-
- News
- Books
Featured Books
- design007 Magazine
Latest Issues
Current IssueProper Floor Planning
Floor planning decisions can make or break performance, manufacturability, and timelines. This month’s contributors weigh in with their best practices for proper floor planning and specific strategies to get it right.
Showing Some Constraint
A strong design constraint strategy carefully balances a wide range of electrical and manufacturing trade-offs. This month, we explore the key requirements, common challenges, and best practices behind building an effective constraint strategy.
All About That Route
Most designers favor manual routing, but today's interactive autorouters may be changing designers' minds by allowing users more direct control. In this issue, our expert contributors discuss a variety of manual and autorouting strategies.
- Articles
- Columns
- Links
- Media kit
||| MENU - design007 Magazine
Estimated reading time: 1 minute
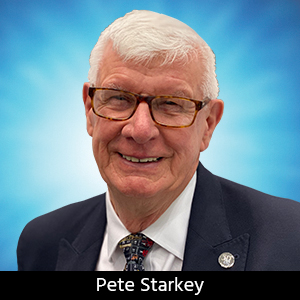
Contact Columnist Form
Glass as an HDI Substrate?
At the EY/IeMRC/ICT joint symposium, New Developments in PCB and Interconnect Manufacturing, held in Rotherham, UK on August 4, 2009, Dr. David Hutt of Loughborough University described work being carried out by his team at Wolfson School of Mechanical and Manufacturing Engineering to investigate the practicability of using glass as an alternative to organic substrates in the fabrication of multilayer interconnects for high-density devices. A space-grade glass, designated CMZ and available in thicknesses of 50 to 150 microns, with expansion coefficient close to that of silicon, had been chosen as the base material. The glass had been machined with a pulsed 248nm Krypton Fluoride excimer laser--using mask projection to produce fine grooves for conductors and waveguides, and microvia holes. Challenges included re-melt, debris, hole taper and microcracking--all minimised by careful process optimisation and the use of a protective film. Electroless copper and electroless nickel had both been successfully deposited onto smooth glass surfaces, and additional testing was ongoing to improve adhesion, using self-assembled APTS monolayers as adhesion promoters. Metallisation of laser-machined areas gave comparatively good adhesion and, if a photoresist was used during laser machining of the conductor pattern, this could act as a mask to define the initial APTS image so that catalyst was attracted selectively to enable full-additive circuit formation. Glass layers had been successfully laminated together without the use of adhesive, by pressure-assisted low temperature bonding, and multilayer interconnects were in prospect.
Click here to see Dr. Hutt's full presentation.
More Columns from The European Angle
CircuitData: A New Open Standard for PCB Fab Data ExchangeI Never Realised It Was So Complicated!
The European Angle: Institute of Circuit Technology 43rd Annual Symposium
Ventec International Group's Martin Cotton Celebrates 50 Years in PCB Design
Reporting on the Institute of Circuit Technology Spring Seminar
EuroTech: Raw Materials Supply Chain—Critical Challenges Facing the PCB Industry
EuroTech: ENIPIG—Next Generation of PCB Surface Finish
EuroTech: Institute of Circuit Technology Northern Seminar 2016, Harrogate