process, Willis reviewed the assembly operation with regard to the compatibility of PCB and component finishes, fluxes, soldering conditions, and cleaning chemistry, then gave examples of coating and cleaning defects.
Page 6 of 7
More Columns from The European Angle
CircuitData: A New Open Standard for PCB Fab Data ExchangeI Never Realised It Was So Complicated!
The European Angle: Institute of Circuit Technology 43rd Annual Symposium
Ventec International Group's Martin Cotton Celebrates 50 Years in PCB Design
Reporting on the Institute of Circuit Technology Spring Seminar
EuroTech: Raw Materials Supply Chain—Critical Challenges Facing the PCB Industry
EuroTech: ENIPIG—Next Generation of PCB Surface Finish
EuroTech: Institute of Circuit Technology Northern Seminar 2016, Harrogate