-
- News
- Books
Featured Books
- design007 Magazine
Latest Issues
Current IssueShowing Some Constraint
A strong design constraint strategy carefully balances a wide range of electrical and manufacturing trade-offs. This month, we explore the key requirements, common challenges, and best practices behind building an effective constraint strategy.
All About That Route
Most designers favor manual routing, but today's interactive autorouters may be changing designers' minds by allowing users more direct control. In this issue, our expert contributors discuss a variety of manual and autorouting strategies.
Creating the Ideal Data Package
Why is it so difficult to create the ideal data package? Many of these simple errors can be alleviated by paying attention to detail—and knowing what issues to look out for. So, this month, our experts weigh in on the best practices for creating the ideal design data package for your design.
- Articles
- Columns
- Links
- Media kit
||| MENU - design007 Magazine
Estimated reading time: 2 minutes
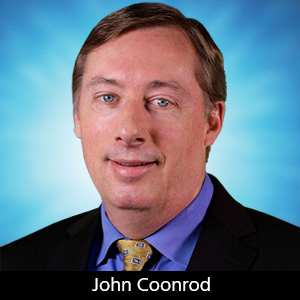
Why Do Different Test Methods Yield Different Electrical Values?
A variety of different test methods may be used for any one electrical concern. This article will discuss the issues related to determining the dielectric constant (Dk) and dissipation factor (Df or Tan-Delta). On a data sheet, a designer may see a Dk value for a material to be 3.5, as an example. Once the designer buys the material and performs necessary evaluations, it may be found that the Dk of the material is 3.8. In some applications this difference in Dk is probably not meaningful; however, for many RF and high-speed digital applications, this difference could be very significant. What is really interesting about this example is that the two Dk values may both be correct, depending on the test methods used.
Most laminates used in the PCB industry are anisotropic and this means that the electrical properties are not the same on all three axes of the material. Typically the thickness (z-axis) of the material will have a different Dk value than the x or y axes of the material. The reasons for this depend on what type of material is being considered.
The laminates used in the PCB industry are typically woven-glass reinforced, however there are notable exceptions. The glass reinforcement layer typically has a different Dk and Df than does the raw substrate of the laminate. The standard E-glass most often used in PCB laminates has a typical Dk value of about 6 and a dissipation factor of around 0.004. The common FR-4 laminates use relatively simple resin systems and the resin itself has a Dk that is around 3 and a Df of about 0.03. Different ratios of resin to glass will cause the laminate to have a Dk that is somewhere between the value of the resin and that of the glass. However, the glass-resin ratio impact on Dk is usually considered when evaluating the material through the thickness axis and if the x- or y-axis is evaluated, the Dk value may be very different than the z-axis result.
A large number of test methods are available to evaluate materials for Dk and Df. The methods that are most often used in the PCB laminate industry for making these measurements are typically tailored to evaluating materials in very large volume. Because of this issue, these test methods need to determine Dk and Df relatively fast, have good repeatability, and be used for quality control. A common test method used is the clamped stripline resonator, where a clamping fixture is used to form a stripline structure; the layer structure of a stripline is ground-signal-ground. This test method determines the Dk and Df of the material in the clamped fixture and more specifically, it is reporting these values related to the thickness axis of the material.
To read this entire article, which appeared in the December 2015 issue of The PCB Design Magazine, click here.
More Columns from Lightning Speed Laminates
Lightning Speed Laminates: Millimeter-wave Properties and PCB Design ChallengesLightning Speed Laminates: Optimizing Thermal Management for Wireless Communication Systems
Lightning Speed Laminates: Test Vehicles for PCB Electrical Material Characterization
Lightning Speed Laminates: Optimum Thermal Stability Considerations
Lightning Speed Laminates: Thermal Management Isn’t Getting Easier
Lightning Speed Laminates: Benefits of High-Performance Hybrid Multilayer PCBs
Lightning Speed Laminates: An Overview of Copper Foils
Lightning Speed Laminates: The Importance of Circuit Features for Millimeter-Wave Applications