-
- News
- Books
Featured Books
- pcb007 Magazine
Latest Issues
Current IssueInventing the Future with SEL
Two years after launching its state-of-the-art PCB facility, SEL shares lessons in vision, execution, and innovation, plus insights from industry icons and technology leaders shaping the future of PCB fabrication.
Sales: From Pitch to PO
From the first cold call to finally receiving that first purchase order, the July PCB007 Magazine breaks down some critical parts of the sales stack. To up your sales game, read on!
The Hole Truth: Via Integrity in an HDI World
From the drilled hole to registration across multiple sequential lamination cycles, to the quality of your copper plating, via reliability in an HDI world is becoming an ever-greater challenge. This month we look at “The Hole Truth,” from creating the “perfect” via to how you can assure via quality and reliability, the first time, every time.
- Articles
- Columns
- Links
- Media kit
||| MENU - pcb007 Magazine
Estimated reading time: 15 minutes
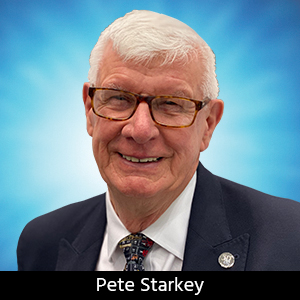
Contact Columnist Form
SMART Group Seminar: Harsh Environments & Electronics
Conformal coatings had historically been applied for protection against these conditions, but the question remained whether conformal coatings and their associated test standards had kept up with the conditions of modern day harsh environments. Although purchase specifications could call-up a range of international, national, government and trade association standards, more and more in-house company standards were being published with increasingly severe environmental conditions, and sequential testing was becoming frequently specified for both unloaded test boards and production boards. A typical company sequential test procedure might include: thermal shock, followed by damp heat cyclic, followed by first thermal cycling, followed by corrosive gases, followed by damp heat constant, followed by second thermal cycling, followed by salt spray test, followed by long-term high temperature, followed by final inspection.
How were the suppliers of conformal coatings responding to these new challenges? New coatings were being developed and Greenman quoted examples of UV curable coatings that looked and behaved like silicones, but were not silicone, synthetic rubber coatings with extreme flexibility and high-temperature performance, and new UV cure silicones that overcame the high slump ratio of thermal cure silicones. And these coatings were being tested to the extremes of all of the specifications currently published or proposed.
The seminar had provided, in logical succession, the expert views of the laminate supplier, the PCB fabricator, the researcher into novel joining methods, the solder supplier and the conformal coating supplier. It remained for Ian Fox from Rolls Royce Controls and Data Services to tie it all together from the point of view of an avionics OEM whose safety-critical products were required to work in close proximity to aero engines. His wrap-up presentation was entitled "Harsh Environment Electronics: Materials and Making it Work." Typical examples of harsh environment conditions were high or extremely low temperatures, high humidity, and corrosive atmospheres. He first considered the effects of high temperatures on components: The maximum storage temperature for conventional semiconductors was 150ºC, although many would operate up to 175ºC with some possible degradation in performance and reduction in lifetime. To achieve useful life above 200ºC, devices based on silicon-on-insulator were required, and for temperatures above 300ºC there were very few options. One was to use devices based on silicon carbide but these were very expensive and of limited availability.
For soldered assemblies at operating temperatures above 150ºC, the properties of eutectic tin-lead were significantly degraded, the solder was extremely plastic and its fatigue resistance was low. Changing the alloy to tin-silver (SnAg4) or tin-antimony (SnSb5) gave satisfactory performance at temperatures up to 175ºC. Modern phenolic based FR4 printed circuit laminates with 180ºC glass transition temperature were acceptable for operation at 150ºC, but higher temperatures required the use of polyimide. For operating temperatures in the range 175-225ºC, high-lead solder alloys Pb95Sn5 and Pb93.5Sn5Ag1.5 were commonly used, although their wettability was limited. At high soldering temperatures, flux degradation was very rapid and inert or reducing atmospheres were recommended. Ian considered that vapour-phase soldering was preferable to convection reflow.
Page 6 of 7
More Columns from The European Angle
CircuitData: A New Open Standard for PCB Fab Data ExchangeI Never Realised It Was So Complicated!
The European Angle: Institute of Circuit Technology 43rd Annual Symposium
Ventec International Group's Martin Cotton Celebrates 50 Years in PCB Design
Reporting on the Institute of Circuit Technology Spring Seminar
EuroTech: Raw Materials Supply Chain—Critical Challenges Facing the PCB Industry
EuroTech: ENIPIG—Next Generation of PCB Surface Finish
EuroTech: Institute of Circuit Technology Northern Seminar 2016, Harrogate