-
- News
- Books
Featured Books
- pcb007 Magazine
Latest Issues
Current IssueThe Hole Truth: Via Integrity in an HDI World
From the drilled hole to registration across multiple sequential lamination cycles, to the quality of your copper plating, via reliability in an HDI world is becoming an ever-greater challenge. This month we look at “The Hole Truth,” from creating the “perfect” via to how you can assure via quality and reliability, the first time, every time.
In Pursuit of Perfection: Defect Reduction
For bare PCB board fabrication, defect reduction is a critical aspect of a company's bottom line profitability. In this issue, we examine how imaging, etching, and plating processes can provide information and insight into reducing defects and increasing yields.
Voices of the Industry
We take the pulse of the PCB industry by sharing insights from leading fabricators and suppliers in this month's issue. We've gathered their thoughts on the new U.S. administration, spending, the war in Ukraine, and their most pressing needs. It’s an eye-opening and enlightening look behind the curtain.
- Articles
- Columns
- Links
- Media kit
||| MENU - pcb007 Magazine
Estimated reading time: 6 minutes
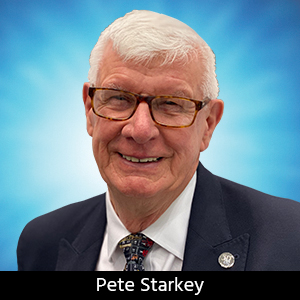
Contact Columnist Form
An Inside Look: Ventec Europe Revisited
Technical Editor Pete Starkey recently had a chance to visit Mark Goodwin, chief operating officer, Europe and USA, for an update on developments at Ventec Europe’s UK Distribution Centre.
Pete Starkey: Hello again, Mark. Time flies! I just checked back and it’s been over six years since I first visited you in Leamington, when you were based at the Sydenham premises. It must be close to three years since you moved Ventec’s distribution operation to the Trojan Business Centre, and I find it really interesting to call-in periodically to keep in touch with your continuing evolution. Last time I was here you were at the final stages of your AS9100C accreditation.
Mark Goodwin: Yes, we have to maintain a balance of priorities--as well as responding to ever-increasing technical demands on laminates and prepregs, we have to make sure the right systems and qualifications are in place to be able to offer quality assurance all the way along the supply chain from our manufacture and distribution to our customers’ PCB shops. Our European operation is now fully accredited to AS9100C, complementing the existing accreditation of Ventec Electronics in Suzhou, and we are in the process of extending the approval to include our North American facilities.
Starkey: Do the aerospace OEMs appreciate what you have achieved?
Goodwin: Not necessarily. They are keen to push AS9100C into the PCB shops, but don’t seem to be putting the same emphasis on material suppliers adopting similar quality philosophies. We are in a unique position among laminators in providing a fully accredited supply chain for high reliability materials, and we are working toward increasing the OEMs’ awareness of what we are able to offer. A big problem is that OEMs tend to write particular brand names and product designations into their drawings and, as time goes on, either be unaware that better materials exist or be unwilling to make any revision, or both--and suffer avoidable problems as a result. This is particularly relevant to the issue of cleanliness.
Starkey: Yes, I sat in on the ECWC World Conference presentation given by Stan Heltzel from the European Space Agency on latent short circuit failure. He showed some quite scary examples! It is clear that ESA see contamination of laminates by foreign material in the dielectric as a major problem, and they are collaborating with key suppliers to mitigate the risk and to define a new procurement specification in the form of Appendix A to IPC-4101-D.
Goodwin: The avoidance of foreign object contamination has been the subject of a major campaign within Ventec for some time now. All the leading manufacturers can formulate good high-reliability materials, but not everyone can make them clean--especially when material thicknesses go below 50 microns. I can show you what investments Ventec Electronics have made in the manufacturing process to eliminate particulate contamination in prepregs and laminates: Superfine filters and magnetic devices, advanced treater technology and clean room management, and the advanced inspection equipment to go with it. I can’t disclose all the details because there are unique proprietary features, but we have demonstrated to the European Space Agency that we can meet their critical requirements, not just at the manufacturing stage, but in cutting, slitting, and packaging for distribution as well. Come and see what investments we are making here in Ventec Europe.
Page 1 of 2
More Columns from The European Angle
CircuitData: A New Open Standard for PCB Fab Data ExchangeI Never Realised It Was So Complicated!
The European Angle: Institute of Circuit Technology 43rd Annual Symposium
Ventec International Group's Martin Cotton Celebrates 50 Years in PCB Design
Reporting on the Institute of Circuit Technology Spring Seminar
EuroTech: Raw Materials Supply Chain—Critical Challenges Facing the PCB Industry
EuroTech: ENIPIG—Next Generation of PCB Surface Finish
EuroTech: Institute of Circuit Technology Northern Seminar 2016, Harrogate