-
- News
- Books
Featured Books
- pcb007 Magazine
Latest Issues
Current IssueSales: From Pitch to PO
From the first cold call to finally receiving that first purchase order, the July PCB007 Magazine breaks down some critical parts of the sales stack. To up your sales game, read on!
The Hole Truth: Via Integrity in an HDI World
From the drilled hole to registration across multiple sequential lamination cycles, to the quality of your copper plating, via reliability in an HDI world is becoming an ever-greater challenge. This month we look at “The Hole Truth,” from creating the “perfect” via to how you can assure via quality and reliability, the first time, every time.
In Pursuit of Perfection: Defect Reduction
For bare PCB board fabrication, defect reduction is a critical aspect of a company's bottom line profitability. In this issue, we examine how imaging, etching, and plating processes can provide information and insight into reducing defects and increasing yields.
- Articles
- Columns
- Links
- Media kit
||| MENU - pcb007 Magazine
Estimated reading time: 5 minutes
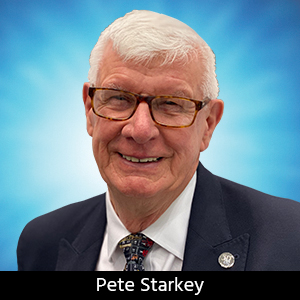
Contact Columnist Form
HASLEN: An Obituary to Black Pad
“HASLEN: An Obituary to Black Pad”--a bold title, bound to attract attention and provoke controversy. The term "Black Pad" has been used since the late '90s to describe a type of solder joint failure associated with electroless nickel immersion gold (ENIG) PCB finishes, where solder separates from from the electroless nickel surface leaving a black or dark grey deposit. Many theories have been considered as to the cause, but recent research suggests the effect originates from hypercorrosion of the nickel-phosphorus deposit during the immersion gold plating process.
A webinar presented by ITRI Innovation introduced a new solderable finish known as HASLEN, combining features of two established technologies to deposit solder directly on to electroless nickel by hot air solder leveling, and made possible by novel fluxes based on deep eutectic solvents. The HASLEN finish was claimed to reduce cost and to offer overall improvements in the longevity and reliability of PCB assemblies when compared with ENIG.
A background perspective was provided by Nick Hoo, Materials Technology manager at ITRI Innovation, who summarised the characteristics of currently available solderable finishes for PCBs and focused on the properties of ENIG: Its excellent solderability and solderability retention on storage and after multiple reflow, good planarity, low substrate dissolution, and low intermetallic growth during soldering or in the solid state because of the nickel diffusion barrier between tin and copper in the final joint. Set against these attributes were the disadvantages of high cost and loss of high frequency signal integrity, and issues such as black pad, nickel passivation, gold coating porosity and nickel-copper migration.
Hoo shared the opinion that black pad was a consequence of excessive corrosion of the nickel coating during the immersion gold process, although the term appeared to have become a catch-all for problems encountered with ENIG coatings. He referred to an observation, made during the EU-funded ASPIS project when ionic liquid technology had been investigated as a basis of alternative plating methods, that the properties of certain ionic liquids offered scope for development as soldering fluxes for electronics applications.
The University of Leicester, a collaborator in the ASPIS project, has been for many years the centre for research in ionic liquids, resulting in the development of many specialist metal finishing applications. Dr. Andrew Ballantyne described how a class of ionic liquids known as deep eutectic solvents (DES), which were low cost and environmentally benign, exhibited an exceptional ability to dissolve metal oxides without the use of acids. Used as the basis of soldering fluxes, these materials could effectively clean metal surfaces and prevent metal oxidation during soldering, and had been shown to be effective on a range of metals, some of which had been considered unsolderable using conventional fluxes.
Page 1 of 2
More Columns from The European Angle
CircuitData: A New Open Standard for PCB Fab Data ExchangeI Never Realised It Was So Complicated!
The European Angle: Institute of Circuit Technology 43rd Annual Symposium
Ventec International Group's Martin Cotton Celebrates 50 Years in PCB Design
Reporting on the Institute of Circuit Technology Spring Seminar
EuroTech: Raw Materials Supply Chain—Critical Challenges Facing the PCB Industry
EuroTech: ENIPIG—Next Generation of PCB Surface Finish
EuroTech: Institute of Circuit Technology Northern Seminar 2016, Harrogate